1. 概述
产品转产过程(Product Transition Process)定义产品从项目概念成功地转移到工厂生产必要的事件、活动和里程碑,确保在工厂生产时采用已证实有效的工艺流程并在一定范围内推广转产方法,从而在批量生产开始时能够提高质量保证、成本控制、项目管理水平 [1] 。
国外机载电子产品领域对于产品转产流程非常重视,早在1984年美国国防部就签发了《Transition from Development to Production》(从研发到生产转移)的DoD 4245.7-M文件,定义了转产相关的设计、测试、生产、转产计划、场地、后勤、管理以及经费核算所需要遵循的过程和标准 [2] ;在美国国家宇航局(NASA) 2005年颁布的《系统工程手册》中的5.5节就是产品转产(如图1所示),描述了不同类型的系统转产的目标以及过程 [1] ;美国还从1985年开始,就设立了“最佳制造实践”评选项目,航空航天领域一直是该项目的考察重点,Raytheon、Rockwell Collins、Northrop Grumman、Lockheed Martin等公司都曾被评为“最佳生产实践卓越奖” [3] ,并且有McGraw-Hill公司的专著 [4] 和Rockwell Collins (现为Collins Aerospace)公司论文 [5] 探讨如何在机载电子产品领域开展产品转产工作。
我国中国质量协会在2001年设立了“全国质量奖”,原名“全国质量管理奖”,是对实施卓越绩效模式并取得显著质量、经济、社会效益的组织授予的在质量方面的最高荣誉;国家质检总局于2013年设立了“中国质量奖”,授予在中华人民共和国境内质量领先、技术创新、品牌优秀、效益突出的组织和对促进质量发展做出突出贡献的个人。但是目前还没有机载电子产品领域的专项评比,几乎没有电子产品转产领域的学术研究论文发表。
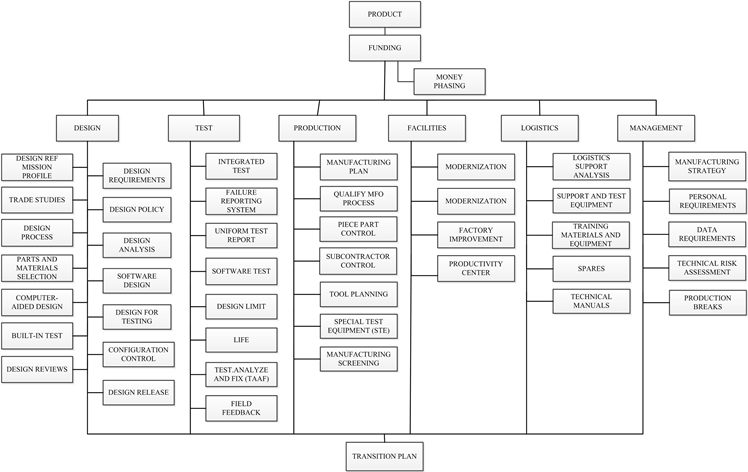
Figure 1. The conversion activity defined in the DoD 4245.7-M document
图1. DoD 4245.7-M文件中定义的转产活动
2. 民用机载电子产品的适航审定要求
适航性(Airworthiness),简称适航,即适于在空中飞行,是民用航空器(包括飞机、飞艇等)一种专有属性,它是指在预期的运行环境和经申明并被批准的使用限制条件下运行时,航空器(包括其部件及子系统、整体性能和操纵特性)的安全性和物理完整性,这种品质要求航空器应始终能保持其符合经批准的型号设计状态并始终处于安全可用状态,该品质主要是通过适航管理来实现的。适航性源于安全性,是世界人民对航空器的一致要求,是通过飞机及其组成部分全寿命周期内的设计、制造、试验、使用、维护和管理的各个环节来实现和保持的。
航空器设计局方审定设计人提出的审定基础和运行限制、审定其生产条件、审定航空器处于适航状态;航空器的设计人和制造人根据经批准的审定基础,表明航空器的符合性。
