1. 前言
作为应用最为广泛的可拆卸机械连接形式,螺纹连接具有可靠性高、操作简单、成本低廉等特点,普遍用于铁路轨道扣件系统的紧固。扣件系统通过螺旋道钉提供合适的预紧力,将钢轨和路基紧固成一个整体,从而为列车行车提供稳定可靠的支撑。若装配时扭紧力矩过大,极易导致超过螺栓材料的屈服极限,将使螺栓在超拧状态下发生断裂或者延迟断裂,扭紧力矩过小将导致长时间使用时滑动、分离甚至松脱等现象,对结构的安全性带来隐患 [1] [2]。为了提高列车行车的安全性,铁路维护部门需要按照修规要求做好路基、轨道养护,对轨道螺栓进行松紧调配、确保扣件系统螺栓连接可靠是养护工作的重要环节。
在螺栓实际装配拧紧过程中,难以直接测量预紧力,通常间接通过其他手段来实现对预紧力的控制,如扭矩控制法、转角控制法、伸长量控制法等。因此,拧紧方法、监测策略以及拧紧装备等,即拧紧技术对螺纹预紧力的离散有着决定性的影响。拧紧技术的发展对于螺栓安装、维护质量和铁路安全起到重要的作用。
2. 常见的螺栓拧紧方法
螺栓预紧力的大小通过施加的扭矩进行控制,在拧紧过程中螺栓发生转动产生转角的变化,螺栓伸长量同时产生相应变化,因此基于扭矩、转角、伸长量的检测和控制,形成了扭矩控制法、扭矩/转角控制法、伸长量控制法、屈服点法等螺栓拧紧方法 [3]。
1) 扭矩法
扭矩控制法通过控制拧紧过程中的扭矩达到预定扭矩从而实现螺栓的拧紧,目前该方法应用最为普遍。扭矩法中拧紧力矩T和预紧力F之间的关系如下式所示,上式中组成拧紧力矩的螺旋副间的摩擦力矩和螺母与支撑面的摩擦力矩均与摩擦系数有关。下式为拧紧力矩计算方法。
(1)
式中:T——拧紧力矩,N∙m;T1——螺旋副间的摩擦力矩,N∙m;T2——螺母与支撑面的摩擦力矩,N∙m;F——预紧力,N;d2——中径,mm;ψ——螺纹升角,φ——螺旋副的当量摩擦角,φ = arctan(f),f为螺纹副摩擦系数;d0——螺纹孔径,mm;D0——螺母环形支撑面外径,mm。
对上式进行简化可以得到 [4]:
(2)
式中:D——螺纹公称直径,mm;K——扭矩系数。
扭矩系数K的大小受螺旋副摩擦系数和螺母与支撑面之摩擦系数的影响,并非常数。螺纹的尺寸精度、螺栓/螺母的材质、表面状态、润滑条件以及拧紧速度等均对K值的离散度造成影响,因此扭矩控制法的精度主要取决于K值 [4] [5]。
由于K值常根据加载经验以及加载条件进行选取,其不确定性会影响预紧力的加载结果,在实际应用中根据工艺经验给出建议的K值选择范围或者规定具体K值。但是螺纹连接面状态的变化或变形导致计算中所用的K值与实际状态不符,造成预紧力达不到精准控制的要求。扭矩法在实际使用中的精度相对较低,获得的预紧力约有50%的误差 [6]。
2) 扭矩/转角法
扭矩转角法也称“转角法拧紧”,于上世纪六十年代在西方国家开始发展起来,该方法在扭矩法基础上发展而来。扭矩转角法是一种螺栓拧紧的过程中,先使用扭矩法控制拧紧至低于拧紧力矩某一值(门槛扭矩)使得螺栓和螺母紧密结合,接着再拧一个规定转角的控制方法 [7]。
