1. 引言
随着国内卷烟市场产品多样化,消费者对卷烟产品需求日渐趋于高质量、高标准、高要求,除了对卷烟产品本身的吸感之外 [1] [2],对于产品包装方式有着新要求,因此本研究对于“二五平”和“十包立式”两种中支卷烟条的包装方式进行设备改造,以适应一对二(一主机二辅机)方式进行两种包装方式的柔性化切换 [3],以满足市场需求、提高设备生产效率、实现产品包装多样化硬需求,并推广应用 [4]。
2. 爬升及下降输送通道研究
在研究设计“二五平包”与“十包立式”烟包的柔性化快速切换方案时,考虑到需要使用一台主机搭配两台辅机,导致烟包输送通道长度较大 [5],若采用低架输送通道,将会带来烟道储存烟包数量少,人员通行不便,不利于辅料及成品运输等缺点,而高架输送将能很好地解决这些问题 [6]。高架烟包输送通道一般安装高度大于2000 mm,保证人员通行及辅料运输有足够的空间。在此烟包柔性化快速切换方案中,ZB418主机烟包出口高度为1178 mm,“二五平包”的包装设备为YB518包装机,其烟包入口通道高度为2170 mm;“十包立式”的包装设备为YB55包装机,其烟包入口高度为780 mm。因此,高架输送通道高度设置为2170 mm,需要一段烟包爬升通道将烟包高度从1178 mm提升至2170 mm,一段下降通道将烟包高度从2170 mm降低至780 mm。
2.1. 烟包爬升通道设计
爬升通道将烟包高度从1178 mm提升至2170 mm,目前烟包爬升方式主要通过传送带完成烟包提升,此种方法结构简单、适用性强,且与传统低架输送通道有良好的适应性。
结构如图1所示,烟包在向上爬升过程中,需弹簧压轮对烟包施加压力,否则会因为烟包与输送皮带间摩擦力不够 [7],造成烟包下滑。因压轮间存在间距,导致烟包压力并不连续,若压力过大,将导致烟包与压轮碰撞,使烟包触皱或留下压痕,造成质量缺陷。
如图2所示,为保证烟包在爬升过程中始终受到压紧力,即在烟包爬升过程中至少有一个弹簧压轮与烟包侧面相接触,烟包弹簧压轮最大间距为烟包长度,烟包长度为91 mm,取整后为90 mm。也可增加一个弹簧压轮,保证爬升过程中始终有两个弹簧压轮与烟包相接触,下面对种情况下受力进行分析:
1、输送带辊子2、输送皮带3、弹簧压轮
Figure 1. Schematic diagram of cigarette bag lifting channel
图1. 烟包提升通道示意图
1、烟包 2、弹簧压轮
Figure 2. Schematic diagram of the force of a cigarette pack
图2. 烟包受力示意图
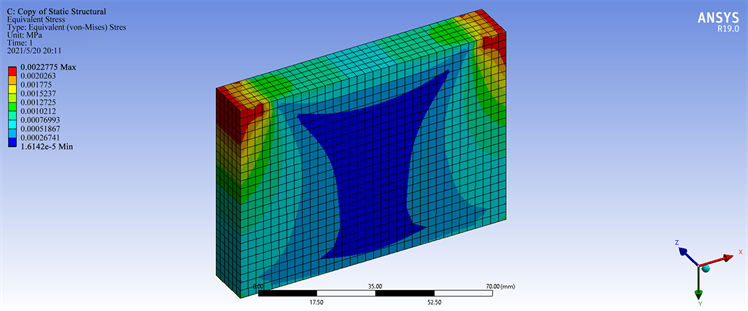
Figure 3. Stress diagram of cigarette bag with 90 mm distance between pressure rollers
图3. 压轮间距90 mm烟包应力图

Figure 4. Stress diagram of cigarette bag with 45 mm distance between pressure rollers
图4. 压轮间距45 mm烟包应力图
从图3、图4所示应力图看出,在相同压紧力需求下,压轮间距45 mm相比90 mm应力集中现象更加不明显,导致烟包触皱或划伤的概率更低,因此压轮间距设置为45 mm。
2.2. 烟包下降通道设计
下降通道将烟包高度从2170 mm降低至780 mm,因烟包存在重力,因此下降通道不需要传送皮带完成烟包输送,其结构相对简单。
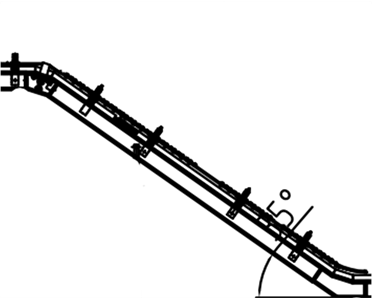
Figure 5. Schematic diagram of cigarette bag descending channel
