1. 引言
近些年来,随着汽车数量的日益增多,废旧轮胎数量快速增长。目前我国已成为仅次于美国的第二大废旧轮胎产生国家,不断增加的废旧轮胎相应也加大了对资源与环境的压力 [1] 。世界各国在早期最普遍的做法是把废旧轮胎掩埋或堆放 [2] ,而后在废旧轮胎翻新、热解、制造胶粉的方面有了一定的研究进展 [3] 。废旧轮胎直接利用或简单切割的处理方法可以用在 [4] [5] :废旧轮胎挡土墙、护舷、公路防护栏、人工岛礁、筑堤、护坡等。废旧轮胎经过二次加工的工序可用作生产再生胶、热裂解生产燃油、生产胶粉或作为热能利用。随着废旧轮胎数量的日趋增长,轮胎–土复合体的提出,将废旧轮胎二次利用,能够明显改善这一问题。
随着地价上涨,征用土地作轮胎的掩埋/堆放场地越来越困难。另一方面,废旧轮胎大量堆积, 极易引起火灾,造成第二次公害。若将废旧轮胎磨成颗粒状进而制成再生胶,再生胶工艺复杂, 耗费能源多,生产过程污染环境, 造成二次污染等已引起公众关注 [6] 。由此可见,高效、环保再次利用废旧轮胎是一个值得关注的问题,于是轮胎–土复合体由此而出现。但国内外对轮胎–土复合体的抗压、抗剪性能的研究还存在很多空白,所以本文在轮胎–土复合体抗压、抗剪方面设计了多组实验工况,并进行数值分析。
2. 实验准备工作
2.1. 实验材料和设备
为保证试验结果的准确性,选用同一品牌、尺寸的轮胎。在实验材料方面,轮胎为:朝阳牌子午线 [7] 废旧汽车轮胎,轮胎尺寸R22-14.5,且使轮胎的磨损程度相近,最大可能降低因为轮胎造成的试验误差。轮胎及填料参数如表1、表2所示。
2.2. 实验工况设计
1) 轮胎复合结构单体抗压实验工况:在压实度统一为90%的前提下,轮胎–土复合体的内部填料分别为黏土、粉土、砂,分别编号为1组、2组、3组。如表3所示。
2) 轮胎复合结构组合体抗剪实验工况:在压实度统一控制为90%、轮胎–土复合体内部填充料种类统一为黏土的前提下,分别在竖向应力为0.02 MPa、0.04 MPa、0.06 MPa、0.08 MPa进行试验,并分别编号为1组、2组、3组、4组。如表4所示。
2.3. 实验步骤
1) 轮胎复合结构单体抗压强度实验操作步骤:
将轮胎放置于钢板上,在轮胎外壁贴上应变片。然后进行内部填料的添加,填加内部材料时,采用分层填加,分层压实、分层捣实的方法,保证轮胎内部不留空隙。
