1. 背景
国家2018年8月22日,国务院总理主持召开国务院常务会议,会议决定有序扩大车用乙醇汽油推广,2019年12月底全国计划推广乙醇汽油,目前除原来推广乙醇汽油省份和地区外,北京、天津、河北地区开始销售乙醇汽油,山东部分炼厂开始销售乙醇汽油,山东京博石油化工有限公司为适应国家政策调整,结合公司现有情况分析,确定汽油中的烯烃含量是主要的制约因素,综合分析公司各种原料烯烃含量,制定相应措施,实现生产乙醇汽油目的,同时为同类炼厂问题解决提供依据。
2. 乙醇汽油国家标准及公司现状分析
1) 车用汽油标准:现行标准执行GB19730-2016,烯烃含量执行国V标准控制24% (v),过渡至2018年12月31日前;2019年1月1日~2022年12月31日执行国ⅥA标准控制18% (v),2023年1月1日起执行国VIB标准控制15%;
2) E10乙醇汽油标准:现行标准执行GB18351-2017,89、92、95号烯烃含量执行国V标准控制24% (v),过渡至2018年12月31日前;2019年1月1日~2022年12月31日执行国VIA标准控制18% (v),2023年1月1日起执行国ⅥB标准控制15%;98号烯烃含量控制15%。
3) 炼厂油品烯烃含量分析
公司标准:目前公司烯烃控制13%,油品调和内控12%;
92号汽油:烯烃最高9.9%、最高13.3%,平均12%.04%
95号汽油:烯烃最高11.2%、最高12.8%,平均11%.92%
98号汽油:烯烃11%
通过以上分析,我公司汽油中烯烃能够满足生产乙醇汽油的标准。
公司汽油主要来源于经过催化裂化、加氢饱和、醚化之后获得,其中醚化是汽油降低烯烃含量的重要措施 [1]。因生产乙醇汽油的原因,汽油中氧含量规定不得超过10%,因此汽油醚化降低系统含量,不能在作为主要手段。醚化作用对油品中烯烃含量的影响分析需要详细分析。
3. 醚化装置停运前后烯烃平衡
公司对汽油的加氢主要分为三个单元,流程如图1所示。生产乙醇汽油需要停运公司醚化装置,前后各油品的烯烃平衡关系如表1所示。
通过表中数据显示,汽油醚化是汽油降低烯烃含量的重要手段 [2],如果停运醚化装置,油品中烯烃含量上涨幅度较大,会成为影响乙醇汽油产品标准的重要因素。轻汽油烯烃变化:停醚化后轻汽油烯烃含量从37%涨到55%,上涨18%个点;按照轻汽油切割比例24%计算,混合油烯烃上涨4.32% (数据依据2018年4月~2018年8月,停醚化后装置烯烃变化);中汽油烯烃变化:中汽油醚化停醚化后烯烃含量由44%上涨至48%,上涨4%,按照抽余油采出比例23%计算,混合油烯烃含量上涨.0.92%;混合油烯烃变化:停醚化后烯烃含量上涨5.24%,目前混合油平均烯烃含量24%,停醚化后上涨至29%~30%。
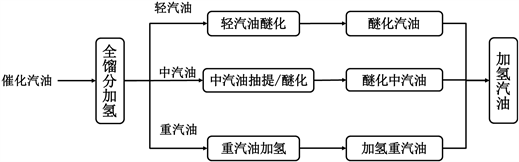
Figure 1. Flow chart of catalytic gasoline processing
图1. 催化汽油加工流程图
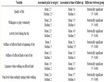
Table 1. Olefin content of different olefins before and after etherification
表1. 醚化前后烯烃各油品烯烃含量
4. 成品汽油调和现状分析
组成汽油的主要组分为:烷基化油、碳五、重整抽余油、苯、二甲苯、MTBE等。根据各项组分分析,生产的汽油烯烃主要来自公司的加氢汽油,其中各牌号油品加氢汽油的含量如表2所示。
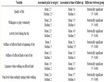