在扭矩/转角法的拧紧过程中,螺栓在外力作用下旋转,产生的预紧力与转角之间的关系如图1所示。oa阶段为螺母空转和逐渐贴近的阶段,当到达a点的贴紧扭矩后,开始进行转角测量。ab阶段为弹性变形,转角和扭矩之间呈线性关系,达到b点最大转角后,随着扭矩的继续增加,b点后进入超弹性区域,在该区域内螺纹出现非线性弹性变形乃至塑性变形。
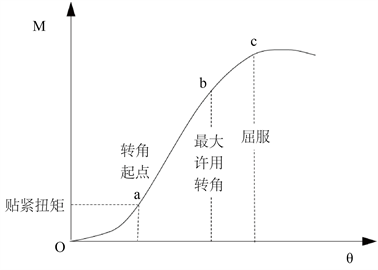
Figure 1. Relationship between torque and angle
图1. 扭矩–转角关系图
ab段的线性弹性变形,其螺旋产生的变形和转角之间有确定的关系,因此可以根据刚度和变形计算预紧力,如下式所示 [8]。
(3)
式中:F——预紧力,N;C——螺旋副总刚度,N/m;
——总伸长量,m;C1——螺栓刚度,N/m;C1——螺栓头部刚度,N/m;
——转角;P——螺距mm。
采用扭矩/转角法拧紧时引起的轴向压紧力力分散度较低,因此相比于扭矩法可以实现精度更高的预紧力控制的效果 [9]。扭矩/转角法在使用中需要确定门槛扭矩即转角起点,拧紧时需要控制速度,避免粘滑现象和过扭现象,对于螺栓和螺母的加工质量要求严格。
3) 伸长量法
伸长量法以螺栓弹性变形阶段的伸长量跟螺栓所受的应力成正比关系作为测量原理,通过测量螺栓伸长量获得所需的预紧力。预紧力和螺栓伸长量的关系如下式。
(4)
式中:F——预紧力,N;C1——螺栓刚度,N/m;
——总伸长量,m;LM——拧紧后的螺栓长度,mm;L0——螺栓的初始长度,mm。
伸长量法的检测结果受螺栓本身的性能影响为主,在其他影响因素中,张冬梅等通过正交试验方法进行的研究结果表明,螺栓拧紧扭矩的影响最为显著,螺栓摩擦系数影响次之,垫圈基本没有影响 [10]。根据图1中ab段扭矩和转角的线性关系可知,在螺距不变的情况下,扭矩与伸长量也有线性关系,扭矩作为伸长量法检测中的重要因素,扭矩确定的情况下伸长量的精度可控。李栋等采用超声波横波法检测了螺栓伸长量的变化,实验值与理论计算值在100~600 MPa的最大误差小于5.61%,误差绝对值的平均值在2%左右 [11]。相比于扭矩法、扭矩转角法获得的预紧力往往受到润滑、摩擦、螺栓材质、表面状态等诸多因素的影响,伸长量法更能真实的反应实际所需的扭矩,因此其控制预紧力的精度更高 [12]。但是伸长量法需要运用红外、超声波乃至CCD图像采集等手段测量螺栓伸长量,受限于设备使用条件和装配效率,应用并不广泛。
4) 屈服点法
屈服点控制法是在扭矩/转角法基础上进一步发展得来的一种螺栓拧紧方法,通过将螺栓或者螺母拧紧到屈服点从而实现拧紧。该方法中螺栓在预紧力和工作载荷作用下出现局部塑性变形,达到螺栓连接的不松动、不脱扣的效果,比扭矩/转角法的拧紧效果更好。从图1中可以看出,扭矩增加到c点,达到了材料的屈服强度,材料开始产生微量的局部塑性变形,一方面可以使得材料产生加工硬化的效果,屈服强度有所增加,另一方面螺栓获得了更大的预紧力,且预紧力的离散度更小,确保了拧紧的可靠。
采用屈服点法拧紧时,通过对拧紧扭矩/转角曲线的斜率进行计算和分析来确定是否达到屈服点,在线性弹性变形阶段扭矩转角斜率基本保持稳定,并且为极大值;当进入到非线性弹性变形塑性变形阶段,扭矩-转角曲线逐渐趋于平缓,斜率开始出现下降;当斜率下降到规定数值时对应于预紧力达到屈服点,采用屈服点法的预紧力正确度可以控制在±8%以内。
