1. 引言
Al-Mg-Si系是一类可热处理强化合金,由于其较高的比强度、优异的成形性能、良好的可焊性及耐腐蚀性能,是轨道交通装备、汽车工业及建筑领域主要的轻量化材料 [1] [2] [3] 。Al-Mg-Si系合金主要强化机制为析出强化,一般认为其时效析出序列为:过饱和固溶体 → G.P.区 → β''相 → β'相 → β相 [4] [5] 。其中β''相为该系合金最主要的强化析出相,在峰值时效状态(T6) β''相大量析出、分布弥散,合金获得最高的强度,但其耐腐蚀性能则较过时效状态差,因此析出相的析出行为不仅显著影响合金的力学性能,而且对其耐腐蚀性能也产生显著影响 [6] [7] 。因而,调控析出相的析出行为,使合金强度和耐腐蚀性能得到最优匹配,是获得高综合性能Al-Mg-Si合金的重要手段。
近年来,针对Al-Mg-Si合金性能的调控机理与方法已有大量文献报道。文献 [8] [9] 研究固溶、时效制度对Al-Mg-Si合金力学性能及腐蚀性能的影响,同时改善了合金力学性能与晶间间腐蚀敏感性;这些工作均通过优化时效工艺的方法调控合金时效析出行为,优化了合金综合性能。然而,这些工作仅从时效过程中纳米析出相析出行为的角度针对合金析出行为进行直接调控,并未考虑合金本身晶粒组织或亚结构对合金析出行为的影响。
因此,为了更直观地研究合金晶粒组织(包括晶粒组织或亚结构等)对Al-Mg-Si系合金力学性能和耐腐蚀性能的影响,本工作通过调控6XXX系铝合金处理工艺,制备了3种不同晶粒组织结构的Al-0.5Mg-0.6Si合金,采用拉伸性能、晶间腐蚀、电子背散射衍射及透射电镜等研究方法,研究了晶粒组织对力学性能及耐晶间腐蚀性能的影响。以期为该系列合金组织与性能调控方法的工程化应用提供有益参考。
2. 试验材料与方法
试验材料为某企业生产的10 mm厚Al-Mg-Si挤压型材,其合金成分如表1所示。在型材上切取多块试样,分为3组。第一组试样为10 mm厚挤压型材冷轧至3 mm,再在535℃下固溶1 h后,立即采用室温水淬火,获得完全再结晶组织,为便于描述,将改组试样记为A组;第二组试样为10 mm厚挤压型材在535℃下长时间(24 h)固溶,随后淬火,记为B组;第三组试样直接取型材中心层3 mm,在535℃下保温1 h后淬火,记为C组。
制备出3种不同晶粒组织结构的试样后,均按180℃/7 h进行人工时效处理,所得的3种试样的晶粒组织特征分别为等轴状的完全再结晶组织、细小的部分再结晶晶粒组织及以挤压变形组织为主的挤压纤维晶粒组织,这三种试样的典型金相组织照片分别如图1所示。
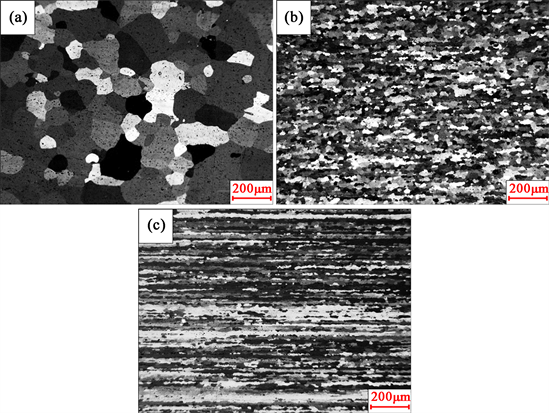