2.1. 机载电子产品的适航认证方式
机载电子产品的适航认证方式主要有技术标准规定TSO取证和作为飞机型号的一部分“随机取证”。
在我国,适航相关的证件包括型号合格审定、生产许可审定和适航合格审定3大类16种适航证,如图2所示。
其中型号合格证(TC)是局方对航空器设计符合性的批准,表明航空器及其系统和零部件的设计符合规定的适航标准和要求,发动机和螺旋桨也可以单独申请TC;生产许可证(PC)是局方对航空器制造符合性的批准,重点在于确认航空器及其系统和零部件的制造、试验、安装等符合经批准的设计;(单机)适航证AC是局方对每架飞机制造符合性的批准。民用航空器的这三个证件都是局方颁发给航空器制造商的,即飞机制造厂或者“主机厂”,表明飞机的设计和制造以及生产的飞机产品本身符合了最低的安全性要
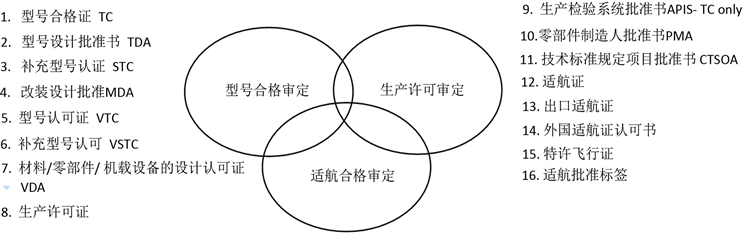
Figure 2. China’s airworthiness forensics
图2. 我国适航取证方式
求和已批准的型号设计。通常主机厂会要求具有独立的技术标准规定(TSO)的装机设备/系统必须取得相应的适航证后才有装机资格,即申请并且取得CTSOA项目批准书或者TSOA批准,由美国FAA批准的TSOA产品可以根据CAAC和FAA的双边协议,通过材料/零部件/机载设备的设计认可证(VDA)进入中国市场。
无论是TSO取证还是随机取证,都需要遵循民用航空产品研制流程。经过了几十年的发展和积累,民用航空产品研制流程趋于成熟,并形成了一系列的航空推荐最佳实践流程和指导文件,从安全性和适航管理的角度来指导安全性评价、飞机和系统研制、软件和硬件的设计和开发工作,如图3所示。
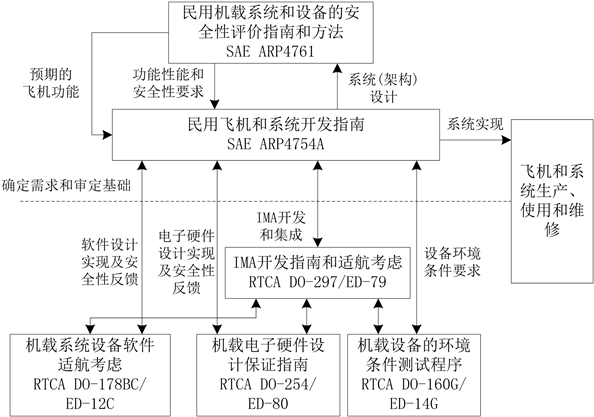
Figure 3. Aircraft and system development guidance document
图3. 飞机和系统开发指导文件
其中,ARP4754A和ARP4761都是局方通过咨询公告的方式明确下来关于安全性评价流程指南以及飞机和系统研制过程指南,申请人须按照这些指南的推荐的设计开展推荐的过程开展研制工作。ARP4761描述了民用机载系统和设备的安全性评价过程和开展安全性评价的方法 [6] ,ARP4754A则描述了飞机和系统的开发过程,明确系统研制的主要活动、阶段和要求,这些航空推荐实践(ARP)指南是由美国汽车工程师学会(SAE)专家成立的工作组编写的 [7] 。
在确定了满足安全性要求的系统架构之后,设备和软硬件的研制工作正式启动,包括IMA中的软硬件模块和资源的研制。局方同样引用航空无线电技术委员会(RTCA)编写的技术文件作为其审查申请人开发流程的依据。这些指南文件包括了指导IMA开发文件RTCA DO-297 [8] 、机载设备软件开发指导文件RTCA DO-178B [9] (2011年12月更新为RTCA DO-178C [10] )和机载电子硬件研制的指导文件RTCA DO-254 [11] 。作为,此外RTCA DO-160G定义了环境条件测试要求 [12] ,也是重要的指南文件。
