1. 引言
化学气相沉积(Chemical Vapor Deposition, CVD)金刚石薄膜具有高硬度、高耐磨性、高热导率、低摩擦系数和低膨胀系数等优异的热力学性能,是理想的工具材料之一。在工具表面沉积金刚石薄膜,大幅提高工具寿命的同时,还能改善加工工件的表面质量 [1] 。硬质合金因其优异的物理机械性能,广泛应用于工具行业 [2] [3] 。在硬质合金工具表面沉积金刚石薄膜可以提高工具表面的硬度和耐磨性能,进而提高其工作寿命。由于金刚石和硬质合金的热膨胀系数差异大,极易在基体和薄膜之间形成较高的热应力,导致薄膜与基体的附着强度低 [4] 。
硬质合金中的钴元素在金刚石薄膜沉积过程中,具有很强的催石墨化作用,也导致薄膜与基体的附着强度低。为了提高薄膜与基体的结合强度,通常采用化学预处理、增加过渡层和基体表面改性等方法。化学预处理方法是利用Murakami溶液((K3Fe(CN)6+ KOH + H2O)和Caro酸(H2SO4+ H2O2)对基体表面进行超声处理。增加过渡层的方法是在金刚石薄膜与硬质合金基体之间制备单层或多层物理介质的过渡层,一方面是硬质合金中粘结剂钴的不利影响,另一方面能够减少硬质合金基体与CVD金刚石薄膜之间界面物理性能的突变,缓和应力集中,改善硬质合金基体与金刚石薄膜的浸润性,可以提高基体与金刚石膜的结合力 [5] 。研究人员利用增加过渡层的方法,在硬质合金基体和金刚石薄膜之间增加金属或非金属镀层,提高金刚石薄膜与基体的附着强度 [6] [7] [8] [9] 。本论文利用硅掺杂方法,在硬质合金表面沉积金刚石薄膜,通过对所制备样品形貌及附着力的检测,对比分析硅掺杂对金刚石薄膜附着强度的影响。为制备高附着强度的金刚石薄膜提供原位沉积的工艺方法。
2. 实验
2.1. 实验材料
硬质合金圆棒,规格Ø4 mm * 60 mm,成份:WC-wt. 6% Co;
乙醇(C2H5OH),分析纯;
铁氰化钾(K3Fe(CN)6),分析纯;
氢氧化钾(KOH),分析纯;
硫酸(H2SO4),分析纯;
过氧化氢(H2O2),分析纯;
丙酮(CH3COCH3),分析纯;
正硅酸乙酯(C8H20O4Si),分析纯;
金刚石微粉,W5;
氢气(H2),纯度99.999%。
2.2. 主要设备及仪器
热丝化学气相沉积设备;
扫描电子显微镜,Zeiss ULTRA55;
He-Ne激光拉曼光谱,SPEX1403;
电动三爪卡盘。
2.3. 样品制备及表征
