1. 引言
氚气是一种纯β发射的放射性气体,其产生的β射线可以激发荧光粉发光,用此原理制备的氚光源无需外加电源、无需维护、使用寿命长,且不受气候环境及油、水、酸等腐蚀介质的影响 [1] 。目前,大尺寸氚光源在矿井、隧道、仓库、机场等地方用于标识 [2] 及照明,尤其在极端环境或易燃易爆的场景下,与有电光源相比具有更大的优势;小尺寸氚光源在轮船、飞机仪表盘、手表、枪械瞄准器具 [3] 等领域更是具有无可替代的作用。
在所有氚光源的形式中,管式气态氚光源的应用最为广泛 [4] 。传统的制备方法通常采用浆料旋涂法 [5] ,以聚环氧乙烷等有机物为粘结剂,为使浆料均匀稳定,通常会加入多种添加剂,通过高温烤管去除这些成分 [6] 。由于各种辅助材料经过高温会残留微量灰分,造成碳沉积,且高温过程中荧光粉与各种杂质气体接触受到污染,这些会影响涂层的发光性能 [7] 。
为了避免浆料旋涂法的上述缺点,本研究采用干粉法制备氚光源的荧光粉涂层。该方法以磷酸为粘结剂、丙酮为溶剂,先在玻璃管内表面涂覆粘结剂溶液,再喷涂干的荧光粉,之后经过加热干燥,得到所需的发光涂层。
干粉法制备发光涂层的过程中,不同浓度的粘结剂溶液可以制备出质地不同的发光涂层,但浓度差异也会造成溶液其他性质的差异,其干燥工艺也不相同。本研究分别使用低浓度粘结剂和高浓度粘结剂制备涂层,在不同温度和程序下干燥固化,通过测定涂层厚度、观察表面形貌和分析元素比例,确定干粉法制备涂层的干燥工艺。
2. 实验部分
2.1. 试剂及仪器
试剂:ZnS荧光粉:北京化工厂;磷酸:国药集团化学试剂有限公司,分析纯;丙酮:国药集团化学试剂有限公司,分析纯。仪器:自搭建旋转喷涂机;WGLL-125BE鼓风式干燥箱:天津泰斯特有限公司;SX-5-12型箱式电阻炉:弗恩森(北京)电炉有限公司;JSM-7600F场发射扫描电子显微镜:德国卡尔蔡司股份公司。
2.2. 低浓度磷酸制备发光涂层
配置低浓度的磷酸–丙酮溶液,将溶液涂覆在玻璃管内壁,垂直悬挂使其形成一层均匀的液膜,向液膜喷涂荧光粉。分别在200℃至500℃之间加热干燥,吹扫表面浮粉,得到所需发光涂层。
2.3. 高浓度磷酸制备发光涂层
配置低浓度的磷酸–丙酮溶液,将溶液涂覆在玻璃管内壁,垂直悬挂使其形成一层均匀的液膜,向液膜喷涂荧光粉。一组涂层直接在高温环境干燥,另一组先在鼓风干燥箱中低温干燥,再升温烘烤。之后吹扫表面浮粉,得到所需发光涂层。
2.4. 表征方法
将带涂层的玻璃管环切,在扫描电镜下观察其剖面,随机选择测量点,测定涂层的平均厚度。
将带涂层的玻璃管纵向切割,在扫描电镜下观察涂层的表面形态、附着物情况。使用EDS能谱扫描涂层表面元素。
3. 结果与讨论
3.1. 低浓度磷酸制备发光涂层
为了确定涂层固化所需的最佳温度,分别在200℃到500℃之间对涂层进行干燥固化。之所以选择200℃以上的温度,是因为涂层固化的主要反应是浓磷酸与玻璃在200℃以上的反应,该反应生成杂多酸,将涂层与玻璃粘接在一起。此外还会发生少量的磷酸与荧光粉表层反应,其产物将荧光粉颗粒相互粘接,得到具有一定厚度的发光涂层。
