1. 引言
电机常用的散热系统为风冷散热系统、液冷散热系统和蒸发冷却散热系统。其中风冷散热系统相较于其他散热系统而言,因其具有可靠性高、成本低廉和散热装置安装简便等优点被广泛应用于小功率电机 [1]。开启式电机的散热系统多采用强迫风冷散热系统,利用电机内部额外的风扇系统提高了电机的散热效率。
开启式电机的电机外壳和前后端盖都留有散热孔,散热孔可以将电机内部的风路与电机外部的风路接通,外部空气可以通过散热孔进入到电机内部进行热交换 [2]。电机运行时将产生各种损耗,这些损耗转产生的热量使电机各部件发热,电机内部的温升升高 [3]。如果开启式电机的散热结构设计不当会造成电机内部温升升高,电机内部温升过高除了会减少电机内部绝缘材料的使用寿命,而且还会降低电机的工作效率,使得电机内部温升继续升高,造成电机的工作温度进一步上升,形成恶性循环,严重影响电机寿命和电机运行的安全性 [2] [4]。
许多专家学者对开启式电机的散热已经有了比较广泛的研究。NODA等 [5] 设计了一款应用于车辆上的开启式电机,此电机采用风冷散热系统且在电机前端留有大量的散热孔。KIM等 [6] 提出了一种应用于开启式电机的热网络模型,通过该模型计算得到的开启式电机在风冷散热系统下的电机定子温度与实际的电机定子温度的误差小于2℃。NAKAHAMA等 [7] 针对车用开启式电机,提出了在风冷散热系统下的电机定子铁心外部与内部双冷却的散热方案。
本文以开启式IP21四级电机为研究对象,运用流体仿真软件Flow Simulation,以提高电机散热能力为研究目标,基于正交试验法对开启式电机散热结构进行优化设计,选取电机的外壳散热孔数量,散热孔位置以及电机内部风扇叶片半径作为试验因素,在Flow Simulation中仿真模拟不同组合下的电机外壳温度,根据正交试验的极差分析来确定散热孔数量、散热孔位置、风扇叶片半径大小的最优组合方案。
2. 正交试验设计方案
正交试验设计因素以及正交表的选取
本次正交试验选取3个试验因素,即风扇叶片半径A,外壳散热孔开孔数量B,外壳散热孔开孔位置(平均分布) C,每个因素都取三个水平,如表1所示。本次的正交试验设计的目的是寻找电机风扇叶片半径、电机外壳散热孔开孔的数量和位置的最优组合,使得电机的散热效果最好,而电机外壳的温度最能反映电机的散热情况,因此把电机外壳的温度作为本次正交试验设计的试验指标。
其中A1代表风扇叶片半径为69 mm,A2代表风扇叶片半径为72 mm,A3代表风扇叶片半径为75 mm;B1代表外壳散热孔开孔数量为22个,B2代表外壳散热孔开孔数量为26个,B3代表外壳散热孔开孔数量为30个;C1代表外壳散热孔开孔位置为外壳的上部和中部,C2代表外壳散热孔开孔位置为外壳的中部,C3代表外壳散热孔开孔位置为外壳的上部和下部。
选取的正交表应该要使试验因素不被裁减,试验因素水平也不被缩减,因此若忽略因素之间的交互作用,
