1. 引言
齿圈、信号齿圈、惯性环等环型工件具有传动、承载、惯性调节等作用,广泛应用于交通和汽车行业。近年来环型工件在生产过程中自动检测越来越重要 [1] ,不仅包括小型齿圈,尺寸规格包括直径100~400 mm之间的许多规格的不同环型工件需要快速准确检测,见图1。
在滤除缺齿、去重槽等特殊区域后,环型工件的圆度测量是环型工件测量的重要内容。调研发现,目前环型工件圆度测量大约存在下面几种检测方法:
1) 三坐标测量仪:利用三坐标测量仪的测量方法适应性较差、测量效率不高,不适合用于环型工件生产过程中的在线检测。
2) 激光三角测量法 [2] :激光三角测量法是利用激光技术进行测量的传感器。它由激光器、激光检测器和测量电路组成,一般适用于高精度、短距离的测量。本文研究发现,该方法在用于环型工件生产过程中的在线高精度检测时具有下面问题:激光三角测量法一般用于单目标点的位移测量,如果采用多个设备同时对多个目标点(比如为了结果精确,本文要求同时测量的测点包括:参考点、内圆边缘、齿底边缘、齿顶边缘等)的位移测量,不仅价格昂贵,数据之间的同步非常困难;虽然也有单个激光三角测量
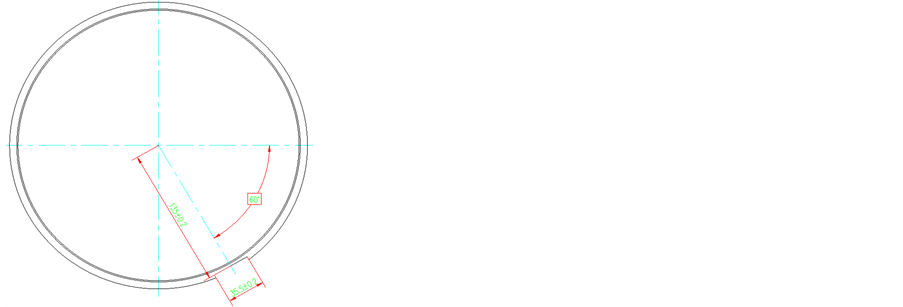
Figure 1. Ring parts (ring gear, signal ring gear, or inertia ring)
图1. 环型工件(齿圈、信号齿圈、惯性环)
设备能对多个目标点同时进行测量,但是对待测的目标点的空间位置要求苛刻,很难满足。
3) 机器视觉:机器视觉能够自动测量产品的外观尺寸(包括微结构尺寸),比如外形轮廓、孔径、高度、面积等尺寸的测量,具有非接触的特点,测量过程不会受到测头、测力、相干光等因素的影响。齿轮、螺纹、凸轮等均是机械制造业中常用的重要零件,由于这些零件形状复杂、参数繁多,用常规通用仪器检测精度和效率较低,通常采用专用测量仪器,测量过程非常复杂,其成本高。随着光电技术和计算机应用的发展,机器视觉在环型工件的测量和检测方面越来越重要,该方法不仅能满足工件的检测要求,而且高效、精确、和灵活,表现出较大优势 [3] 。根据采集图像的传感器类型,这类测量总体上可以分为两类:① 基于面阵列传感器的环型工件测量,该方法对于测量对象多个位置一次曝光成像,得到的位置及相对位置确定,但是该方法要求测量对象尺寸不大,否则成像精度不高。② 基于线阵列传感器的环型工件测量,该方法将有限像素排列(一般1至3行),对测量对象的线型区域进行高精度扫描,由于相机和测量对象的相对移动,将每次扫描的线型图像进行拼接,即可得到整副图像。该方法最大特点是有针对性,提高了检测精度,但是该方法要求测量对象与相机之间有相对运动。
目前,基于机器视觉的环型工件尺寸检测的应用和研究大多局限于面阵列传感器的方法,这种方法相对简单可靠,缺点是覆盖范围小,一般不能对直径大于300 mm的环型工件进行高精度的检测 [4] [5] [6] 。
采用线扫描机器视觉的方法不仅可以提高检测精度,而且可以将多规格环型工件检测任务采用分治的方法分配给不同检测设备进行检测,使得多规格环型工件高精度检测成为可能。
2. 环型工件检测任务分配方法
由于生产的环型工件类型不同,不同类型的待测量的工件的尺寸形成了某个空间的一个分布,比如图2描述了一个测量任务分布。