该方法能够实现高精度的螺栓拧紧,且在相同的夹紧力下螺栓材料可以减少28%~55%,节约成本55%,有效地降低螺栓的材料和成本 [13]。但因为夹紧力需产生塑性变形,因此螺栓仅能使用2~3次,往往用于一次性装夹后无需反复多次拧紧的螺栓装配。屈服点法在应用中如何精确的捕捉螺栓的屈服点是一个难题,传统的螺栓屈服点通过斜率判断,当拧紧曲线斜率减小到弹性阶段斜率的50%,即判定为屈服。但是拧紧过程中数据波动性对斜率数据造成干扰,导致无法精确铺捉到屈服点。汤春球在扭矩/转角法的基础上采用固定频率采样、滤波有效降低了数据的波动性,采用线性回归方程取得扭矩–角度曲线的梯度和线性斜率系数(LSc)精确的确定螺栓拧紧的屈服点,改善了扭矩衰减情况 [14]。此外。如何获得准确的屈服点并且分析该方法下过高的预紧力对螺栓疲劳强度的影响需要进一步深入研究。对于屈服强度和抗拉强度较为接近的高强度螺栓,采用屈服点法还需要考虑螺栓的延迟断裂问题。
综上所述,四种典型的螺栓拧紧方法的优缺点比较如表1所示。扭矩/转角法、屈服点控制法、伸长量法的预紧力精度高,但是技术成本较高、开发难度相对较大,拧紧设备或工具的工作效率相对较低,推广和应用受到了一定的局限,多用于高精度高、可靠性的螺栓连接。扭矩法尽管预紧力精度较差,但是其成本低、效率高,操作简单,目前在螺栓拧紧作业中应用最为广泛。
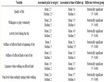
Table 1. Common tightening methods and their characteristics
表1. 常见拧紧方法及特点
3. 拧紧工具及装备的应用
随着在高强度螺栓材料、集成电路、数显技术以及微控制器等技术的快速发展,螺栓副制造技术以及螺栓拧紧相关技术研究成果不断进步,相应的拧紧技术及其装备发展迅速。拧紧技术的发展经历了手动拧紧、半自动拧紧以及全自动拧紧阶段,正朝着数字化、智能化拧紧方向发展。
拧紧工具主要是各种类型的扳手、拧紧机和拧紧生产线。扳手包括普通扳手和扭矩扳手,普通扳手使用时依赖操作者的经验,无法精确定扭。扭矩扳手采用扭矩法进行定扭,主要有指针式、数显式的各类扭矩扳手,可靠、重要的螺栓连接往往采用精度较高的数显式扭矩扳手施工,数显式扭矩扳手在发达国家应用较为普遍,以德国和日本在这一领域的技术和装备较为先进,已经成为扭矩扳手的重要发展趋势。数显式扭矩扳手的动力源有手动、气动、电动、液压等形式,这几种类型的扭矩扳手的主要优缺点对比如表2所示。
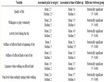
Table 2. Characteristics of digital display torque wrench [15]
表2. 数显式扭矩扳手的特点 [15]
