1. 引言
电火花线切割(WEDM)简称线切割。所谓的线切割就是利用钼或铜等金属细丝作为电极,通过电极丝的连续移动,并对工件进行脉冲火花放电,从而达到通过放电蚀除金属,使工件切割成型的目的。利用电火花线切割加工电极丝比较细,对于厚度较小的薄板加工精度较高等特点,可在加工模具、工件样板和精密仪器中应用,并能取得较好的加工效果。另外邱明波等人 [1] 利用双线电火花线切割电解复合加工技术对太阳能硅片进行切割及制绒处理。实验表明,采用此方法对太阳能硅片进行加工,具有效率高、厚度薄、切缝窄的特点,并且可以直接获得绒面结构,无明显裂纹 [2] 。电火花线切割加工技术可以有效解决加工材料的脆度、硬度和强度对加工工艺的影响,在加工中可取得比较理想的效果。在使用过程中,产生质量最大的问题就是断丝,使加工过程中断。重新穿丝会影响生产效率,使加工工件精度变低,甚至会造成工件报废。
2. 断丝原因
发生断丝的因素主要有电极丝特性、电极丝运行异常、工作液浓度异常、电参数选用不合理、工件材质特性、与加工工艺等原因。但电火花线切割加工中电极丝断丝的根本原因只有电极丝承受的轴向载荷超过电极丝的极限强度,拉断电极丝和放电瞬间热负荷过大,烧断电极丝 [3] 。
2.1. 拉断原因分析
从力学角度分析电极丝被拉断主要因为轴向应力太大和电极丝强度太低。在电火花线切割机床运行过程中,施加在电极丝上的力大致可以分为放电时因电流产生的电磁力和放电过程施加电压产生延迟点火产生的静电力,以及工作液流动产生的流体动力等。当以上力作用在电极丝就会引起电极丝振动。加工过程中电极丝振动产生的附加弯矩力。显然,电极丝振动振幅越大,其动态轴向力越大,越容易断丝。为了减小电极丝振动常用方法即使增加电极丝张紧力。张紧力增加的同时电极丝轴向静态力也会同时增大,同样有拉断电极丝风险。
在满足加工要求的前提下选用电极丝的直径越大所能承受轴向拉力越大。一方面可提高电极丝的拉断力(如表1所示),减少电极丝的抖动,承受电流大,可采用较强的电流进行加工,提高输出的脉冲能量,提高整体加工效率;另一方面工电极丝直径越大切割缝隙越大,作液容易渗入切割缝隙,有利于排出电蚀产物。
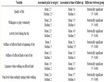
Table 1. The minimum tensile force of several kinds of molybdenum wire diameter
表1. 几种直径钼丝的最小拉断力
所以在加工过程中一定要选用合适规格的电极丝与合适的数量的张力重锤配重块。否则会在加工过程中因拉力过大而产生断丝现象(配重块的选择请参考图1)。
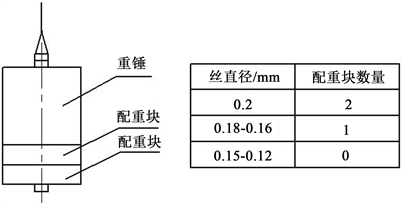
Figure 1. The relationship between counter weight and the diameter of molybdenum wire
图1. 钼丝直径与配重块关系
2.2. 烧断原因分析
电火花线切割是利用连续移动的电极丝(铜丝或钼丝)作为工具电极(连接高频脉冲电源的负极),对工件(连接高频脉冲电源的正极)进行脉冲火花放电腐蚀、切割加工。其加工放电(单次脉冲电火花放电)的微观过程都是热(主要是表面热源)和电动力、电磁力、热动力以及流体动力等综合作用的过程。这个过程大致可分为四个阶段:电极和工件之间产生电离层通道(两电极间绝缘介质分解);火花产生使工件材料融化或气化并分解(过程中电极丝有轻微损耗);切断电流并引起火花的内爆;使用电介质液冲洗清除金属颗粒及杂质(放电间隙恢复绝缘)。