Figure 1. Optical microstructures of the different samples: (a) sample A; (b) sample B; (c) sample C
图1. 不同试样的金相组织:(a) A试样,(b) B试样,(c) C试样
依次将A、B、C合金3种不同晶粒组织结构的试样进行机械抛光,随后按照GB/T 3246.1-2012《变形铝及铝合金制品组织检验方法第一部分:显微组织检验方法》标准所述的方法对试样进行阳极覆膜处理。金相显微组织的观察在OLYMPUS BX51M型偏光金相显微镜下进行,并分别对试样进行多个视场进行金相组织观察。室温拉伸试验按GB/T 228.1-2010《金属材料拉伸试验第一部分:室温试验方法》所述的方法在DDL-100万能电子试验机上进行,试样标距为50 mm,拉伸速度约为2 mm/min。晶间腐蚀性能测试参考GB/T7998-2020《铝合金晶间腐蚀测定方法》中所述试验方法,将试样在35℃恒温57 g/L氯化钠和10 mL/L过氧化氢溶液体系下浸泡24 h后,采用金相显微镜观察试样的腐蚀特征并测试其最大腐蚀深度。
采用电子背散射衍射技术(EBSD)分析3种试样晶粒组织及亚结构的详细特征。EBSD试样分别经机械抛光、电解抛光后,在ZEISS-EVOM10型电镜下进行采集,采集步长为0.8 μm。
采用透射电镜观察3种不同晶粒组织结构的试样晶内、晶界上析出特征,试样分别经机械减薄、人工减薄至约70 μm厚,随后进行电解双喷,双喷电解环境为30% HNO3+ 70% CH3OH溶液,温度控制在−30℃左右,试验在FEI TECNAI G2 20上进行,加速电压为200 kV。
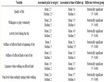
Table 1. Chemical compositions of the experimental alloys
表1. 试验材料的化学成分
3. 研究结果
3.1. 微区晶粒组织
图2为不同试样晶粒组织的EBSD分析结果。从图中可见,3种试样的晶粒组织可见显著的差异,A试样为粗大的等轴状完全再结晶组织,B试样为晶粒较为细小但保留了部分亚晶组织的部分再结晶组织,C试样中存在大量亚结构和较多的变形组织。将3种试样的再结晶分数及平均晶粒尺寸进行统计,所得结果如图3所示,从图中可见,A试样再结晶分数约95.2%,其平均晶粒尺寸约173.1 μm;B试样再结
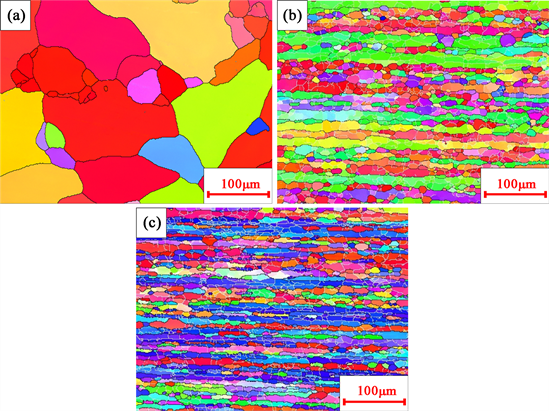