2.2. TSO取证产品转产要求
对于已经建立了TSO技术标准的机载电子产品,通常会采用TSO取证方式以便研发的产品可以直接表明与技术标准的符合性并复用在不同的飞机平台上。
TSO技术标准中明确要求了适航认证需要的生产数据,如果生产资料不符合要求,即便研发阶段数据都符合要求,也不能获得TSO认证。以下以TSO-C128a为例,说明转产对于适航取证和民用机载产品的重要性。
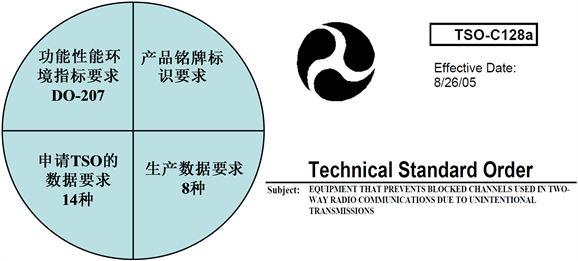
Figure 4. Device for preventing channel congestion caused by accidental transmission in two-way radio communication
图4. 双向无线电通信中用于防止意外传输导致通道拥塞的设备
TSO-C128a规定的适航数据如图4所示,其中明确规定了功能、失效状态类别、功能鉴定(最低性能指标)、环境鉴定(环境条件和试验程序)、软件鉴定、偏离,并对产品的铭牌标识作出了明确要求,此外提出了相应的申请资料要求和制造人资料要求。对于提交适航当局的数据以及制造商准备审查的数据要求如下表1所示。
2.3. 随机取证产品转产要求
对于没有TSO标准的机载产品,只能通过随机取证方式,作为TC的一部分表面其研制过程和结果符合相应的流程、功能、性能以及安全性要求,即按照图3所示的系统开发指导文件表明符合性。
1) 在《机载电子硬件设计保证指南》(RTCA DO-254)文件中,明确规定了需要检查生产数据、测试设施、通用资源的可用性和适合度来确定,采用硬件实现和验证过程的输出结果来确保高效的产品生产。
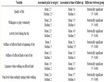
Table 1. Airworthiness review list
表1. 适航审查清单
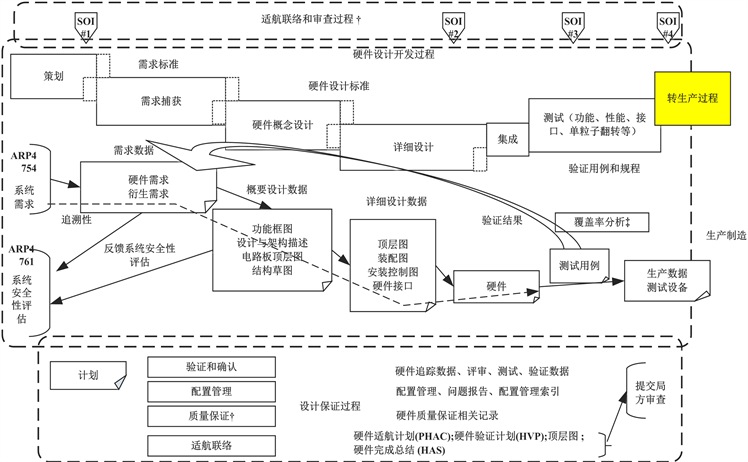
Figure 5. The development process of the onboard electronic hardware
图5. 机载电子硬件研制流程
机载电子硬件研制流程及产品转产如图5所示,其中机载电子产品转产的主要目标包括:建立包括所有设计和生产数据的基线来支持一致性的可重复生产活动;
2) 所有与安全性相关的制造需求都被识别并编入文档,并在生产过程中得到有效控制;
3) 衍生需求都被反馈给了产品实现过程和其他适用的过程;
4) 转产过程中的错误和疏忽环节都得到了妥善的处理。
3. 民用机载电子产品转产过程
产品转产过程用来对一个已经完成验证和确认的最终产品在集成为最终系统,或者将顶层的最终系统产品移交给意向的最终客户,这些产品(包括系统级产品)通常在研发过程中完成产品实现或者产品集成,产品转产过程是产品研制和实现过程中的最后一个环节,也是系统从一个层级到更高层级的桥梁。转产是产品线生命周期阶段的重要组成部分,也是最终产品工作项分解(WBS)中的重要组成部分。
