1. 引言
金属基复合材料(Metal matrix composites, MMC)具有高比刚度、高比强度、耐磨损性好和低的热膨胀系数等优异性能,近些年来,在航空、航天及汽车等工业领域得到广泛的关注 [1] 。其中,颗粒增强铝基复合材料具有可设计性强、成本低、应用面广、易制备等突出优点,从而成为金属基复合材料中的研究重点 [2] [3] 。目前,大多数研究多关注于铝基复合材料的制备工艺和基本力学性能上 [4] [5] [6] ,对于铝基复合材料划伤缺陷疲劳性能研究鲜有报道。在工程实际中,划伤缺陷是比较常见的微小损伤类型,在结构生产和结构服役中,各种可能都会造成划伤缺陷,如制造、装配和运输过程中由工具或设备等刮碰引起的划伤缺陷 [7] 。这种划伤缺陷在结构的制造和服役过程中均不可避免,因此,研究铝基复合材料划伤缺陷疲劳性能,对于结构设计和安全分析具有重要的意义。
本文对SiC/2009Al复合材料光滑试样和划伤缺陷试样(划伤深度0.15 mm、0.25 mm及0.40 mm)疲劳性能进行了分析,研究了划伤缺陷对SiC/2009Al复合材料疲劳性能的影响和材料的缺口敏感性,并建立了划伤缺陷试样的Kt-Kf关系式,为SiC/2009Al复合材料在工程上的应用及疲劳寿命预测提供了试验数据依据。
2. 实验材料与方法
2.1. 实验材料
实验材料为SiC/2009Al复合材料,材料毛坯为自由锻件,如图1所示,其化学成分如表1所示,拉伸性能如表2所示。
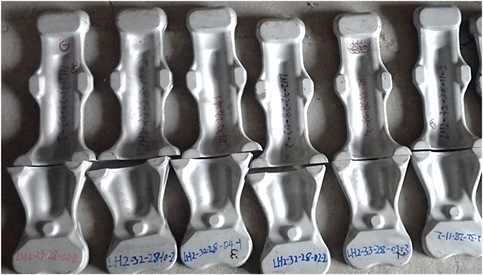
Figure 1. Hand forging of SiC/2009Al matrix composites
图1. SiC/2009Al复合材料自由锻件
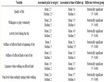
Table 1. Chemical composition of SiC/2009Al matrix composites (mass fraction %)
表1. SiC/2009Al复合材料化学成分(质量分数%)
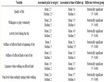
Table 2. Tensile properties of SiC/2009Al matrix composites
表2. SiC/2009Al复合材料拉伸性能
2.2. 试样形式及尺寸
光滑试样如图2所示,划伤缺陷试样形式与光滑试样形式相同,在试样中部位置预制划伤缺陷,划伤缺陷深度为0.15 mm、0.25 mm和0.40 mm,如图3所示。
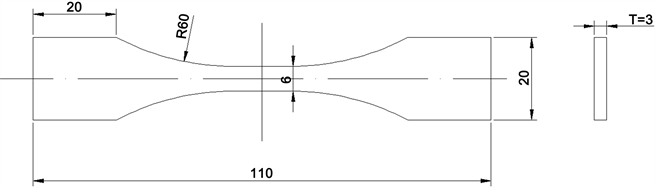
Figure 2. Shape and size of smooth specimen (mm)
图2. 光滑试样形状及尺寸(mm)
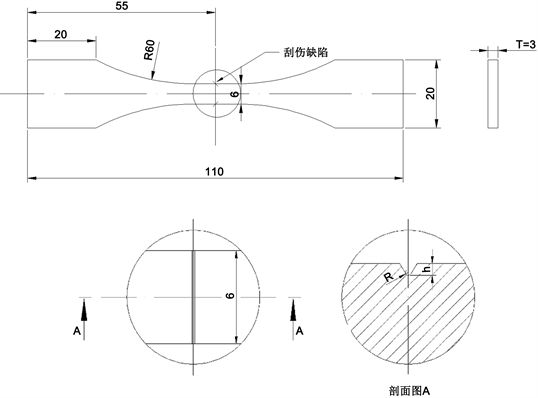
Figure 3. Shape and size of scratched defect specimen (mm)
图3. 划伤缺陷试样形状及尺寸(mm)
2.3. 实验方法
在高频疲劳试验机上进行SiC/2009Al复合材料疲劳性能试验,实验过程按照GB/T 3075-2008《金属疲劳试验轴向力控制方法》标准要求进行。室温大气环境,试验频率80 Hz~100 Hz,加载波形为正弦波,应力比R = −1。采用成组法获得中低寿命区疲劳数据,成组法为3级应力水平,每级应力水平的疲劳寿命应满足95%置信度要求。采用升降法获得107疲劳极限,升降法为5个升降对,3~5级应力水平。
3. 疲劳性能实验结果