Figure 2. EBSD characterizations of the different samples: (a) sample A; (b) sample B; (c) sample C
图2. 不同试样EBSD分析结果:(a) A试样;(b) B试样;(c) C试样
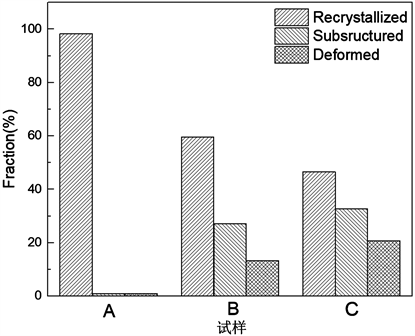
Figure 3. Grain structures of the different samples
图3. 不同试样的晶粒组织结构
晶分数约59.6%,变形组织分数约为13.5%,平均晶粒尺寸约16.2 μm;C试样再结晶分数约46.5%,变形组织分数约为19.7%,平均晶粒尺寸约10.2 μm。
3.2. 透射电镜显微组织
图4为3种不同晶粒组织试样在[001]带轴下晶内析出相组织,从图中可见,三者晶内均观察到大量的呈针状的析出相,其中A试样中析出相的约105.3 nm,分布较为稀疏,B试样析出相尺寸约56.4 nm,其分布较A试样密集;而C试样析出相尺寸最小,约43.2 nm,分布也最为密集。此结果表明,基体晶粒组织特征对晶粒内部纳米级析出相尺寸和分布存在显著影响。图5所示为3种不同试样晶界附近的透射电镜显微组织。从图中可见,3种不同试样晶界处均未观察到析出相衬度,但晶界周围均可见明显的无沉淀析出区(PFZ),3者晶界处的析出特征无明显差异。
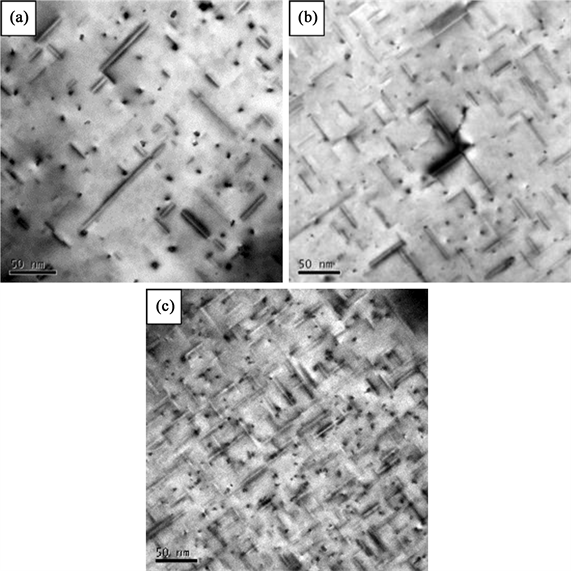
Figure 4. TEM images of precipitation of the samples: (a) sample A; (b) sample B; (c) sample C
图4. 不同试样的透射电镜显微组织
3.3. 力学性能
图6为3种不同晶粒组织试样人工时效后的拉伸性能结果。从图中可见,3中不同晶粒组织的试样力学性能表现出显著的差异,其中,完全再结晶的A试样,抗拉强度261.7MPa、屈服强度250.5 MPa,部分再结晶试样B相较于A试样,抗拉强度提高高27 MPa、屈服强度17.6 MPa,而保留挤压纤维组织的C试样强度最高,其抗拉强度和屈服强度较A试样分别提高了44.7 MPa、33.7 MPa。就断后伸长率而言,B试样最高,为16.2%,较伸长率最低的完全再结晶试样A试样提高40%。
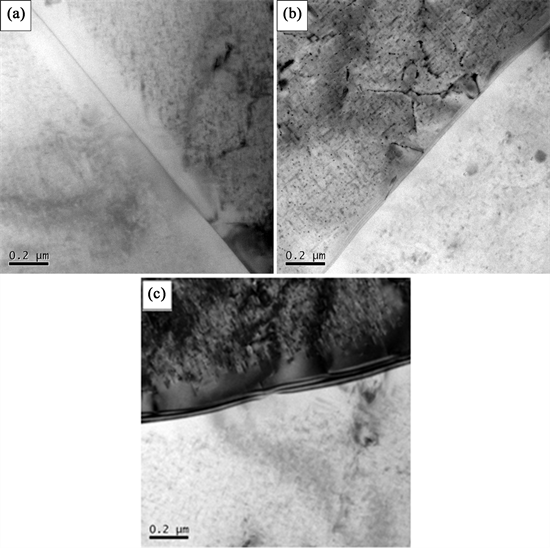
Figure 5. TEM images of precipitation of the samples on GB: (a) sample A; (b) sample B; (c) sample C