利用乙醇对基体进行超声清洗后,进行“化学两步法”预处理。首先,将硬质合金基体置于碱溶液(KOH + K3Fe(CN)6+ H2O = 1 g:1 g:10 mL)中超声30分钟,用清水冲洗后烘干。然后,将基体置于酸溶液(H2SO4:H2O2= 1 mL:4 mL)反应1分钟,用清水冲洗后烘干。最后,用颗粒度为5 μm的金刚石粉研磨基体表面,去除表面在“化学两步法”预处理时产生的疏松层,以丙酮超声清洗基体。预处理后的基体,固定于热丝化学气相沉积设备中的工件台上,用于热丝的钽丝对称分布于硬质合金基体的两侧。
硅掺杂金刚石薄膜的沉积实验的反应源气体为氢气,以丙酮为碳源,正硅酸乙酯为硅源,将正硅酸乙酯按照硅/碳的原子浓度比,配制Si/C浓度为20,000 ppm的混合溶液。利用氢气鼓泡法将碳源和硅源输入反应腔室内。为了进行对比研究,同时在圆柱形硬质合金基体上进行了普通金刚石薄膜的制备。普通金刚石薄膜(标记为样品A)和硅掺杂金刚石薄膜(标记为样品B)的沉积工艺参数如表1所示。薄膜沉积装置示意如图1所示,氢气瓶中输出的氢气I分为两路I1和I2,其中I1作为鼓泡的动力气体,经防倒流瓶(3),进入鼓泡瓶(4),为保证丙酮不受温度变化的干扰而影响输出流量,将鼓泡瓶置于装有冰水混合物的保温容器(5)中。输出的反应源气体I3(氢气、丙酮和正硅酸乙酯),和反应源气体氢气I2混合为气体I4,通过进气口(9)进入反应腔室(8),反应源气体在热丝(10)的激发分解作用下,在样品基体(11)表面生成硅掺杂金刚石薄膜。
利用扫描电子显微镜、He-Ne激光拉曼光谱检测所制备薄膜的形貌与质量。采用机械抛光法,利用金刚石粉和砂带对所制备的样品进行磨抛处理,考察圆柱形基体金刚石薄膜的附着强度。
3. 结果及分析
3.1. 薄膜性能表征
图2是连续沉积6小时的普通未掺杂和硅掺杂金刚石薄膜表面形貌。图2(a)中显示普通未掺杂金刚石的颗粒尺寸为3~4 μm,晶粒间的界线明显。图2(b)中的硅掺杂金刚石颗粒尺寸为1~2 μm,金刚石颗粒
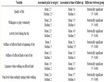
Table 1. Parameters of film depositing
表1. 薄膜沉积工艺参数
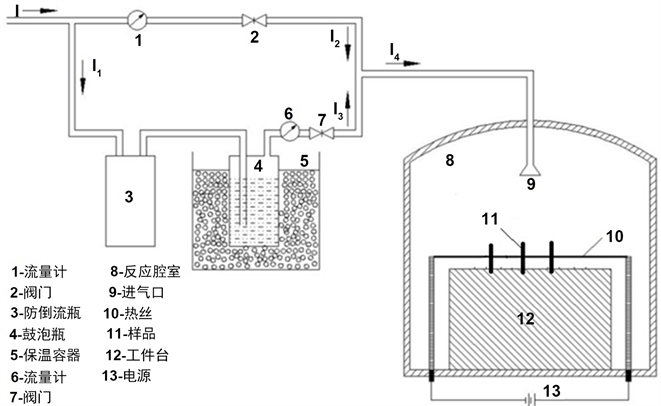
Figure 1. Schematic diagram of deposition system
图1. 薄膜沉积装置结构示意图
尺寸显著减小。两种类型的金刚石薄膜拉曼光谱如图3所示。从图3(a)中可以看出,普通未掺杂金刚石薄膜的拉曼光谱在1336 cm−1处显示出明显的特征峰,该特征峰表明薄膜中的碳结构呈现sp3结构,金刚石质量良好。偏离典型金刚石结构特征峰1332 cm−1,是由于薄膜内部有残余应力所导致。图3(b)中的硅掺杂金刚石薄膜的拉曼光谱中,1332 cm−1附近特征峰的半高宽增大,表明硅元素的引入,使得金刚石薄膜的结晶质量低于普通未掺杂金刚石薄膜 [10] 。