随着我国制造业的快速发展,对拧紧装备的需求越来越大,自动化程度的要求越来越高,因此各种拧紧机和拧紧系统的开发和应用受到重视,以电力驱动的拧紧机和拧紧系统在生产线装配中得到了广泛的应用。自动化拧紧装备的研发主要解决多工位、高效、高精度拧紧问题,近十多年来国内的企业和研究机构开展了大量的研究工作,围绕拧紧作业中的定位、机构运动、拧紧动作、预紧力误差控制等方面开展研究,不断优化系统的识别、动作、精度控制算法,取得了良好的进展。如安徽江淮汽车股份有限公司基于PLC、AVR等开发了多轴电动拧紧机控制系统,能有效解决了欠拧紧、过拧紧及扭矩曲线显示等关键问题,并应用汽车装配生产线 [16];辽宁工业大学的赵博等人基于单片机、PI调节算法设计了无刷直流电机控制系统,并将该控制系统成功应用于活塞螺母拧紧机上 [17]。上汽通用五菱汽车股份有限公司的发动机前端盖的拧紧系统,实现了传动多轴自动拧紧 [18];林巨广等人设计了机械手式变矩双轴拧紧机,实现了提高生产效率的目的 [19]。廖金团等采用PLC与S120相结合的控制方法,设计了发动机装配线上的拧紧机定位控制系统,提高了控制精度 [20];一汽解放汽车有限公司无锡柴油机厂改进了S350梯形框架拧紧机的梯形框架,提高了螺栓拧紧的精度和稳定性 [21]。
现代拧紧技术以扭矩、转角的控制为核心,借助于多传感器技术的综合,推动了拧紧控制方法、拧紧控制技术的创新。如扭矩传感器、转角传感器、伸长量传感器在拧紧系统中综合应用,实现了扭矩、转角和伸长量信号的采集、分析,提高了拧紧作业的质量 [22]。现代先进拧紧技术还能够完成对关键工序的实时质量监控和数据跟踪采集,实现防止漏拧紧、防止拧紧顺序错误、防止零件漏装等,解决了螺栓装配预紧力控制精度、实施过程监测、可追溯性等问题,大大提高螺栓的装配质量和管理水平。金文伟等设计6轴制动盘螺栓拧紧机,通过1个总控机构控制6根拧紧轴的分控机构,保证6根拧紧轴同步拧紧,并能控制螺栓的拧紧顺序,防止漏拧或过拧的发生 [23]。
随着现代信息技术、自动化技术的迅速发展,基于新型传感技术、自动控制技术和网络技术乃至人工智能技术的现代先进拧紧技术,使得螺栓拧紧装配技术进入一个新的阶段。赵俊峰提出了基于深度学习的CNN模型,直接从激励响应信号中学习特征,并监测螺栓连接结构的装配紧度,该方法可以有效的区分6种螺栓松紧状态,相比其它方法具有更高的准确率 [24]。宋琛琛等 [25] 采用PZT材料的电阻片监控螺栓松动,有效地隔离了临近螺栓松动对信号的干扰,对螺栓松动的敏感性更高;基于压电传感器的螺栓监控技术也得到了研究 [26]。曾宪平等为了保证装配质量的可追溯性,研发了基于物联网技术的螺栓实时监控管理系统,实现了关键工位拧紧力矩数据监控 [27]。
借助云计算和大数据技术实现装备作业状态数据和螺栓实时状态的存储、处理及共享功能,有利于缩短维护周期、降低维护成本,该类技术能够进行数据在线采集、实时传输和处理,实现监控、报警、数据分析、数据共享、管理决策等功能,成为现代拧紧技术和拧紧装备的重要发展趋势。
4. 拧紧装备在铁路养护中的应用
铁路轨道养护作业的重要工作内容之一就是扣件系统检查、监测和维护,其中拧紧或者松开道钉是其中的重要环节。相比于制造业中常见的生产、装配工作环境,轨道养护具有以下独特性:1) 露天施工,受地理环境、气候条件的影响较大,难以获得持续、有效的电力供应;2) 维护作业不能影响正常行车,因此维护作业设备需要便于携带和移动,必要时可在短时间内搬离轨道;3) 作业效率高,拧紧可靠。因此,轨道养护中的工作条件对于拧紧设备和技术提出轻量化、高效、高精确度的要求。