图5. 不同试样晶界处析出相的透射电镜显微组织:(a) A试样;(b) B试样;(c) C试样
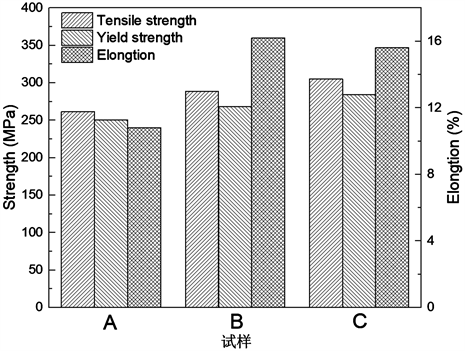
Figure 6. Mechanical properties of the different samples
图6. 不同试样的力学性能
3.4. 耐晶间腐蚀性能
图7为3种不同试样的晶间腐蚀检测结。从图中可见,3种试样的晶间腐蚀深度有显著差异。完全再结晶试样A仅观察到微弱的晶间腐蚀,其最大腐蚀深度26.7 μm,而B试样存在局部腐蚀现象,同时可见明显的网状晶界,其最大腐蚀深度约82.4 μm;C试样发生较为严重的晶间腐蚀,大量晶粒从试样上脱落,其腐蚀最大深度约113.7 μm。此结果表明,晶粒组织结构对晶间腐蚀存在显著的影响。
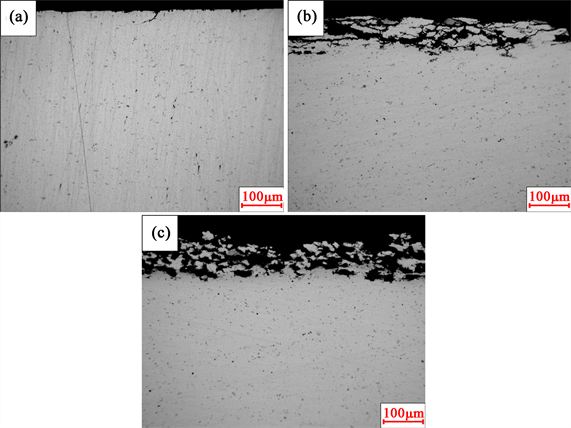
Figure 7. Intergranular corrosion morphology of the samples with different grain structures: (a) sample A; (b) sample B; (c) sample C
图7. 不同试样的晶间腐蚀形貌:(a) A 试样,(b) B试样,(c) C试样
4. 分析与讨论
合金的强化机制主要包括细晶强化、固溶强化、析出强化和位错强化等 [10] [11] 。对于本文所用的Al-Mg-Si合金来说,对合金强度具有重要贡献的机制为细晶强化、析出强化等,其中析出强化是对强度贡献最大的强化机制。在本文的试验条件下,3种试样晶粒尺寸和晶粒组织构成不同,这种差异首先引起了细晶强化效应的差异,即晶粒尺寸最大的A试样细晶强化效果最弱。其次,由于析出相的析出动力学行为与材料内部晶界、亚晶界、位错及空位等高能量缺陷有关,这主要是由于这些高能量的缺陷为合金析出相提供了形核位置,而在相同的时效制度下,形核位置的数量显著影响析出相的尺寸、分布等。因此,从图4中可见,亚结构和变形组织含量最高的C试样,其析出相尺寸最细小分布最密集,相应地其强度最高;而完全再结晶组织的A试样,析出相尺寸最大分布最稀疏,因而其强度最低。
一般认为 [10] [11] [12] ,合金晶间腐蚀敏感性与晶界析出相的分布及晶界附近的无沉淀析出区(PFZ)显著相关。晶界析出相或PFZ与基体之间存在电位差,在腐蚀环境中容易形成腐蚀微电偶诱发阳极溶解,从而引发晶间腐蚀。然而,在本文的试验条件下,3种试样均表现出相同的晶界析出特征(如图5所示),而晶间腐蚀深度存在显著差异(如图7所示)。此结果表明,晶间腐蚀深度与晶界析出特征并无显著关联性。