图5. 烟包下降通道示意图
如图5所示,下降通道由滑轨、上护板和侧护板组成,上护板及侧护板主要起防止烟包飞出的作用。滑轨材质为45钢,与烟包相接触的面作抛光粗处理,摩擦力较小,烟包可沿滑轨向下滑动。在烟包开始进入下降通道时,烟包会与上护板发生碰撞,烟包下降至最低点时,烟包会与低架输送通道的传送皮带发生碰撞。当倾角越大时,烟包下降速度越快,发生撞击时动能越大;但倾角过小时会出现烟包下降不畅,造成阻塞,护板安装高度同样。
倾角与护板高度对下降无效性系数影响显著,且由图6所示主效应图看出当护板高度取10 mm,倾角取40˚时,下降无效性系数最小。
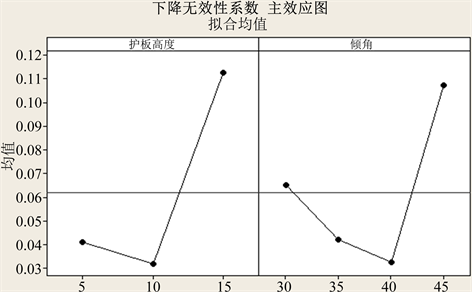
Figure 6. Main effect diagram of falling invalidity coefficient
图6. 下降无效性系数主效应图
3. 输送皮带动力系统分配研究
烟包输送通道通过输送皮带完成烟包的输送,输送皮带因运输速度高、连续性强,结构简单,可靠性强等优点,在卷烟生产中被广泛运用。在本章的研究中,输送皮带将主机生产出的小包输送至辅机,
是连接主辅机间的桥梁。本设计中,因主机和辅机位置相隔较远,且在运输过程中需要转弯,需要将多段输送皮带组合,完成烟包输送中烟包转弯、爬升、下降等过程。根据主机及辅机安装位置,输送通道布置如图7所示。
输送皮带动力系统分配设计
输送皮带需要电机驱动,传送皮带驱动原理图如图8所示,驱动电机经减速机减速后,将动力传递到输送皮带辊轴上,输送皮带辊轴在摩擦力的作用下,带动输送皮带旋转。为减少驱动电机安装数量及提高电机利用率,在相邻两条皮带间,可用齿轮传动机构传动,实现两条或两条以上传送皮带共用一个驱动电机,此时,输送皮带动力系统分配设计是否合理将影响输送皮带运行状况。
1、驱动电机 2、减速机 3、输送皮带4、输送皮带辊轴
Figure 8. Conveyor belt drive schematic
图8. 传送皮带驱动原理图
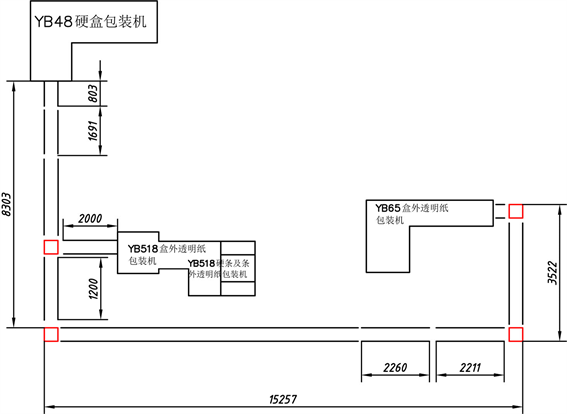
Figure 9. Schematic diagram of conveying channel length
图9. 输送通道长度示意图
1) 输送通道设计
根据主辅机相对位置,由图9可知,输送通道总长为29.1 m。查询输送皮带得知1 m输送皮带所需功率为45.4 W。减速机传动效率为95%,所需总功率为1390.8 W,所需电机额定功率为1807.9 W,得出所需电机数量为2.4台。即输送皮带电机为3台。
2) 驱动电机动力分配
图10所示为输送电机分配位置,单台驱动电机功率为0.75 Kw,可驱动输送皮带的最大长度为16.5 m,一共3台驱动电机,小组决定,驱动电机动力分配如下:1号电机驱动1、2、3、4共计4段输送皮带,2号电机驱动5、6段输送皮带;3号电机驱动8、9共计2段输送皮带。在此动力分配下,电机安全系数均大于或等于1.3,符合负载要求。
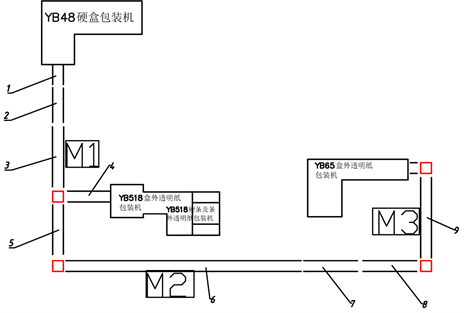
Figure 10. Installation position diagram of drive motor
图10. 驱动电机安装位置示意图
4. 柔性化快速切换分道器研究设计
为了实现“二五平包”与“十包立式”烟包的柔性化生产,需要将两台辅机并联,考虑到需要使用一台主机搭配两台辅机,需要设计烟包通道快速切换装置,实现短时间内将烟包输送通道在YB518包装机YB55包装机间相互切换。研究人员决定采用柔性切换烟通道,只需拆除柔性烟包切换通道的固定螺栓,
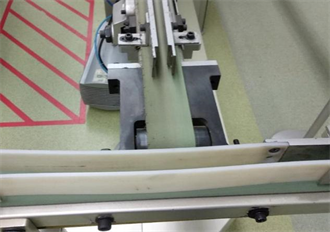
Figure 11. Physical diagram of lane divider in straight line state