加载之前,对轮胎–土复合结构体加载1 MPa进行预压(表5)。卸载之后进行正式加载。每级加载
表1. 轮胎参数
表2. 复合体填料参数
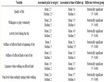
Table 3. The compressive experiment condition of tire-soil composite
表3. 轮胎-土复合体抗压实验工况
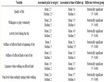
Table 4. The shear experiment condition of tire-soil composite
表4. 轮胎–土复合体抗剪实验工况
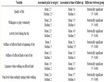
Table 5. The parameters of tire-soil composite
表5. 复合体各项参数
0.5 MPa,加载8级,至4 MPa;卸载每级1 MPa,分4级进行卸载。每级加载卸载对数据进行记录。填满轮胎之后,采用环刀法取样对压实度进行验证。
填筑过程如图1所示。
2)轮胎复合结构组合体抗剪强度试验操作步骤:
放一块钢板在地上作为底板,在底板上放置3根滚轴,在滚轴上方,放置一块承压板,将两个复合结构体A1、A2分别放置于承压板之上,在A2复合结构体上放置一个钢板,分别在两个复合结构体放置两个圆弧承压板,在下面的A1复合结构体的圆弧承压板外侧中心放置横向千斤顶以及与之相连的压力传感器,在上面的A2复合结构体圆弧承压板外侧中心位置放置反力梁,以此来固定A2复合结构体。
在加载之前,先进行预压,竖向加载10 KPa,水平加载5 KPa,再卸载至零。加载时,先将竖向压力分别控制在20 KPa、40 KPa、60 KPa、80 KPa,然后施加水平荷载。控制标准为应变法,横向每变形1 mm,读取对应应变下的水平荷载数值。加载速率为1.0 mm/min,直至复合结构体发生剪切破坏。
轮胎复合结构组合体抗剪试验如图2所示。
3. 试验结果分析
3.1. 轮胎复合结构单体抗压强度试验
竖向变形
各复合体压缩模量及竖向应力–应变关系如表6、图3所示。
由图表可以看出:
加载时,随着应力的增大,三种填充料的轮胎–土复合结构体的应变随着应力的增大成近线性增大;卸载时,随着应力的减小;该复合体的应变随之减小,但没有完全恢复。这说明,该复合体的变形是弹塑性变形,即有一部分为塑性变形,卸载之后,无法恢复;当加载到峰值时,填料为黏土的复合体变形
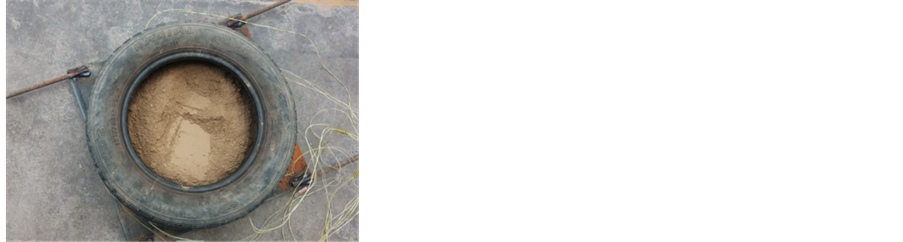
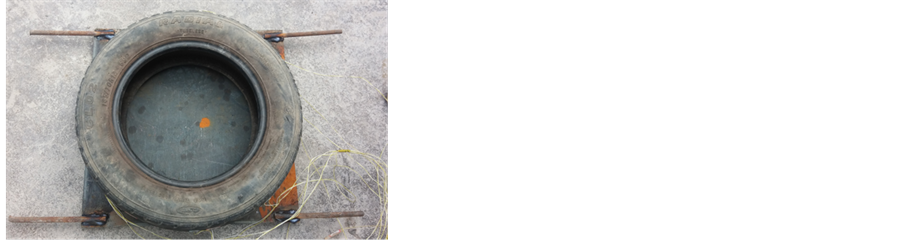
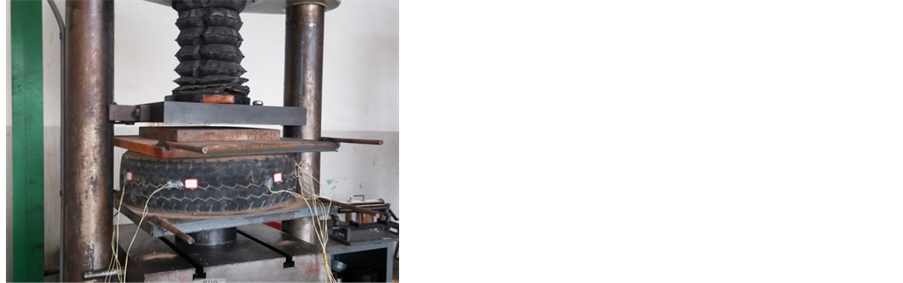
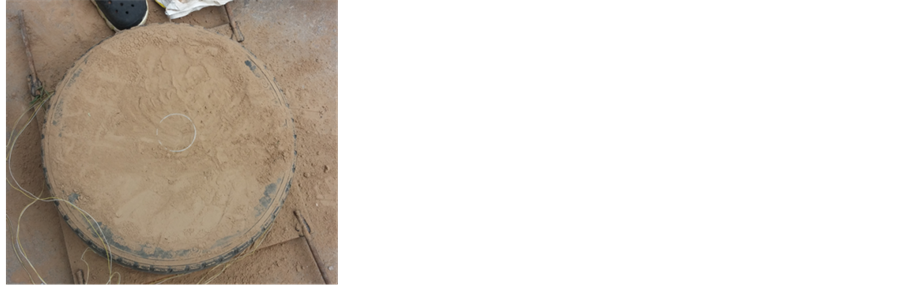
Figure 1. The filling process of tire-soil composite
图1. 轮胎–土复合体填筑过程
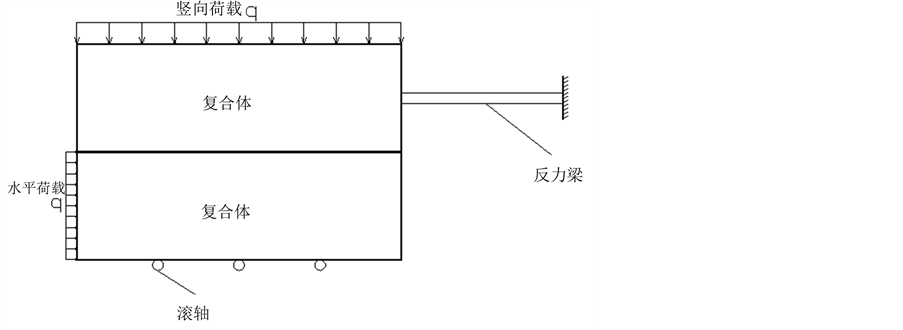
Figure 2. The shear experiment schematic diagram of tire-soil composite
图2. 轮胎–土复合体抗剪试验示意图
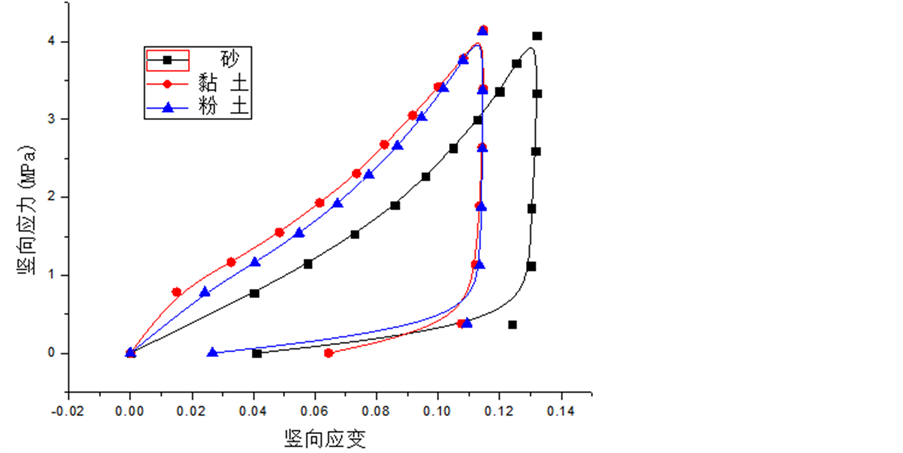
Figure 3. The vertical stress strain diagram of different composites
图3. 不同填料复合体竖向应力–应变图
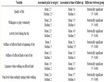
Table 6. Compression modulus and post-press compaction of each composite
表6. 各复合体压缩模量及压后密实度
量最小,填料为砂的复合体变形量最大,这表明:填料为黏土的复合体压缩模量最大,填料为粉土的复合体次之,填料为砂的复合体压缩模量最小;在最后一级荷载卸载阶段,可以看出,填料为粉土的复合体回弹量较填料为粘土的复合体大。这表明:填料为粉土的复合体中的塑性变形部分较填料为粘土的复合体小。
3.2. 轮胎复合结构组合体抗剪强度试验
复合体τ-△L、黏土τ-△L曲线,如图4、图5所示。从图中可以看出:
轮胎–土复合结构体的黏聚力比黏土小4.8 KPa,减小了46.15%。这是由于,复合结构体的相互接触面是由橡胶轮胎和黏土组成的,而橡胶轮胎那部分接触面不提供黏聚力,因此轮胎–土复合结构体的黏聚力比黏土小;轮胎–土复合体的内摩擦角比黏土大14.72˚,增大了83.68%。分析其原因可能是,接触面是由橡胶轮胎和黏土组成的,橡胶材料的摩擦系数较黏土大,因此轮胎–土复合结构体的内摩擦角比黏土大;通过对比黏土和轮胎–土复合结构体的界面特性试验可以发现(图6和表7),轮胎–土复合结
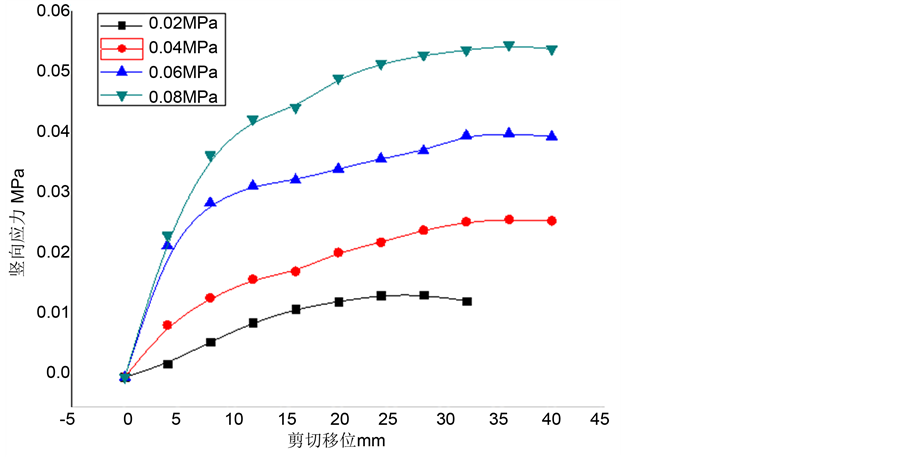
Figure 4. The shear stress and lateral displacement variation curve of composite
图4. 复合体的τ-△L曲线
注:τ为切应力;△L为横向位移变化量。
Figure 5. The shear stress and lateral displacement variation curve of clay
图5. 黏土的τ-△L曲线
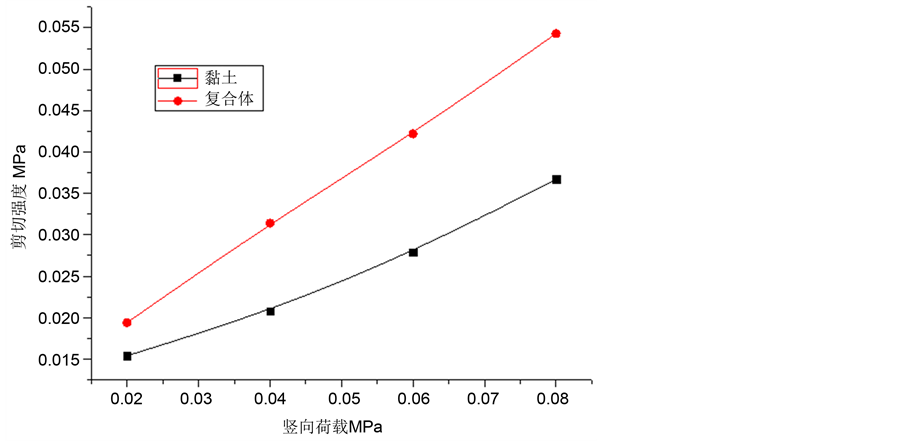
Figure 6. The shear test contrast figure experiment between clay and composite
图6. 黏土与复合体的剪切试验对比图
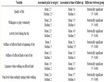
Table 7. The comparison of cohesion and internal friction angle between clay and composite
表7. 复合体与黏土C、ψ值对比
构体能够明显的增大土体的内摩擦角,从而提高土体的抗剪强度。但与此同时,会降低土体的黏聚力,在实际工程运用的过程中,可以通过轮胎–土复合结构体之间的相互捆绑连接来解决。
4. 数值计算模型
4.1. 基本假定
1) 挡土墙墙背填料特性为均质的、各项同性的;
2) 轮胎–土复合体中轮胎外壁和内部填料之间没有空隙,紧密接触。
4.2. 数值模拟主要单元
为了进一步分析轮胎–土复合体在支挡结构中的位移变化情况,本研究采用plaxis [8] [9] [10] 对轮胎–土挡土墙模型进行数值分析,该程序是由荷兰PLAXISB.V.公司推出的一系列功能强大的通用岩土有限元计算软件。