3.1. 典型机载电子产品生产过程
一个典型的机载电子产品的生产过程如图6所示,在完成了表面贴装之后,产品进入了流水生产线,各生产设备或人工操作按照订单需求调整生产速度并进行协调。
在对当前产品生产有清晰的认识后,需要对产品进行进一步的分类。根据产品工艺流程和工作台的设置进行规划。根据产量和每天的工作计算新的节拍时间,节拍时间的计算方法如下,节拍时间是生产每件产品的平均时间,消除生产瓶颈,根据当前的生产工序和各个工作环节的划分,计算每个工作环节的工作节拍时间(Takt Time)。根据节拍时间对各个工作环节的工作量进行再次的优化和平衡。首先要考虑的是超出平均时间的地方,这些地方将成为实际生产中的瓶颈环节。在把超出节拍时间工作环节中的部分工作内容移到其他的工作环节之后,重新计算各个环节所需要的时间,尽量确保各个工作台之间的工作量接近节拍时间。如果有些重要的工作不能移动到其他工作环节,则在保留该工作环节的基础上,尽量减少该环节的工作量,以便与其他的工作环节进行合并或者共用,从而提高大规模生产的整体效率。
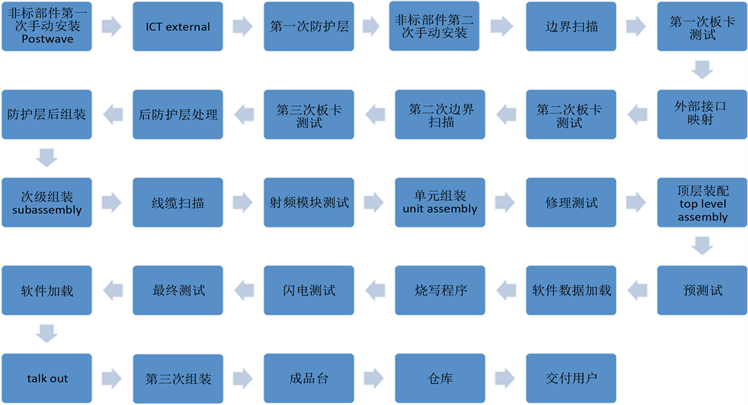
Figure 6. The production process of a typical airborne electronic product
图6. 典型的机载电子产品的生产过程
3.2. 机载电子产品转产过程活动
产品转产过程面向最终的产品和批量生产,并且这些产品将直接交付给最终的实际用户,因此产品转产有着更加严格过程和技术要求。为了达到产品高效一致性生产的目标,产品转产在产品开发的全生命周期的各个阶段都需要开展,主要包括项目策划阶段、产品研发阶段、和产品生产阶段,以下分别介绍在不同阶段需要开展的活动。
3.2.1. 项目策划阶段
在项目策划阶段,需要明确目标产品的成本目标,从物料、人工、场地、能耗、运营摊销等方面估算成本,建立生产测试计划和生产质量保证计划,建立产品转产/建造计划,明确生产的目标、测试需求、主要测试指标、工艺流程、工艺缓解时间安排、测试计划、里程碑节点等要素,并且定义目标产品的生产需求(如产量、节拍时间等),此外还需要研发、生产、质量、采购等部门联合制定产品开发项目计划,确定在产品中能够复用的研发和生产部件、测试环境、场地和产线,制定转产里程碑节点,并且规划评审更新产品制造成熟度,制定生产原则,并且针对转产和工艺流程设计进行工作项分解。
3.2.2. 产品研发阶段
在产品的研发阶段,需要更新项目策划阶段产生的输出,识别关重件(如直接影响关键指标、独家产品、长订货周期等),开展材料/部件的可生产性分析,确定部件发展路线图,对于可能废型(Obsolete)的部件开展持续供货分析,沟通潜在的供应商,并开展供应商策略管理,对需要替换和外协的部件编写或者更新技术要求,进行BOM清单审核,同时编写针对生产所需要的测试需求PTR,开展元器件相关的可靠性分析(如DFMEA/PFMEA),开发原型系统和产品,必要时采用3D打印的塑料模型来确认几何尺寸。