如果在加工过程中电极之间放电能量过大就容易烧断电极丝。此种情况下就应适当降低放电脉冲宽度,降低脉冲电流等办法减少电极之间放电能量以减小断丝概率。但此种方法会降低加工效率。
2.3. 正常断丝
在正常加工过程中,其他原因排除的情况下。随着加工工件数量及时间的增加,虽然能正常完成加工,但电极丝会逐渐变细,电极丝不断地磨损消耗。加工中由于放电腐蚀导致电极丝损耗,随着时间的累加,达到极限尺寸不能承受能量负荷及应力载荷而断丝 [4] 。这种情况不能重新穿丝,继续加工。而是需要更换电极丝。
以快走丝线切割常用的电极丝径0.18 mm规格的钼丝为例,正常断丝情况下钼丝直径大概下降为0.12~0.13 mm。
3. 影响断丝因素
3.1. 因工作液而产生的断丝的情况
线切割的工作液具备冷却、洗涤和对电极丝镀覆能力 [5] 的作用,同时因为是放电加工。就要求这种液体能够有较好的电化学作用,有一定的电绝缘性,防止金属表面锈蚀。
此处以皂化工作液为例。在快走丝线切割对工件进行加工的时候,要选择质量较好的皂化工作液进行加工工作,同时必须保证调配工作液的水质要好。根据加工工件所要达到的质量要求,把工作液配置成不同的比例。工作液的浓度一般在5%到20%之间。浓度的高低要根据切割速度的高低来配制。如果要求切割的速度比较高,或者加工的工件比较厚,那么就可以把工作液的比例配制在1%至8%左右。这样加工起来就会比较稳定。如果加工的工件对质量要求比较高,那么可以把工作液配制在10%到20%之间。工作液在使用八至十天之后,一般要更换新的工作液。如果在加工中工作液浓度选择不合适,那么电极丝在放电时电极丝上会产生的异常放电坑。放电坑周围的分散状裂纹会异于正常的增大。损耗大的电极放电坑较深。另外由于在不合适的工作液中电极丝镀覆能力变差,电极丝得不到应有的修复,极易在放电坑周围的应力集中处产生裂纹。高速走丝时电极丝在加工中受到单向应力作用,该作用使微裂部分不断扩展,最终导致断丝。选择合适比例的工作液,并且做到及时对工作液进行更新,可以减少断丝情况的出现。
3.2. 因为工件材料性质引起的断丝的情况
电火花线切割加工过程中还会因为工件材料存在加工应力、淬火应力、内部夹渣、工件未消磁等原因而造成断丝。
在线切割加工经过锻打淬火的金属材料时,如果没有消除材料内应力,在线切割加工过程中极易因材料原因产生的收口变形,从而发生夹丝情况,进而致使断丝情况出现。如果是未淬火,而是存在加工应力的材料。在线切割加工中则大多会形成张口变形。在发生形变的过程中极易发生材料变形造成弹丝的情况发生。这种情况下也极容易断丝。面对上述情况对于锻打淬火材料,我们可以用多次回火的上方法去除材料内应力。非淬火且存在加工应力的金属材料在线切割加工中我们可以通过打孔然后穿丝的加工方式来控制腔体工件的材料形变。如果以上加工方法均不理想的情况下。我们还可以通过多次加工来消除材料内应力,用以达到材料成型后的稳定性。