Table 2. Proportion of catalytic gasoline in each grade gasoline
表2. 各牌号汽油中催化汽油比例
汽油池调和分析:从目前加氢装置烯烃含量及停醚化后烯烃变化来看,如果按照公司执行标准汽油加氢装置烯烃需要降低6%。如果按照国家标准国VIA执行,调和没有问题,标准过度到2022年12月31日;如果执行国VIB,按照92、95号50%比例调和,烯烃含量在指标上限,需要解决烯烃超标问题。
5. 解决技术方案
基于生产需求,2019年初需要停醚化,进行乙醇汽油的调和,混合汽油烯烃含量需要降低至22%,导致轻汽油和中汽不在事宜作为生产汽油的合格组分,这两重组分的下一步处理处理方案需要解决,基于此,指定6中解决方案:
方案1:轻汽油抽出送至催化装置
自脱轻塔抽出后轻汽油送至二催新加柴油喷嘴、三催送至第二提升管多产烯烃组分(丙烯、乙烯),轻汽油24吨/小时,烯烃含量50%,轻汽油送至催化后,烯烃含量降低12%,中汽油、重汽油混合油剩余18%,满足需求;
工程量:去三催化流程具备、二催化需要进行装置内配管,不停工可以进行实施;
优点:解决烯烃问题,投资少,马上可以实施;
缺点:影响催化装置部分加工量,投用效果需要进行验证轻汽油转化率;
方案2:轻汽油定向分离裂解做低碳烯烃:利用某单位定向分离技术对轻汽油进行定向转化产低碳烯烃,可以满足需求;
工程量:新建定向分离装置,项目工程费用5000万元以上,采用固定床酸性催化剂,两反应器切换再生。
优点:解决烯烃问题;
缺点:新上装置投资较大,实施周期预计2年时间;
方案3:中汽油定向分离缓和芳构化:利用采用固体酸催化剂对中汽油烯烃进行缓和芳构化,烯烃转化率最高85%左右,中汽油采出比例23%,烯烃含量48%,缓和芳构化后中汽油烯烃含量可以明显降低,混合油烯烃可以降低9%左右,可以满足需求;
工程量:新建缓和芳构化装置,项目工程费用约5500万元,采用固定床反应器,两反应器切换再生。
优点:解决烯烃问题
缺点:新上装置投资较大,单纯为解决烯烃问题;实施周期预计2年时间;
方案4:中汽油烯烃定向分离:分离中汽油烯烃,分离后剩余烯烃为轻重汽油烯烃,汽油采出比例23%,烯烃含量48%,混合油烯烃降低11.04%,可以解决问题;
工程量:对溶剂进行调整,烯烃回收塔根据塔顶抽出负荷进行改造。
优点:周期短,溶剂需要调整,改造较小;
缺点:目前正在进行考虑技术可行性,正在进行评估,无案例;
方案5:辛烷值恢复技术利用:
重汽油加氢后增加辛烷值恢复反应器,进行烯烃的异构及芳构化,烯烃降低5%左右。
工程量:新上反应系统,装置投资较大,需要提温增加热源;实施周期预计2年时间,
优点:技术成熟,直接可以应用;
缺点:投资较大,烯烃降低较少;
方案6:吸附烯烃分离技术,分离汽油中烯烃,作为单体烯烃产品或者去裂解装置;
可以提高提高产品价值,目前技术处于小试阶段,近期进行中试,技术还不成熟,持续进行关注。
6. 总结
从以上6项技术措施进行对比,目前可以马上进行实施的为第1项轻汽油去催化装置,目前去200万吨/年催化流程具备,去65万吨/年催化可以进行流程改造实施,现阶段正在推进去两套催化装置试验;第2、3、5项实施周期较长,投资较大,需要考虑现有装置用地问题;第4项与技术方进行沟通对接进行确认是否可以实施,第6项作为持续关注技术,作为单体化工品提高产品附加值。从质量控制角度目前公司执行标准为国六B标准,实际国家执行标准为国六A至2022年12月31日,可以考虑对市场无影响的前提下执行国六A标准;从油品调和的角度降低汽油加氢装置汽油的调和比例可以解决。