正交表对于3因素3水平的正交试验是最优的正交表,正交试验的具体安排如表2所示。
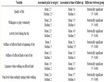
Table 2. Orthogonal test schedule
表2. 正交试验安排表
3. Flow Simulation仿真
SOLIDWORKS Flow Simulation直观的计算流体力学(CFD)工具可使设计人员模拟真实条件下的气体流动,因此选择使用Flow Simulation进行电机外壳温度的仿真。Flow Simulation的仿真分析步骤为:
1) 模型预处理;
2) 仿真参数设置;
3) 结果后处理。
3.1. 模型预处理
Flow Simulation的模型预处理就是删去对仿真结果没有影响或者影响较小的零件与特征。对于本模型而言,首先删除对电机的散热没有影响的零件,例如飞轮罩、接线盒、螺栓等,其次删去对仿真结果影响较小的特征,例如模型中的圆角、倒角、螺栓孔等,最后简化部分零件,例如将电机的内部风扇简化为圆柱体、轴承简化为圆柱体等,同时对电机外壳的散热孔和前端盖的散热孔进行了封盖处理,确保电机的内部空间为封闭状态,简化后的电机模型如图1所示。
3.2. 仿真参数设置
对于电机外壳温度的仿真分析类型以及物理特征设置为内部的固体内热传导;流体数据库选择空气;默认固体设置为钢;热动力参数的温度设置为25℃。
开启式电机的转轴、轴承和上下端部的材料设置为钢;定子铁心和定子冲片的材料设置为硅钢片;铝锭的材料设置为铝;外壳和前后端盖的材料设置为铁。
开启式电机工作时产生的温升主要是由开启式电机内部的转子铁芯和定子冲片的运转产生的热量所引起的,将转子铁芯和定子冲片设置为热分析仿真中的体积热源,体积热源的温度设置为60℃。
要得到仿真的数值,必须要给定需要的边界条件,对于开启式电机设置如下的边界条件,如图2所示。
1) 入口边界条件:开启式电机的入口边界条件设置等于内部风扇的设置。风扇设置为外部入口风扇,选择简化后的风扇的上表面作为入口边界,风扇的风机曲线选择风机曲线405型号的外部入口风扇,流动参数设置为垂直于面,环境压力设置为0.101325 MPa,温度设置为25℃。
2) 出口边界条件:选择端盖的内表面为出口边界,边界条件的类型设置为压力开口,环境压力设置为0.101325 MPa,温度设置为25℃。
3.3. 结果后处理
在仿真结果中插入体积参数,组件选择为电机外壳,参数选择为温度(固体)。
仿真结果例图如图3所示。
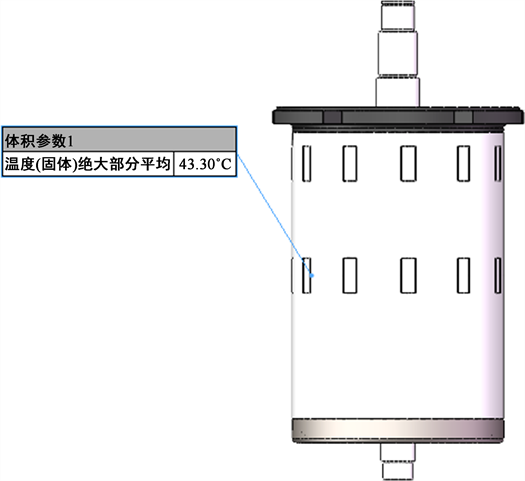
Figure 3. The temperature of the motor housing
图3. 电机外壳温度
将仿真实验的结果填入正交表,如表3所示。
4. 正交试验的结果分析
4.1. 极差分析
极差分析法可以较为直观的分析试验的结果,极差分析法主要包括极差分析表和因素水平与指标关系图两部分。
