1. 引言
电动汽车控制器作为电动汽车的核心部件,用来控制电动汽车电机的启动、运行和停止,其与电动汽车电机装配的品质关系到整部车的运行状态。装配生产线是一种大规模高效生产的组织形式,它可按照一定的生产节拍完成各工位的作业任务 [1] 。传统电动汽车控制器装配方式主要是手动装配,工人劳动成本高,且效率低下,难以满足行业发展的需求。自动化技术、信息技术等的飞速发展极大推动了自动生产线的发展,同时也为研制高效、智能的电动汽车控制器装配流水线提供了良好的基础。本文以稳定、高效、智能为目标,根据电动汽车控制器装配需求,综合运用自动化控制技术、现场总线技术 [2] [3] 等设计并开发基于三菱可编程控制器的电动汽车控制器装配流水线控制系统,实现对电动汽车控制器装配流水线的整体控制。实践结果表明,该装配流水线有效解决了控制器在装配过程中工人劳动强度大、装配效率低的问题,在保证装配流水线稳定运行的前提下提高了控制器的装配质量和装配效率。
2. 电动汽车控制器装配流水线控制系统总体设计
本电动汽车控制器装配流水线主要由起点升降机、终点升降机、传送带、倍速链、气动阻挡器、活动气缸等部分组成,能够完成工装板的升降、输送、回收等动作,实现装配线的循环换板与连续作业,整体机械结构如图1所示。其中线体输送装置设计为上下双层式,上层部分实现控制器的装配作业,下层部分回收工装板。整个装配线分为起点升降装置、终点升降装置、线体输送装置,三种装置协调配合,共同完成控制器和电动机的装配以及工装板的回收工作。控制器与电机的装配工作是依托在工装板上进行的,装配线设有6个工位,依次进行6道工序当控制器与电机的装配完成第六道工序,由终点处的机械手臂将装配好的电机取走,工装板降落通过下层线体输送机构实现回收。
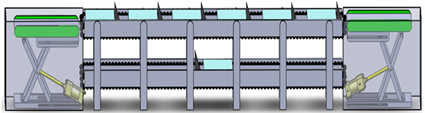
Figure 1. Integral mechanical structure
图1. 整体机械结构
电动汽车控制器装配流水线控制系统总体方案采用主/从式的控制形式,集数据采集、执行控制,数据运算于一体,执行控制系统实现对升降装置、传送带装置、线体输送装置、电机和气缸的联合控制;数据采集系统通过采集各工位处作业信息反馈至中央控制系统以确定是否进行下一步作业,实现信息采集与计算。本控制系统由中央控制模块、升降控制模块、线体输送控制模块、安全保护控制模块组成,控制系统总体结构如图2所示。
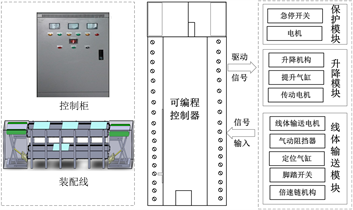
Figure 2. Overall structure of control system
图2. 控制系统总体结构
在本电动汽车控制器装配流水线控制系统中,信息采集单元将设备状态信息传输给三菱PLC进行数据的处理,PLC对传递的数据进行分析计算后,给执行控制单元发出命令,本控制系统通过可编程控制器与设备信息的智能交互,最终实现数据采集、动作控制和故障急停等功能,实时控制电动汽车控制器装配流水线的运行。
2.1. 升降控制模块
升降控制模块包括起点升降机和终点升降机,信号的采集通过限位开关进行,当起点升降机降到位,升降机未检测到板子,倍速链仍在运动,则升降机上的传送带在电机的带动下开始工作,将下层倍速链输送的工装板收回,当工装板触碰到升降机上的限位开关,传送带停转,起点升降机上升,当升降机升到位,若是上层倍速链运动,1号工位处没有工装板,则起点升降机上的传送带正转,将工装板送至1号工位处,待1号工位处检测到工装板信息,起点升降机传送带停转,起点升降机下落,进行下一轮准备,终点升降机功能和起点升降机类似,这里就不再累述,升降模块结构图如图3所示。
2.2. 线体输送模块
线体输送模块分为两部分,一部分为上层工作输送模块,另一部分为下层回收模块,线体输送模块共有六个工位,每个工位进行一道工序,当六块工装板都到位,定位气缸分别将其定位,若是起点升降机和终点升降机均到位,则倍速链停止运动,各个工位处指示灯亮起,工人师傅开始作业,当各工位处工人完成对应的工作,踩下脚踏,工位处指示灯熄灭,当六处指示灯均熄灭,且终点升降机升到位,则倍速链重新启动,各工位处的气动阻挡器下降,工装板依次输送到下一个工位处,线体输送模块结构如图4所示。
2.3. 安全保护模块
装配线每个工位处均设置一个紧急开关,每一个开关都可以控制整条装配线的运转,工人师傅遇到突发状况可以按下紧急开关,信息传送到中央控制系统,然后控制系统给执行机构发出指令,实现装配线的急停,从而保障了工人师傅以及操作设备的安全。
3. 电动汽车控制器装配流水线控制电路设计
本控制系统的设计选用三菱Q系列PLC [4] [5] [6] [7] [8] 为本控制系统的核心单元。
总控输入模块I/O分配在总控输入模块中,需要PLC的输入端口为2个。PLC的I/O口地址分配表如表1所示。