图11. 分道器直线状态实物图
烟包输送通道就可在一定范围内随意弯曲,实现在不同辅机间的快速切换。
根据主机与辅机放置位置,研究人员将分道器设置为,分道器呈直线时,烟包通道通向YB55包装机,分道器呈90˚转弯时,烟包通道通向YB518包装机。
如图11所示,分道器是通过柔性条对不同通道的接/断,实现分道的功能,分道器可以根据实际生产需要,快速将将烟包引入“二五平包”或“十包立式”包装机,从而满足不同包装样式对设备的要求。
柔性通道需在直线状态与90˚转弯状态间切换,在直线状态时,柔性通道可设计为与普通通道宽度相同,而在90˚转弯通道状态时,通道宽度设计不合理将导致烟包在转弯处发生阻塞。通过相关性实验、回归分析得出当通道宽度在28.5 mm时阻塞次数为负数,实际阻塞次数最小值为0,此时阻塞次数最少,且实验所有中支牌号时,均不发生烟包阻塞现象,即转弯处通道宽度确定28.5 mm。
5. 动态车速自主调节系统研究
在实际生产中,主机短时停机的发生频次较高,当主机因夹烟或者辅料搭接短时停机时,停机时间基本小于30 s,此时输送通道上烟包数量较少,导致辅机频繁在停机与启动间切换,辅机工作状态不稳定,存在质量风险。若在烟包输送通道上增加检测器,检测通道上烟包数量,以此为依据控制辅机车速动态调整,可减少辅机停机次数,增加辅机运行稳定性。
在距辅机烟包入口处不同距离的3个点的烟包通道上安装有检测器,当通道上烟包数量较少时,烟包间存在间距;当烟包数量较多时,烟包会出现首尾相接现象。烟包通道上烟包数量适中时,烟包序列处于1号2号检测器之间;当首尾相接的烟包序列到达1号检测器位置时,说明烟包通道上烟包较多,辅机接收到信号后控制辅机提速;当烟包序列长度小于2号检测器位置时,说明通道上烟包数量较少,辅机开始减速;当烟包序列长度小于3号检测器时,通道上的烟包序列极少,辅机立即停机。
1、1号检测器2、2号检测器3、3号检测器
Figure 12. Diagram of detector installation position
图12. 检测器安装位置示意图
由原理可知,可通过调整如图12中的1、2、3号检测器距烟包入口处的距离来控制辅机加减速或停机的时机,研究人员决定设计实验选择出最佳组合,减少辅机的停机次数。
1) 检测器距离设置
1、2、3号检测器安装位置通过距烟包入口处距离来确定。参考辅机技术说明书,3号检测器推荐安装位置为距烟包入口处2~3 m,2号检测器推荐安装位置为距3号检测器1~3 m,1号检测器推荐安装位置为距2号检测器2~5 m,安装位置如下表1所示。
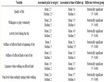
Table 1. Orthogonal experimental factor table
表1. 正交实验因子表
2) 根据因素选择表进行正交实验
根据因素水平表,3因素3水平采用L9表,按照正交表设计实验方案进行实验,试验记录如下表2所示。
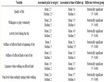
Table 2. Orthogonal experimental table
表2. 正交实验表
通过正交实验确定,3号检测器安装位置为距烟包入口处2.5 m,2号检测器安装位置为距3号检测器3 m处,1号检测器安装位置为距2号检测器3.5 m。
6. 总结
通过技术的研究与设计,本文通过对烟包爬升通道设计、烟包下降通道设计、输送皮带动力系统分配研究设计、柔性化快速切换分道器研究设计、动态车速自主调节系统研究设计等,实现了“二五平包”与“十包立式”烟条生产线的柔性化切换,并首次实现FOCKE系列主机与GD系列辅机的适配性生产应用。提高产品线产品牌号切换效率,大大提升设备生产效率,实现产品包装多样化硬需求,并推广应用。