极差分析的计算公式如下。
(1)
(2)
(3)
式中:
为各因素i水平下的试验指标和;
为第k个指标;
为
的平均值;n为试验次数;R为因素的极差。
方差分析表如表4所示,因素所对应的试验指标和的大小可以判断因素的优水平,把各因素的优水平进行组合得到最优组合。极差可以反映因素对试验指标的影响大小,因素的极差越大说明该因素对正交试验的指标的影响也越大,因此可以根据极差的大小来确定该因素对于整体试验因素的重要程度,即因素的主次顺序。
为直观显示各因素水平对试验指标的影响程度的大小,以试验因素水平为横坐标,试验指标即电机的外壳温度为纵坐标,绘制出各因素水平与试验指标的关系图,如图4所示。
由表4和图4可知,在开启式电机的散热结构设计下,随着开启式电机内部风扇叶片半径的增加,电机的外壳温度也在逐渐增加,在试验因素水平A1下,电机的外壳温度最低。随着开启式电机的外壳散热孔开孔数量的增加,电机的外壳温度也在逐渐增加,在试验因素B1下,电机的外壳温度最低。在外壳散热孔开孔位置为外壳的上部和中部的结构下,即试验因素C1,电机的外壳温度最低;在外壳散热孔开孔位置为外壳的上部和下部的结构下,电机的外壳温度最高,同时由极差分析表可知,外壳散热孔开孔位置的极差的数值最大,因此外壳散热孔开孔位置对电机散热结构设计的影响最大。
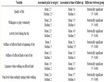
Table 4. Analysis of variance table
表4. 方差分析表
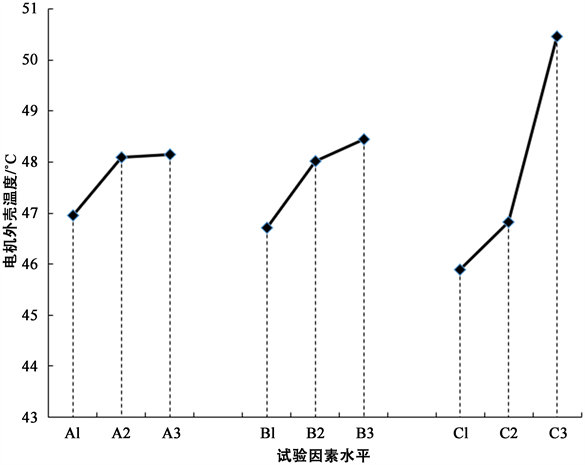
Figure 4. The level of each factor is related to the temperature of the motor housing
图4. 各因素水平与电机外壳温度关系
通过上述的极差分析可以判断三个因素对设计开启式电机散热结构的影响程度的大小的顺序依次为外壳散热孔开孔位置、外壳散热孔开孔数量、风扇叶片半径。对于开启式电机来说,电机外壳的温度尽量越低越好,由表可知因素A的优水平为A1;因素B的优水平为B1;因素C的优水平为C1,因此方案A1B1C1对开启式电机散热结构是最优方案,即风扇叶片半径为69 mm,开启式电机外壳的散热孔开孔数量为22个,散热孔开孔位置为电机外壳上部和中部,平均分布开孔位置则电机外壳上部平均分布有11个散热孔;中部平均分布有11个散热孔。
4.2. 优化方案验证
正交试验设计得出的最佳试验方案对应正交表中的试验号1,为A1B1C1。为进一步验证该方案为开启式电机散热结构设计的最佳方案,下述与原开启式电机散热结构方案进行对比。
在原开启式电机散热结构设计中,电机的风扇叶片半径为69 mm,电机外壳散热孔的开孔数量为30个,开孔位置为外壳的上部和下部,外壳上部平均分布有15个散热孔,外壳的下部平均分布有15个散热孔。在Flow Simulation中进行仿真时,模型的预处理和仿真参数设置与在正交试验下的设置完全相同,结果预处理选择温度表面,仿真结果如图5所示。