在切割铸造类工件时也要时刻注意。因为此类工件在铸造过程中可能存在砂眼、气孔或导电率低的杂质。切割过程中遇到此类情况时,杂质会因其未与金属同时融化而凸显出来造成与电极丝摩擦拉扯,导致断丝情况发生。此种情况发生后可以通过放大脉宽与脉间,同时降低切割速度,以求利用火花放电将切缝路径上的杂质高温熔融或气化。或者编制一段在放电过程中反复进退(0.5~1 mm范围以内)的程序,并在切割过程中加大工作液流量。以达到在反复切割过程中工作液可以将杂质冲刷出来目的,并达到恢复正常切割的状态。
在线切割加工中,很多情况是前期经过多道工序后才开始进行线切割加工。很多加工方式加工后的金属工件内会残余磁性。工件残余磁性就会导致在线切割加工过程中切割缝隙因为金属残屑或氧化物堵塞造成放电稳定性变差,引起断丝。此种情况可在线切割加工前对工件退磁。
由线切割加工原理,我们可知线切割在加工过程中的放电间隙阶段会产生高温氧化作用。在这一过程中有一部分工件材料氧化物会因为镀覆效应黏附在电极丝上。一般金属材质氧化物为导电物质,放电间隙状态良好,而加工铝及铝合金材料时,铝材的金属氧化物是陶瓷性物质,导电性下降,出现工件切不动、断丝、导电块反而消耗快的问题 [6] 。此种情况下我们就应及时更换导电块以保证加工状态的正常。
3.3. 因电参数引起的断丝的情况
线切割加工中电参数的选择十分重要。电参数的选择直接影响加工过程中工件粗糙度、工件尺寸精度以及切割速度与电极丝寿命。这里的电参数包含放电脉冲时间(脉宽)、放电脉冲间隙时间(脉间)、脉冲峰值电流、矩形脉冲与分组脉冲的选择、空载电压、走丝速度。
其中脉冲峰值电流和空载电压大小是直接影响放电脉冲能量大小的因素之一。固定长度的放电脉冲时间脉冲内峰值电流越大,在此放电脉冲时间内释放的能量越大,同时对工件电蚀效率也就越大。但是固定长度的放电脉冲时间脉冲内峰值电流和空载电压过大的情况下,则会出现切割速度加快工件表面粗糙度变大,电极丝损耗量增大,导致断丝。
在其他放电参数固定不变的情况下,放电脉冲时间和放电脉冲间隙时间的选择则是直接影响加工效率和加工质量的直接因素。放电脉冲时间直接影响单个放电脉冲能量,放电脉冲间隙时间则直接影响放电脉冲的放电的频率,两者都对加工效率有直接影响。一般情况下,单个放电脉冲时间长短与单个放电脉冲放电能量大小成正比,增加放电脉冲放电时,或是缩小放电脉冲间隔,都可以提高加工效率。但是工件表面质量会相应降低。在放电脉冲间隙选择过小的情况下,虽然会增大放电脉冲频率,但同时在放电脉冲间隙时间内也会有无法很好的排除电蚀余留的产物、工作液(电介质液)消电离不充分等情况的发生。在工作液消电离不充分的情况下来不及恢复到电极丝与工件之间应有的绝缘强度,则容易产生电弧放电烧断电极丝。反之,在放电脉冲间隙过大,则会影响工件表面质量和加工效率。但是在放电脉冲宽度过大的情况下,就会在放电间隙中产生放电点集中现象,从而致使断丝。在一般情况下根据工件材质与工件厚度不同,放电脉冲时间与放电脉冲间隙时间的比值在1:8之间选取。
在电参数中切割速度是在加工效率上体现最直观的一个因素。在电火花切割加工过程中,进给过快,则有可能因为放电能量不足,造成电极丝与工件直接接触,造成短路,继而引发断丝。此时加工速度反而更慢。进给过慢,有较多的空载波,致使加工速度过慢。大大落后于工件被蚀除的速度,电极间将偏于开路,会时而开路时而短路,容易引起断丝。进给过快过慢都会引起加工不稳定,不能很好发挥机床性能。
3.4. 因为工艺方法和路线造成断丝的情况