3.2.3. 产品试生产阶段
在产品的试生产阶段,需要更新项目策划阶段和设计阶段产生的输出,引入生产专家开展可生产性分析,根据生产要求和成本要求更新BOM清单,开艺流程编制和试生产,按照确定的生产要求开展全产能试生产以便发现生产线的瓶颈并作出相应的调整,改进生产流程和文件。新产品导入工程师将整个生产试制过程中发生的问题汇总到“试制问题报告”中,由生产管理部门组织召开新产品试制总结会议,对所有问题进行分析改进。确认改善方案及责任人后将所有问题提报至CQ进行追踪。
上述产品转产过程的活动可以用如图7所示的流程来表示。需要指出的是,这些活动需要根据企业的设计保证体系和流程,与产品研制的评审阶段相结合,为转阶段的条件要素贯穿到要设计评审(PDR)、详细设计评审(CDR)、测试就绪评审(TRR)、生产就绪评审(PRR)等里程碑节点中得到落实和管控。
对于民用机载电子产品,有竞争力的价格是赢得市场并持续发展的必要条件。我国自主研制的机载电子产品价格普遍高于国际民用机载产品,这也是若干已完成取证适航取证的产品无法得到市场认可的原因之一。
为此,要开展如图8所示的产品成本控制流程,在研发之初,就应到考虑产品的价格目标,将成本作为重要的“需求”,在项目策划阶段确定产品的原材料目标和可接受的生产/测试工时目标,进而分配产品成本。在研制过程中,评估产品设计、对比设计元器件清单(BOM)与目标成本之间的差距,确定生产投入的工时与目标之间的偏差并不断优化,在转产阶段制定针对性的行动计划来削减成本,使得产品的实际成本接近甚至低于目标成本。
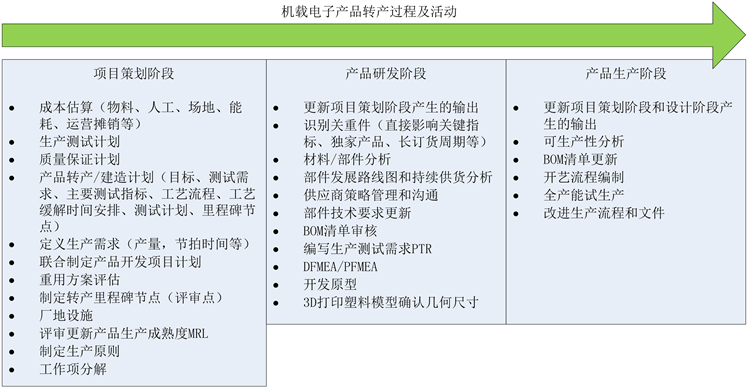
Figure 7. The on-board electronic product conversion process
图7. 机载电子产品转产过程
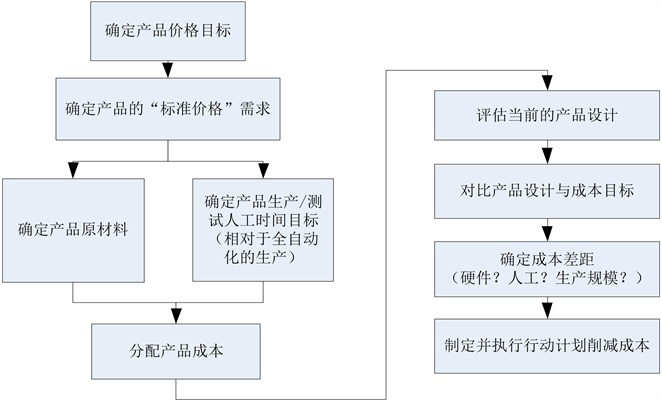
Figure 8. Product cost control process
图8. 产品成本控制流程
3.3. 新产品制造成熟度评价
为保障大规模时产品能顺利达到设计产能,引入制造成熟度(Manufacture Maturity Level, MML)评价生产过程的人、机、料、法、环以及产品设计,来协助产品产能的提升,促使生产效率得到提高、产品成本达到预期目标。
在生产成熟度评价的过程中,需建立具有不同专业背景的跨组织团队,来解决产品生产过程中可能出现的问题,同时通过制造成熟度评价来建立一套标准操作流程和评判标准,为决策层提供信息并掌握项目风险级别。产品成熟度评价可从生产技术和产品物料两方面进行评估,以下分别说明这两个方面的制造成熟度评价方法。
3.3.1. 产品物料成熟度
生产物料稳定是制造成熟的前提条件。定义了“0~5”的6个级别来描述产品物料清单(BOM)的成熟度(如图9),确定BOM从初始到满足成本要求和大规模生产的状态,具体说明如下:
0级和1级:初始设计阶段的物料清单,设计尚未固化,初步开展了重用和器件成本分析;
2级:已通过分析明确了关重件,完成了物料持续供货分析,确定了可重用的部件,通过初步器件成本分析;
3级:主要物料已经固化,可用于长订货周期器件的采购,用于工程样机和老化试验;
4级:物料清单已经基本固化,可用于试生产样机部件采购并支持生产测试;
5级:在试生产过程中,物料清单进行了必要的调整已经完全固化,用于批量生产、库存备货采购。
3.3.2. 产品制造成熟度
同样定义了“0~5”的6个级别来描述物料以外的人、机、法、环以及产品设计、成本控制等生产制造的成熟度(如图10所示),例如人员技能、场地设施、工艺流程、质量控制等,具体说明如下:
0级和1级:初始设计阶段,初步考虑了产品转产计划,尚未建立生产流程和环境;
2级:已完成了产品转产计划,明确了生产工时和质量控制目标,确定场地、人员、设备要求;
3级:完成了产品试生产,并在运行过程中进行调整和优化;
4级:批量生产样机部件采购并支持生产测试;
5级:全产能的生产制造达到了稳定状态。
3.4. 参与转产过程的角色和职责
在民用机载产品研制环境下,通常都采用项目经理负责制,即项目经理对产品的研发、生产、售后等全生命周期商业模型负责。产品转产过程也在项目经理的主导下,由研发、生产以及成本控制、供应商管理部门共同参与(如图11所示),具体参与的角色包括:
研发:技术经理、计划经理、系统工程师、产品线工程师、系统工程师、产品线工程师软件/硬件/结构工程师、配置管理、设计保证/过程控制;
生产:生产线规划、生产测试中心、生产工艺师、自动化机器编程人员生产经理、新产品转产经理、质量保证、PDM产品数据管理、设计保证/过程控制;
其他部门:生产成本控制、供应商/材料管理等。
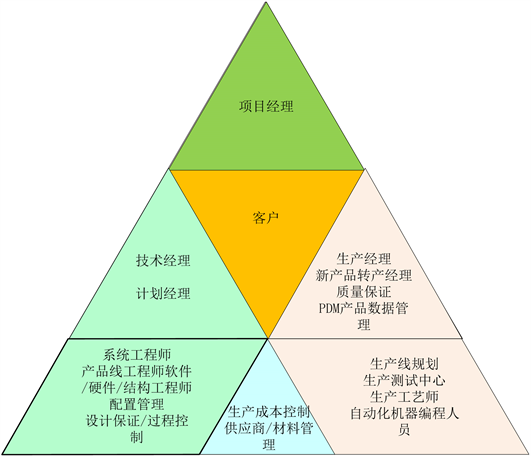
Figure 11. Roles and responsibilities for participating in the conversion process
图11. 参与转产过程的角色和职责
4. 结束语
由于使用场景的特殊性,民用机载电子具有高安全、高可靠、低成本的特点,并且需要通过适航认证,这对产品的设计、开发、生产提出来很高的要求。产品转产是产品设计研发和生产制造之间的纽带和桥梁,对于产品的质量和成本控制起到了至关重要的作用。本文参考业界顶尖企业如Collins Aerospace、Honeywell、Cobham的最佳实践,结合自身在C919、AG600、MA700等型号项目中的研发和生产经验,提出了机载电子产品的转产流框架程,明确了主要活动和转阶段条件,并且与项目执行过程中的项目里程碑节点(如概要设计评审PDR、详细设计评审CDR、测试就绪评审TRR、生产就绪评审PRR)相一致。产品转产相关的策划、评价活动应在产品研发早期阶段就开始,并不断更新直到产品开始交付。这些流程和方法也适用于其他电子产品的转产过程和生产成熟度评价。
参考文献