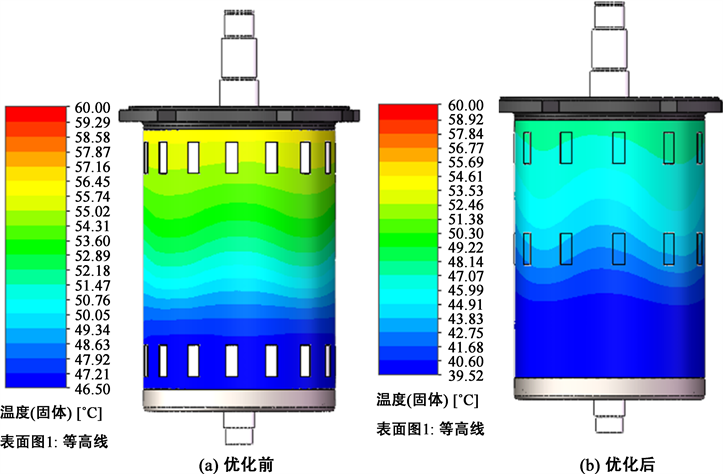
Figure 5. Motor housing surface temperature diagram
图5. 电机外壳表面温度图
由极差分析表可知,外壳散热孔开孔位置对开启式电机散热结构设计的影响最大,对于开启式电机来说,其电机的温升越低越好。由对比图可知,优化前的电机外壳表面最低温度为46.50℃,优化后的电机外壳表面温度最低为39.52℃。优化后的电机外壳表面最低温度比优化前的电机外壳表面最低温度降低了6.98℃。优化前电机外壳表面中部以及上部的温度要明显高于优化后的电机外壳表面中部以及上部的温度,因此电机外壳的散热孔位置放置在电机外壳的上部以及中部是最合理的位置。
在Flow Simulation中对优化前后的电机模型进行仿真,模型的预处理和仿真参数设置与在正交试验下的设置完全相同,在结果预处理阶段插入体积参数,组件选择为电机外壳,参数选择为温度(固体),优化前后的电机外壳温度图如图6所示,优化前的电机外壳温度仿真数值为51.13℃,优化后的电机外壳温度仿真数值为43.30℃。优化后的电机外壳温度比优化前的电机外壳温度下降了7.83℃,电机的散热状况得到了明显的提升,优化效果较好。
5. 结语
本文根据开启式电机在电机外壳与端盖处留有散热孔的散热结构和在内部利用风扇进行强迫风冷散热的散热系统方式,采用正交试验设计的方法,确定了影响开启式电机三个试验因素,即电机风扇半径、电机外壳散热孔开孔数量和电机外壳散热孔开孔位置。
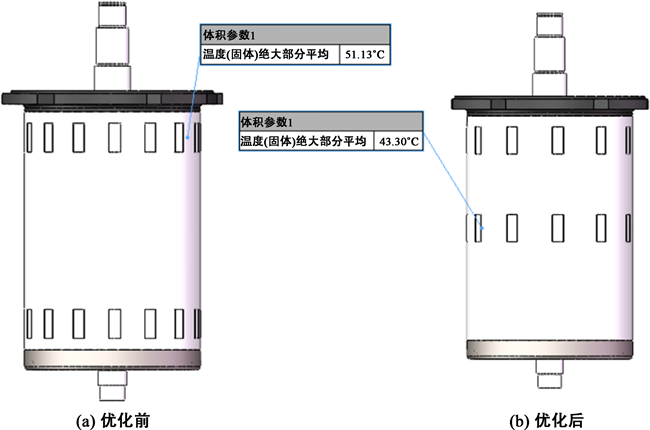
Figure 6. Motor housing temperature diagram
图6. 电机外壳温度图
采用
正交表确定了试验方案,并利用Flow simulation对开启式电机外壳进行仿真得到了电机外壳温度的数值。正交试验的极差分析表明了选取的三个试验因素对开启式电机散热结构影响大小的主次顺序依次为外壳散热孔开孔位置、外壳散热孔开孔数量、风扇叶片半径。由极差分析表判断出了因素A的优水平为A1;因素B的优水平为B1;因素C的优水平为C1,确定了正交试验方案A1B1C1为开启式电机散热结构的最优方案,即风扇叶片半径为69 mm,开启式电机外壳的散热孔开孔数量为22个,散热孔开孔位置为电机外壳上部和中部,平均分布开孔位置则电机外壳上部平均分布有11个散热孔;中部平均分布有11个散热孔。
在优化方案验证中,优化前的电机外壳温度仿真数值为51.13℃,优化后的电机外壳温度仿真数值为43.30℃,优化后的电机外壳温度比优化前的电机外壳温度下降了7.83℃,优化效果较好,增加了开启式电机的使用寿命和提高了开启式电机的使用安全性。