为进一步对比考察硅掺杂对圆柱形硬质合金基体表面沉积金刚石薄膜的影响,在生长6小时以后的普通未掺杂和硅掺杂金刚石涂层的基体上,用表1所示的工艺参数,继续原位沉积金刚石薄膜4小时。图4是累计沉积10小时后,普通未掺杂和硅掺杂金刚石薄膜的表面形貌图。图4(a)是沉积10小时的普通未掺杂金刚石薄膜表面形貌,同图2(a)相比,金刚石表面形貌无明显变化。图4(b)是沉积10小时的硅
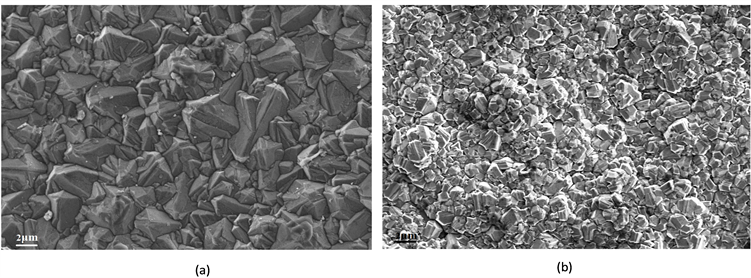
Figure 2. The morphology of diamond films deposited for 6 h: (a) conventional, (b) silicon-doped
图2. 沉积6小时的金刚石表面形貌:(a) 普通 (b) 硅掺杂
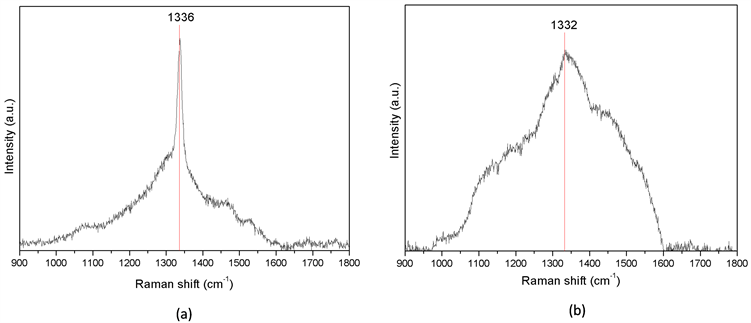
Figure 3. Raman spectra of the diamond films deposited for 6 h: (a) conventional, (b) silicon-doped
图3. 沉积6小时的金刚石薄膜拉曼光谱:(a) 普通 (b) 硅掺杂
掺杂金刚石薄膜表面形貌,和图2(b)对比可以看出,金刚石颗粒呈团簇状积聚,表明随着沉积时间的延长,在硅掺杂金刚石表面的原位沉积过程中,不断地二次形核与生长,随着沉积时间的变化,金刚石颗粒在细化。
拉曼光谱的检测结果表明,沉积10小时的普通未掺杂金刚石薄膜的光谱特征和沉积6小时的金刚石薄膜相比,特征峰从原先的1336 cm−1偏移至1338 cm−1附近,如图5(a)所示,表明薄膜内部的应力随着沉积时间的增加而变大。沉积10小时的硅掺杂金刚石薄膜拉曼光谱如图5(b)所示,拉曼光谱中除了代表金刚石特征的1334 cm−1附近的特征峰以外,在1480 cm−1附近也有明显的特征峰,由于晶粒的细化使得晶界面积增加,处于晶界处的反聚乙炔增多导致 [11] 。
硅掺杂金刚石薄膜的沉积过程中,由于硅原子半径比碳原子大,使得硅–碳键比碳–碳键在薄膜表面产生更多的缺陷,可以促进金刚石薄膜生长的二次形核率,使金刚石晶粒细化,形成亚微米级金刚石涂层结构,改变薄膜的应力状态,有利于附着力性能的提高。
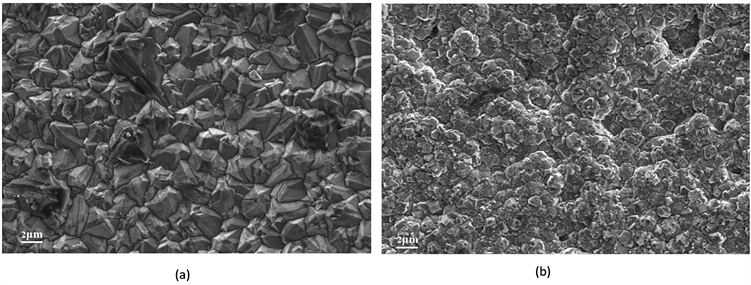
Figure 4. The morphology of diamond films deposited for 10 h: (a) conventional, (b) silicon-doped
图4. 沉积10小时的金刚石表面形貌:(a) 普通 (b) 硅掺杂
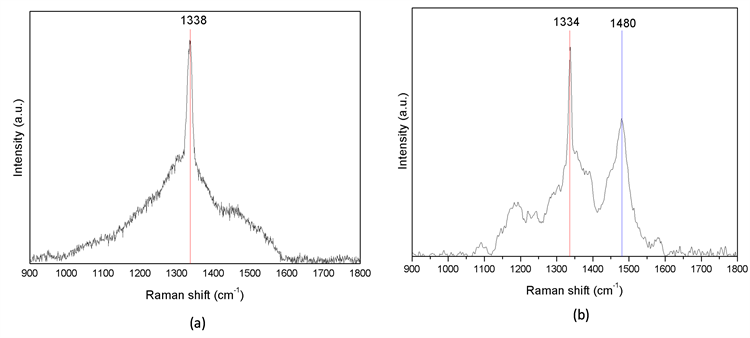