目前轨道螺栓的旋松及紧固等维护作业主要以手工、冲击式内燃机机动扳手、液压扳手或传统电动扳手或装备为主,其预紧力控制采用扭矩法,重量相对较轻,能够满足便携和易于移动的要求。其中,手工拧紧的劳动强度大、作业时间长、工作效率低、螺栓拧紧质量无法保证,主要用于临时性手工作业。气动式拧紧尽管拧紧较为可靠,但是因使用中需要气源,难以用于野外施工作业。液压式工作效率较低,维护保养工作中难以得到有效应用。目前在铁路行业中普遍采用的电动拧紧技术及装备,多应用于生产线的各关键部位拧紧,其使用环境良好、工况单一,精度较高,但也存在以下缺点:系统多采用工业级PC,不便在移动场合应用;外形和重量都过大,不利于转场搬运,因此难以满足特殊工况的轨枕螺栓高精度拧紧养护作业的要求。
对于轨道螺栓的拧紧作业质量,我国有明确的规定,如“《铁路线路修理规则》(2019)规定:护轨道钉或扣件齐全完好,扭矩不符合规定者不超过±5%”,TB/T 30990-2012《扣件螺栓机动扳手》3.2要求“机动扳手扭矩精度±5%”。铁路养护部门松、紧螺栓采用机动扳手进行,主要以德国、日本的紧扣机动扳手为主。在铁路螺栓的安装和维护领域,德国ROBEL公司系列电动扭紧工具则占有重要地位,扭矩精度误差低于4%,通过汽油机供给动力和工作照明,转速80/230 rpm,最大扭力1000 N∙m,用于线路上的各种扭力操作,目前在国内铁路维护领域的进口设备占有较大的比例。日本电动数显扭矩扳手,控制扭矩可以达到1000 N∙m~3000 N∙m,控制范围较广,扭矩控制精度为4%,内置microSD卡能实现扭矩数据的存储,在国际市场上应用较广,法国吉斯马的相关装备最大扭矩达到2600 N∙m,具有较高的定扭精度,在轨道行业上有一定的推广。国产的内燃机机动扳手相比于国外产品尽管价格较低,但是精度控制较差,使用寿命和可靠性有待进一步提高。
尽管现有轨道螺栓的拧紧作业质量能够满足相关的扭矩规定要求,但是从螺栓拧紧质量来看,依然有很大的技术提升空间。现有装备采用扭矩法控制预紧力精度差的局限,往往造成螺栓过拧紧,导致螺栓拧断或丝牙破坏或轨枕破坏;无法精准统计全作业周期螺栓拧紧后的扭矩数据;冲击大、噪音大等,影响了铁路养护作业的工作质量和效率。因此,进一步提高螺栓的预紧力控制精度、监控螺栓松紧质量、降低机动扳手重量、提高使用中的舒适性,是轨道螺栓拧紧装备的发展方向。
5. 总结和展望
近年来,现代拧紧技术的快速发展使得其工程应用成为可能,与汽车制造行业以及航空航天行业相比,铁路、轨道交通行业在养护作业中对螺栓的先进拧紧技术的应用还不够广泛。随着铁路技术的飞速发展,列车高速重载是发展的必然趋势,特别是复兴号标准动车组的上线运行,其持续运行速度达到350 km/h,不仅对螺栓连接安全可靠性的要求更高,而且留给维修作业的时间间隔越来越少,原有的作业方式及维护手段远不能适应现代化铁路发展的要求。先进拧紧技术与智能的结合和应用,提高拧紧作业的精度、效率,乃至实现对养护作业质量的监控和管理,将是铁路、轨道交通行业养护作业的重要发展方向。
基金项目
重庆市技术创新与应用发展专项重点项目(cstc2019jscx-fxydX0065)。