3.4.1. 工件装夹原因造成的断丝
电火花线切割机床在加工金属薄板件时,大多采用多层堆叠的装夹方式来进行切割加工。如果装夹不得当,薄板与薄板层间叠压不实,极容易在切割过程中因为机械振动和电极丝的拉力,致使在切割过程中重叠板发生位移,加工中出现电极丝被卡死,导致电极丝断裂。
另外在切割薄层金属材料或者超薄层金属材料的时候。因为其本身刚度性能较低。机床运行过程中材料本身可能发生大幅度颤抖。这种情况下也容易发生放电不均或卡丝现象,致使电极丝断裂。这里以0.1 mm厚度的钛合金材料加工为例,在加工此类材料时大多采用两层较厚的钢板将其夹在中间,以辅助被加工材料,使其减少因材料颤抖而发生的电极丝断裂。
3.4.2. 不合理的切割路线引起的断丝
在线切割加工中不合理的加工路线也是引起断丝的重要原因之一。这里面很重要的一个因素是在设计切割路线时没有考虑到因为工件刚度原因在工件加工过程中产生的形位变化而导致断丝。
如图2中a所示切割路线,当切割到远离夹持部分时工件可能因为自身重量或者材料刚度不够的原因致使靠近夹持端已被切过的工件部分下垂。这样就会造成工件远离夹持端部分与坯料部分将电极丝夹紧甚至卡死。造成电极丝断裂。
在图2中b所示切割路线,则会大大减少工件自身刚度原因或者工件重量原因造成工件形位变化而夹丝现象发生,从而大大减小了断丝的风险。
此外因为切割路线问题造成材料内应力平衡遭到破坏,使被加工材料发生变形,也有可能导致电极丝被夹断。
例如在加工模具凸模时,如果采用切割路线是由外向内切割的路线。凸模在坯件材料上被切割下来的过程中,会很大程度的破坏模具坯件材料内部应力平衡,从而使被加工材料发生变形,可能导致所加工凸模精度降低,甚至电极丝被夹断。如果采用预制工艺孔(穿丝孔),不从坯件材料外部切入。而是将切入点设置在坯件材料轮廓内的封闭切割。在这种情况下便最大限度的减少破坏坯件材料内部应力。能更好的保证凸模的尺寸精度和避免因材料应力而断丝。
3.5. 电极丝直径与材质造成的断丝
电极丝直径的粗细是影响断丝的一个主要原因。电极丝粗细,一方面影响电极丝所能承受的极限张力,减少电极丝的抖动幅度,另一方面电极丝的粗细直接确定切缝的宽窄,同样影响工作液是否容易渗透进切缝,是否有利于排屑。所以为确保加工的稳定,及时更换电极丝。防止因为电极丝直径过低而引起断丝影响加工效率。
电火花线切割机床常用电极丝依据材料分类通常可分为钼丝、钨丝、铜丝。其中钼丝与铜丝在平时使用中最为常见。铜丝延展性好,加工过程稳定。但是由于自身材料原因铜丝抗拉伸能力较差,在放电加工过程中铜质电极丝自身损耗也大。所以在加工过程中电参数与张紧力选择不合适就容易产生断丝。又根据其材质特性,铜丝多用于单向慢走丝线切割机床中。钼丝由于材质特性,其熔点高、韧性高、抗拉强度低、低热膨胀系数和较高密度等典型特征。所以钼丝常用在往复走丝切割机中(快走丝线切割、中走丝线切割)。但是因为钼丝材质原因,其在穿丝等过程极易因为弯折而造成损伤而断裂。
4. 结束语
数控电火花线切割机床在运用中影响电极丝状态的因素很多,以上仅是在实践运用过程中对部分常见断丝原因的分析和探索。并在此基础上摸索出相应的预防和解决方法。相对比其他类型加工模式,数控电火花线切割是具有其特有的技术优势的。在技术上总结、实践中积累解决问题的经验,并系统反馈于平时的实践操作中。这样便可更好的提升工作效率和工件质量。