Figure 5. Raman spectra of the diamond films deposited for 10 h: (a) conventional, (b) silicon-doped
图5. 沉积10小时的金刚石薄膜拉曼光谱:(a) 普通 (b) 硅掺杂
3.2. 薄膜附着强度
由于圆柱形金刚石涂层样品无法进行Rockwell压痕测试,采用“抛光研磨法”对比普通未掺杂和硅掺杂金刚石薄膜与硬质合金基体的附着性能。将圆柱形基体装夹于车床的三爪卡盘,用涂有金刚石粉的砂纸对表面进行抛光处理。图6和图7分别是普通未掺杂金刚石和硅掺杂金刚石涂层样品抛光1小时后的扫描电镜形貌图。图6(a)显示出普通未掺杂金刚石涂层基体在抛光中出现明显的薄膜脱落现象。图6(b)中可看出在薄膜脱落的表面有露出的硬质合金基体(图中的白色部分)及残留的金刚石薄膜。普通未掺杂金刚石薄膜在沉积过程中,热残余应力积聚,在研磨抛光的外力作用下,导致薄膜脱落。图7是硅掺杂金刚石涂层抛光1小时后的形貌,薄膜表面光滑平整,未出现薄膜脱落现象,表明薄膜与基体的附着强度较高。同时表明,硅元素的引入,有利于金刚石薄膜的表面后处理。
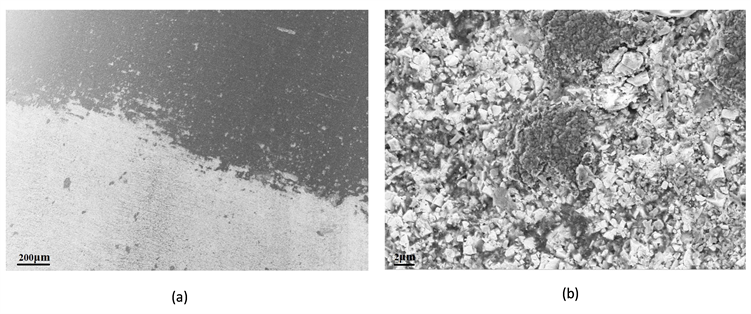
Figure 6. The morphology of conventional diamond films after polishing: (a) low magnification, (b) high magnification
图6. 抛光后的普通金刚石表面形貌:(a) 低倍率 (b) 高倍率
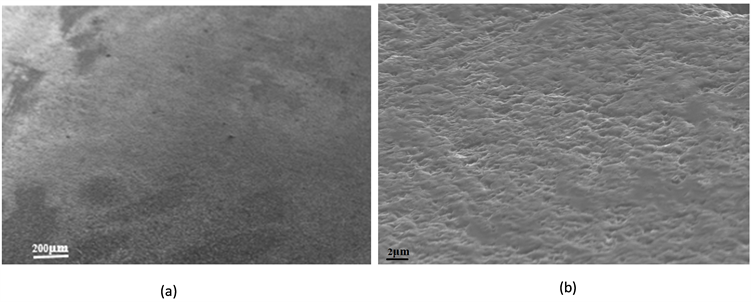
Figure 7. The morphology of silicon-doped diamond films after polishing: (a) low magnification, (b) high magnification
图7. 抛光后的硅掺杂金刚石表面形貌:(a) 低倍率 (b) 高倍率
4. 结论
本文利用热丝CVD方法,在圆柱形硬质合金基体表面沉积硅掺杂金刚石薄膜。
1) 在CVD金刚石薄膜沉积过程中,硅与碳结合形成硅–碳化学键,由于硅原子半径大于碳原子半径,在薄膜表面形成更多的位垒,有利于促进金刚石薄膜沉积过程中的二次形核,从而细化金刚石晶粒尺寸。
2) 硅元素的引入,减缓了薄膜内部的应力,能够显著提高薄膜与基体的附着强度。为硬质合金基体制备低粗糙度和高附着强度的金刚石薄膜提供了一种方便有效的方法。
基金项目
上海市自然科学基金资助项目(18ZR1401100);中央高校基本科研业务费专项资金(2232019D3-35)。