作者前期研究结果表明 [13] ,在Al-Mg-Si合金中大角度晶界上未观察到析出相,而在小角度晶界上可见明显呈连续分布的Mg-Si原子偏析带,如图8[13] 所示。大角度晶界的观察结果与本文对3种试样晶界处的观察结果相吻合。本文试验材料的成分、热处理工艺、晶粒组织等均与文献 [13] 基本一致,因而其析出特征应该与文献 [13] 所述的结果一致。虽然这种析出特征的机理目前未见文献报道,但仍可用于解释本文3种合金晶间腐蚀的差异。如图2、图3所示B、C合金内部存在大量小亚晶组织(小角度晶界),这些小角度晶界应该是影响合金耐腐蚀性能的一个主要因素。此外,文献 [12] 表明,材料内部变形储能越大,越容易引发腐蚀。从本文的结果来看,由于A试样为粗大的完全再结晶晶粒组织,其变形储能几乎完全释放,而B试样和C试样中,存在较多变形组织,因此B、C试样的耐蚀性能较差。综上所述,晶粒组织中亚结构、变形组织含量最高的B试样,其晶间腐蚀深度最大。
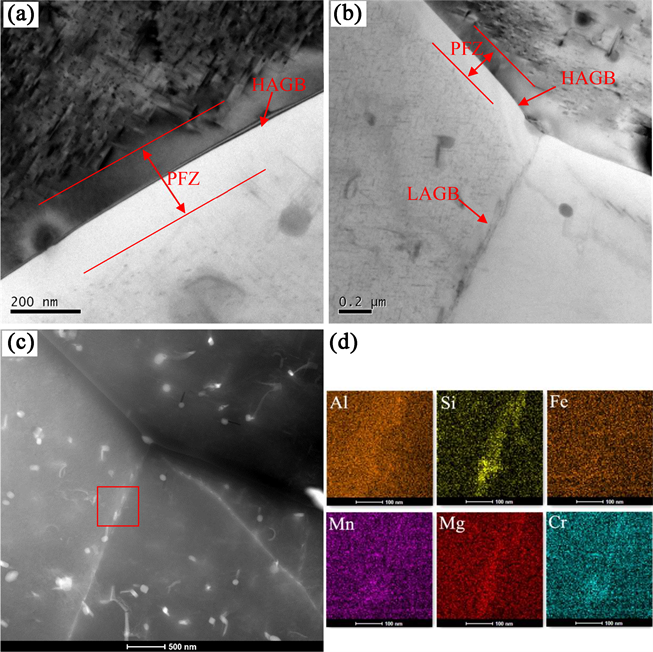
Figure 8. [13] Precipitation morphology of HAGB and LAGBs in Al-Mg-Si alloys: (a) HAGB; (b) LAGB; (c) STEM micrograph of (b), (d) corresponding EDX-Mapping of the selected area in (c)
图8. [13] Al-Mg-Si合金中大小角度晶界析出相形貌:(a)大角度晶界;(b)小角度晶界;(c)图(b) STEM形貌;(d)图(c)中小角度晶界选区的EDX-Mapping
5. 结论
本文通过EBSD、TEM等晶粒组织的分析,研究了3种不同晶粒组织的Al-Mg-Si合金力学性能和耐晶间腐蚀性能,得到如下结论:
1) 在本文试验条件下,Al-Mg-Si合金中亚结构和变形组织作为析出相形核的优先位置,显著细化了析出相尺寸,同时使得析出相分布更为密集,显著提高了析出强化效应,因而粗大等轴状再结晶组织的A试样强度最低,而晶粒尺寸最小、亚晶含量最多的C试样与A试样相比,强度提高约35 MPa。
2) 在本文的试验条件下,亚结构和变形组织是影响3种晶粒组织的Al-Mg-Si合金试样耐蚀性能的主要因素。亚结构、变形组织含量最高的B试样,其晶间腐蚀深度最大。其机理在于Al-Mg-Si合金中小角度晶界上存在呈连续分布的Mg-Si原子偏析带、变形组织携带的变形储能等因素促进了晶间腐蚀的发展。
NOTES
*通讯作者。