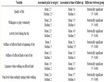
Table 1. Address allocation table for general control input module
表1. 总控输入模块地址分配表
在总控输出模块中,需要PLC的输出端口为8个,PLC的I/O口地址分配表如表2所示。
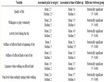
Table 2. Address allocation table for general control output module
表2. 总控输出模块地址分配表
在装配线输入模块中,需要PLC的输入端口为12个,PLC的I/O口地址分配表如表3所示。
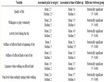
Table 3. Address allocation table for assembly line input module
表3. 装配线输入模块地址分配表
在装配线输出模块中,需要PLC的输出端口为19个。PLC的I/O口地址分配表如表4所示。
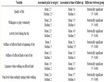
Table 4. Address allocation table for assembly line output module
表4. 装配线输出模块地址分配表
电机控制回路如图5所示。
4. 电动汽车控制器装配流水线控制系统软件开发
电动汽车控制器装配流水线的控制系统采用模块化的设计思路。基于装配线控制系统的总体方案,电动汽车控制器装配流水线控制系统设计的软件部分主要包括:中央单元控制程序、开关量输入程序、手动输入程序、数字输出程序、急停控制程序。
4.1. 电动汽车控制器装配流水线控制流程
本电动汽车控制器装配流水线主要分为三个部分:起点升降装置、线体输送装置、终点升降装置,三处协调配合工作,实现控制器的装配以及工装板回收,工作流程如下所述:
1) 起点升降装置动作
当起点升降机降到位,若起点升降机处工装板未到位,起点升降机上的传送带反转,将未到位的工装板传送到位,工装板到位后,触碰限位开关,电机停转,起点升降机将工装板提升到工作起点,当起点升降机升到位,装配线上层倍速链运动且1#工位处没有工装板时,带动传送带正转,将工装板传送至1#工位处,当起点升降机上未检测到工装板时,传动电机停转,同时起点升降机下降。
2) 终点升降装置动作
当终点升降机升到位,若终点升降机处工装板未到位,终点升降机上的传送带正转,将未到位的工装板传送到位,终点工装板到位后触碰限位开关,电机停转,终点升降机下降,下降到位后,若是下层倍速链在运行且下层倍速链未检测到工装板,传动带反转,将工装板传送至下层倍速链,下层倍速链检测到工装板后,传送电机停转且终点升降机上升。
3) 线体输送装置动作
当6个工位处工装板到位,上下层倍速链仍在运动,但在气动阻挡器的作用下,各工位处工装板停止前进,由于各工位处工装板触碰各工位处限位开关,6工位处定位气缸压杆伸出,将工装板固定住,当起点和终点升降机升到位后,上下层倍速链停止运动,6个工位处工位指示灯亮,各工位处工人开始装配作业,当6个工位处均工作完毕,各工位处工人踩下脚踏,各工位定位气缸收回指示灯熄灭,若终点升降机升到位,上下层倍速链启动,各工位处气动阻挡器下降,工装板向前滑行,1秒后气动阻挡器重新浮起。此外,本流水线在6个工位处均设置急停开关,每个开关均可实现整条流水线的急停,操作员在紧急情况均可以拍下开关,从而保证人身以及设备的安全。控制系统程序流程如图6所示。
4.2. 电动汽车控制器装配流水线程序结构
本文根据电动汽车控制器装配的需求,设计并开发基于三菱可编程控制器的电动汽车控制器装配流水线控制系统,综合运用三菱Q系列PLC控制器、远程I/O模块等实现对装配线的控制。控制系统主要分为:升降装置控制模块、线体输送控制模块、安全保护控制模块,三个模块中央控制单元的控制下协调工作,控制系统的设计的程序结构如图7所示。
5. 调试与结论
现场进行联机调试,验证现场动作与所设计的工序是否吻合。将控制器与电动机放置在起点工作位置,启动装配线,经过六道工序装配完成后,由机械手取走已装配的控制器,工装板经过下层倍速链完成回收。试生产实验数据如表5所示。
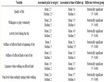
Table 5. Trial production experiment data
表5. 试生产实验数据
经验证,现场动作与所设计的工作流程完全吻合,电动汽车控制器装配流水线各模块工作紧密协调,工装板可以实现循环利用,安全保护装置能够应急制动。该流水装配线自2018年5月投产使用,由于采用了多工位循环输送,大幅提高了各工位的装配效率,截至目前已实现了连续75天无故障运行。