通过升降法获得SiC/2009Al复合材料光滑试样和划伤缺陷试样的107疲劳极限,结果如表3所示。通过成组法获得光滑试样和0.25 mm划伤缺陷试样中低寿命区的疲劳数据,采用最小二乘法对成组法和升降法试验数据进行拟合,得到S-N曲线拟合公式参数如表2所示,S-N曲线如图4所示。
S-N曲线采用三参数Stromeyer方程,公式表达式如公式(1)所示。
(1)
其中
为最大名义应力;N为疲劳寿命;A、α疲劳曲线形状参数。
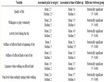
Table 3. Experimental results of fatigue property
表3. 疲劳性能实验结果
*注:因原材料数量限制,划伤深度0.15 mm和划伤深度0.40 mm缺陷试样仅进行了升降法试验,获得了相应的107疲劳极限值,未进行成组法试验,因此,未获得对应的S-N曲线。
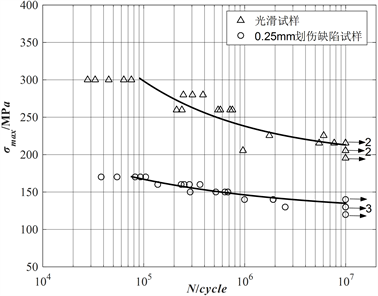
Figure 4. S-N curve of smooth specimen and scratched defect specimen
图4. 光滑试样及划伤缺陷试样S-N曲线
4. 分析与讨论
4.1. 划伤缺陷对SiC/2009Al复合材料疲劳性能的影响规律
如图5所示为SiC/2009Al复合材料不同划伤缺陷深度下的疲劳性能变化规律。可以看出,随着划伤缺陷深度的增加,材料的疲劳性能逐渐下降,试样疲劳性能与划伤缺陷深度近似为负相关的线性关系。
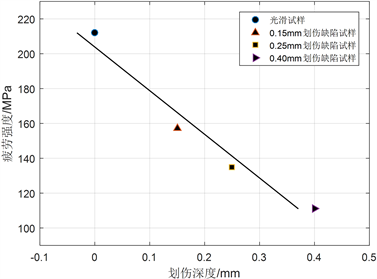
Figure 5. Effect of scratch defect depth on fatigue property
图5. 划伤缺陷深度对疲劳性能的影响
4.2. 缺口敏感性分析
根据实验获得的SiC/2009Al复合材料光滑试样和划伤缺陷试样的疲劳极限,根据公式(2),计算可得用于表征缺陷部位疲劳强度降低程度的疲劳缺口系数Kf。
(2)
式中:Sfl为光滑试样的疲劳极限;Sfk为划伤缺陷试样的疲劳极限。
对于划伤缺陷,可采用有限元分析获得各自的理论应力集中系数Kt。根据疲劳缺口系数Kf和应力集中系数Kt,根据公式(3) [8] ,计算可得缺口敏感性系数q。
(3)
缺口敏感性表征材料对缺口的敏感程度,它能反应疲劳过程中,材料发生应力重新分布,降低应力集中的能力 [9] 。由表4可以看出,随着划伤缺陷深度的增加,缺口敏感性系数q逐渐增大。
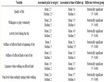
Table 4. The calculation result of Kt, Kf and q
表4. Kt、Kf和缺口敏感系数q计算结果
4.3. Kt-Kf关系式
Kt-Kf关系式经常用于飞机结构的设计,目前大部分金属材料Kt-Kf关系符合线性关系 [10] 。根据表中的Kt和Kf计算结果,获得SiC/2009Al复合材料的Kt-Kf关系曲线如图6所示,由图可知,Kt-Kf呈线性关系,拟合关系式为Kf= 0.526 Kt− 0.0317。
5. 结论
通过对SiC/2009Al复合材料光滑试样和划伤缺陷试样(划伤深度0.15 mm、0.25 mm及0.40 mm)疲劳性能进行研究和分析,结论如下:
1) SiC/2009Al复合材料光滑试样疲劳极限为212 MPa,0.15 mm划伤缺陷疲劳极限为157 MPa,0.25 mm划伤缺陷疲劳极限为135 MPa,0.40 mm划伤缺陷疲劳极限为111 MPa;
2) 划伤缺陷对SiC/2009Al复合材料疲劳性能影响显著,划伤缺陷深度与疲劳性能呈负相关线性关系;
3) 随着划伤缺陷深度的增加,SiC/2009Al复合材料缺口敏感性增大;
4) SiC/2009Al复合材料Kt-Kf为线性关系,其关系式为Kf= 0.526 Kt− 0.0317。