每个温度下的样品都反应足够长的时间,经过刮擦测试,荧光粉涂层均得到充分干燥。之后在扫描电镜下观察,结果如图1所示,200℃到400℃之间制备的发光涂层,其荧光粉颗粒表面覆盖了一层晶体,尤其以250℃到350℃之间晶体最多;400℃以上的涂层,其表面的片状晶体逐渐减少,有粉末状物质产生。
关于片状晶体与粉末状物质,由于所有样品能谱扫描得到的元素比例S:Zn均小于1,且实验过程中出现了硫化氢气体的刺激性气味,确定该物质是加热干燥过程中磷酸与硫化锌反应生成的磷酸锌。当温度较低时,磷酸与玻璃反应的速度相对较慢,从而有更多的磷酸与荧光粉反应生成磷酸锌,且溶剂蒸发的速度也较慢,磷酸锌有较充足的时间结晶,产生相对完整的晶体结构,电镜下就能观察到片状的晶体。此处所述的“较慢”,实际上依然是很短暂的时间,荧光粉表面的片状结晶也很微小,其直径约为1 μm,厚度仅有100 nm左右。若温度剧烈升高,溶剂会在极短时间内蒸发掉,就来不及形成片状晶体。
使用EDS能谱扫描了不同反应温度下荧光粉表面元素的原子数量比,如表1所示。反应未开始前,S元素与Zn元素的原子数量之比应为1,之后由于硫化氢气体逸散,涂层体系内S元素减少,Zn元素不变,S元素与Zn元素的原子数量之比小于1。磷酸与玻璃的反应不会影响S元素与Zn元素的比例,两种元素比例的变化完全是因为磷酸与荧光粉的反应。荧光粉表面的S/Zn数值越小,说明磷酸锌晶体层越厚,覆盖了下方的硫化锌荧光粉颗粒,可能会阻碍β射线激发荧光粉,从而降低涂层的发光性能。
根据表1可知,400℃及以上的涂层S/Zn > 0.93,与350℃及以下的涂层相比有显著提高,说明400℃及以上的温度更适合控制固化反应。扫描电镜下的图片显示,400℃涂层表面有少量片状晶体,450℃及500℃的涂层表面未观察到片状晶体,因此综合考虑450℃为涂层固化的适宜温度。
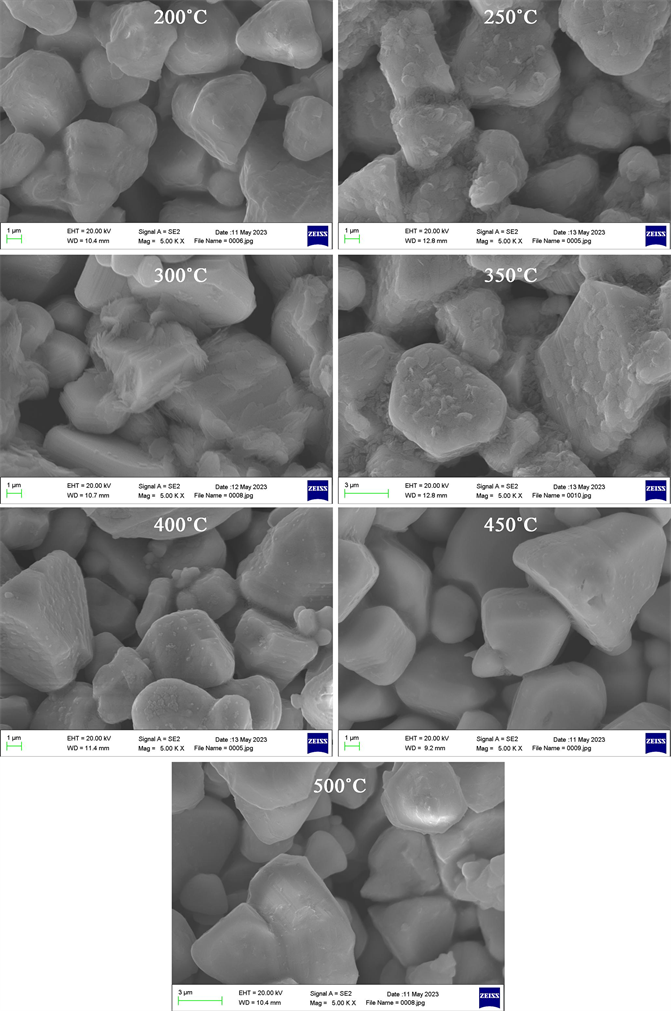
Figure 1. Surface morphology of phosphor coatings obtained at different reaction temperatures
图1. 不同反应温度所得涂层的表面形貌
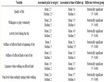
Table 1. Atomic ratios of elements on the surface of phosphor coatings obtained at different reaction temperatures
表1. 不同反应温度所得荧光粉表面元素的原子数量比
3.2. 高浓度磷酸制备发光涂层
由2.1所述粘结剂发生固化反应的最佳温度为450℃,使用高浓度磷酸溶液制备涂层时,相同的干燥工艺得到的涂层有明显缺陷,如图2所示。扫描电镜下观察所得涂层,发现涂层中出现较多小气泡。考虑到涂层固化的过程可能同时伴随溶剂的气化逸散,且这两个过程发生的先后顺序与温度有关,并影响涂层质量。如图3所示。高浓度磷酸溶液与低浓度磷酸溶液的一个显著区别在于,高浓度磷酸溶液的黏度很高,溶液体系内分子间作用力较大。与低浓度溶液相比,高浓度溶液中溶剂分子更难扩散和挥发。而将涂层突然置于高温环境下,表层溶液最先受热开始反应,进一步阻碍了溶剂分子的扩散,内层的溶剂来不及逸散就被混合物包裹在内部,受热气化后形成气泡。如果在高温之前增加低温阶段,可能使溶剂充分逸散,避免气泡形成。