4.3. 模型尺寸及材料参数
挡土墙墙体部分是由8个复合体两两一组呈“梯形”组成。复合体及墙背填料属性如表8所示。
4.4. 计算结果分析
Plaxis数值模拟计算结果,如图7所示。提取1~9号点位移变化,如图8所示。
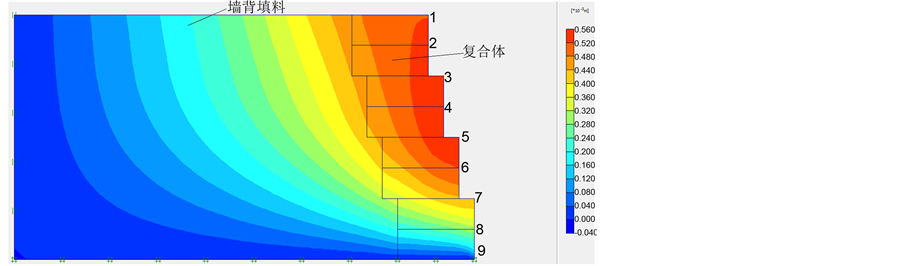
Figure 7. The horizontal displacement change of tire soil retaining wall by numerical modeling
图7. 数值模拟复合体支档结构水平位移变化
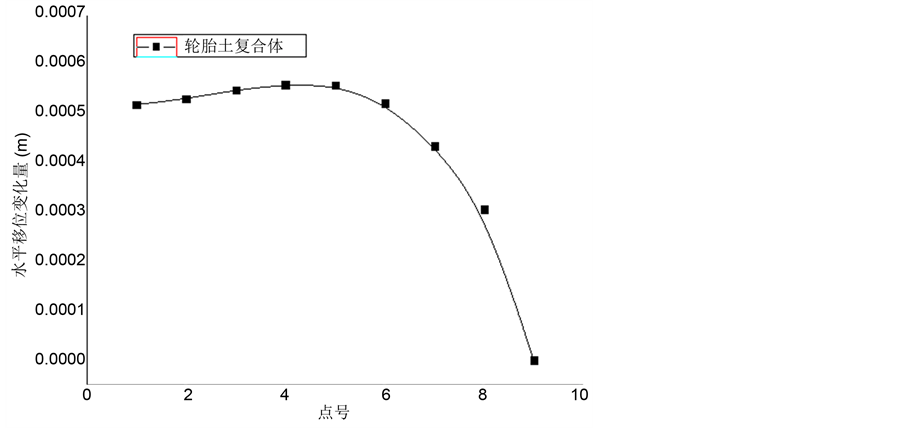
Figure 8. The horizontal displacement change of point 1 to point 9
图8. 1~9点水平位移变化
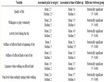
Table 8. The wall back filling properties and composite input by plaxis
表8. Plaxis输入复合体、墙背填料属性
从上图可以看出:
在整体上,1~6号点的水平位移变化量都在0.5 mm左右,水平变化量最大的是5号点,其水平位移变化量为0.558 mm;在7~9号点中,水平位移依次减小,且减小幅度较大,为0.22 mm/点;该支档结构在下方3个复合体中,较为稳定,而薄弱点在水平位移最大处即5号点的位置,因此若对该挡墙结构进行安全性加固,可考虑在挡墙的中上部进行安全性处理。
5. 结论
1) 由于轮胎–土复合体会有轮胎对内部填料提供的一个横向的围压,所以在抗压强度上,会比素土有明显的提高,利用轮胎–土复合体有较高的抗压强度,可以将该复合体用于公路基础、机场跑道等对抗压强度要求较高的地方;
2) 通过轮胎–土复合抗剪强度方面具有较高内摩擦角的特性,可以将轮胎–土复合体用于挡土墙的设计之中,由于轮胎–土复合体是一个弹性体,在地震多发地带,会有着很实际的应用;
3) 该新型材料的提出,有着多方面的现实意义,不仅能提高废弃轮胎的二次利用率,而且在抗压、抗剪方面有着多方面的实际应用,具有很好的应用前景。