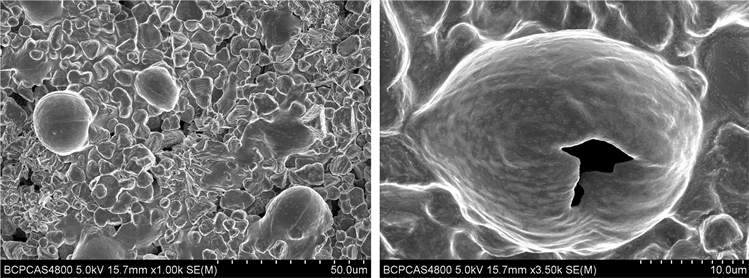
Figure 2. Bubbles in the phosphor coatings
图2.荧光粉涂层出现气泡
为了验证上述假设,制备出平整无缺陷的涂层,采用两步法进行涂层干燥。将完成荧光粉喷涂的玻璃管置于鼓风式干燥箱中进行溶剂脱除。由于市售磷酸含有一定量的水,涂层中的溶剂为丙酮和水的混合溶剂,为了加快溶剂脱除同时避免固化反应大规模发生,将溶剂脱除的温度暂定为90℃。保温30 min后,在马弗炉中450℃烘烤固化。使用扫描电镜观察涂层表面形态,如图4所示,涂层平整致密,没有气泡及其他缺陷,说明上述假设成立,且先90℃烘干30 min再高温烘烤的干燥工艺,适用于高浓度磷酸溶液制备涂层。
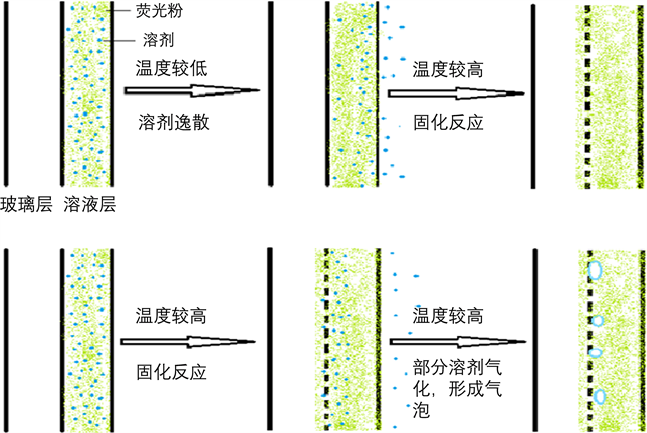
Figure 3. The curing process of the coating and the cause of the appearance of the bubbles
图3. 涂层固化过程及气泡出现原因

Figure 4. Surface morphology of the coating obtained by two-step drying
图4. 两步法干燥所得涂层表面形貌
低浓度粘结剂与高浓度粘结剂制备出的涂层,在厚度和透气性两方面具有较大差异。如图5所示,低浓度粘结剂制备出的涂层,由于粘结剂含量较少,其结构较为疏松,荧光粉颗粒之间仅有少量粘结剂相连,有较大孔隙,氚气可以进入涂层内部激发内部荧光粉;高浓度粘结剂制备出的涂层结构致密,表面平整,粘结剂填充了荧光粉颗粒的间隙,导致孔隙较少。两种涂层的厚度分布如表2所示,高浓度粘结剂制备出的涂层,厚度可控范围更大。
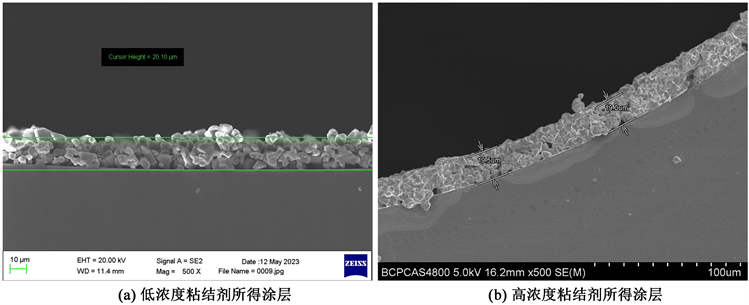
Figure 5. Cross profiles and thicknesses of phosphor coatings obtained with different concentrations of binder solutions
图5. 不同浓度粘结剂所得涂层剖面及厚度
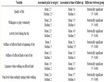
Table 2. Range of controllable thickness of phosphor coatings obtained from binder solutions at different concentrations
表2. 不同浓度粘结剂所得涂层厚度可控范围
4. 结论
干粉法制备氚光源的发光涂层过程中,高浓度粘结剂和低浓度粘结剂对应的干燥工艺有所不同。粘结剂浓度较低时,直接在450℃高温烘烤即可;粘结剂浓度较高时,应选择两步法进行干燥,即先在90℃低温烘干30 min,之后在450℃固化涂层。
明确高浓度粘结剂和低浓度粘结剂制备涂层的干燥工艺,可以得到不同厚度、不同透气性的发光涂层,对后续继续开展其他相关研究是十分必要的。