期望采用单台测量设备对众多不同类型的环型工件进行高效、精确的测量并不现实。为此,本文设计了可调式测量系统ARMS,使得每套ARMS系统在自己的测量空间内高效、精确。而整个测量任务由不同参数的多套测量设备完成。为了充分发挥测量设备功能,减少设备使用量并降低运行成本,设计了环型工件检测任务分配方法RMTGM,该方法包括3部分:① 确定检测任务、② 确定检测设备工作条件、③ 分组计算。
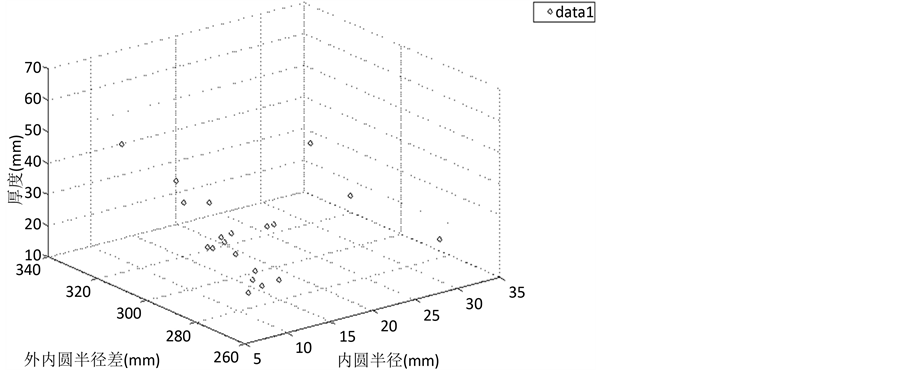
Figure 2. Distribution of a group of parts to be measured
图2. 一批待测环型工件尺寸分布
2.1. 确定检测任务
首先要确定检测任务,其中包括:检测对象类型、检测对象尺寸范围、每类检测对象的检测物理量、检测质量要求与分级标准等。本文检测对象包括大小不一的各种环型工件,部分待测工件列表如下表1。
本文检测内容主要包括对齿圈、质量环、信号环等工件的内圆圆度、齿顶圆圆度、齿根圆圆度进行检测。检测的要求比较苛刻,主要包括:
1) 测量对象尺寸范围大:外圆直径100 mm至400 mm,厚度1 mm至40 mm;
2) 测量精度高:误差在0.01 mm以内;
3) 测量效率高:单次测量时间不超过3秒。
2.2. 确定检测设备工作条件
单个设备具有测量特定范围,本文设计的测量系统ARMS最大有效视野60.0 mm,视野的起点和终点、镜头的最优成像位置等则作为设计参数有待确定,而参数受到如下工作条件约束:
1) 工件上表面必须位于镜头光轴上最优成像位置的±2.5 mm之间;
2) 工件的内圆边缘必须位于镜头视野以内;
3) 工件的外圆边缘必须位于镜头视野以内。
2.3. 待测工件分组计算
给定一批待测工件,首先可以分成两类:可以采用本文设备进行测量的工件,和不可以采用进行测量的工件。对于这些可以被测量的工件(假设M个),一定存在一个最小的测量设备数目N (N > 0且N ≤ M)和这N个设备的一组设备参数,使得每个能够被测量的工件满足测量要求并能够实施测量。
这是一个混合整数目标优化问题(MINLP),可以利用文献 [7] 提供的方法进行求解。基本思想是:
1) 产生合法解群,评价,进入迭代。
2) 修正合法解群,再评价,计算收益,更新修正方法并修正解群,本次迭代完成。
3) 返回继续迭代或输出最优解。
3. 自动圆度检测系统
3.1. 系统硬件方案
将零件推送到旋转平台的中心后,位于旋转平台下方的电磁吸环上电产生磁场,将工件固定在旋转平台上并随之转动。旋转平台是磨光的玻璃材料制造,其下表面固定有标准尺寸的参考圆盘,理论上要求参考圆盘的中心与旋转台转动中心重合,而实际上可能随旋转中心跳动。平台上方布置有1台高精度
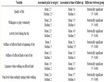
Table 1. A set of parts to be measured
表1. 一组待测环型工件
(12 K)线扫描CCD相机,并配置有双侧远心镜头以减少畸变。旋转平台下方布置有高强光LED光源及电磁吸环。线扫描CCD相机在LED背光环境下对工件表面摄像后得到工件的尺寸信息。旋转平台带动高精度旋转编码器并对于相机进行触发。相机的数据传到电脑进行分析,得到工件的内外圆度等信息,并进行表达、存储、显示、查询和质量判级等。图3是系统示意图。
3.2. 基本原理与精度计算
首先考虑理想情况。假设旋转台的转动是理想的,其转动轴线不发生跳动,转台转动轴线在测量平面的投影为O点;再假设系统经过调节,使得①参考盘的中心与O点重合,且②扫描线或其延长线经过O点,见图4。
理想情况下,工件圆度的测量描述如下:
1) 在转台旋转1周的过程中,依次在图像中搜索待测p点和参考圆盘边缘q点,利用它们的像素坐标,转换得到各自极坐标序列Xp和Xq;
2) Xp-Xq,得到待测圆与参照圆边缘相对位置差序列dR;
3) dR加参照圆盘的半径r0,得到待测圆的极坐标序列;
4) 将极坐标轨迹数据转换为直角坐标下的轨迹坐标;
5) 利用最小二乘法,进行圆度拟合,得到圆心和圆度。
假设旋转台的转动轴线在X方向可能发生跳动。由于待测p点和参考圆盘边缘q点的相对位置不变,上述圆度计算方法依然成立。
假设旋转台的转动轴线在X和Y方向都可能发生跳动,且扫描线或其延长线并不经过O点,上述圆
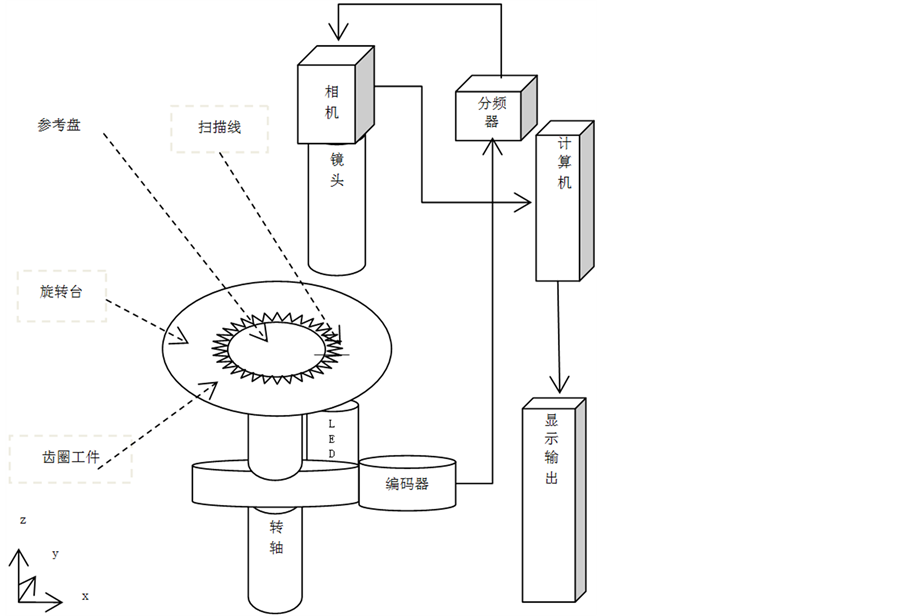
Figure 3. Automatic roundness measuring system
图3. 自动圆度检测系统(ARMS)
度计算方法具有一定的误差。
假设转动轴心在Y方向最大跳动位移为t (本文中,t = 5 um),参照圆盘中心Y方向偏移T (本文中,T < 0.5 mm),环型工件半径为r,则引起的误差取决于r、t、T、和检测面与扫描线之间夹角a这4个量的大小,如图5所示,误差分析如下:
(1)
假设T = 0.5 mm,环型工件直径为r = 200 mm,则e = 0.0006375 mm。
假设T = 1.5 mm,环型工件直径为r = 200 mm,则e = 0.0056626 mm。
计算表明,由于转动轴心的跳动小,所以对于测量的影响也很小;相比之下参照圆盘的固定位置非常重要,如果参照圆盘的固定位置适当,使得参照圆盘中心接近实际转动中心,测量误差是可以容忍的。
本文采用了E2V AVIIVA UM8 系列线阵相机。其传感器为N = 12 K的线阵CCD传感器,单个感光CCD尺寸为5 um*5 um,总长为:
(2)
远心镜头的放大率K = 1.0,其物方视野FOV = 61 mm。单个像素对于的视野为:
(3)
计算表明,如果2个像素能区分和识别出特定目标,即可达到预定0.01 mm的精度,系统分辨率符合应用需求。
3.3. 扫描速度计算
相机扫描速度决定了图像纵向的分辨率,如果扫描速度太慢,数据取样少,容易引入随机误差;如果扫描速度太快,不仅处理的数据量大,而且给毛刺的滤除带来困难。测量要求t = 3秒完成一个工件的测量,每个圆度测量要有N = 256个采样点。实验发现,为了滤除毛刺等干扰,每个采样点至少包含K = 36行像素,并且采样点之间间隔至少为9*K = 36 × 9行数据。相机的采样行频至少为:
(4)

Figure 4. Ideal measurement of roundness
图4. 理想转台上检测圆度
代入数据,得到相机的行频30720行/秒。
3.4. 边缘检测与目标定位
要求定位的目标主要包括4部分:参照盘边缘、工件内圆边缘、齿底、齿顶等。在这些目标识别定位之前,首先要进行图像预处理、边缘检测、以及毛刺滤除处理。
图像预处理利用特定滤波器来改善与噪声有关的边缘检测的性能。一般而言,滤波器在降低噪声的同时也导致了边缘强度的损失 [7] ,同时滤波器有较大的计算开销,因此滤波器要谨慎使用。本文采用了具有区域选择性和方向选择性的滤波算法,用较小计算代价完成滤波任务。
由于本应用只涉及一定方向角的纵向边缘,为了提高计算速度,特简化边缘识别算法。主要分2步完成:
1) 计算梯度。根据实际需求,只需要计算特定方向上灰度的梯度即可,而这个特定方向由以前几帧图像上边缘的切线方向,以及一个±30以内的变化决定。
2) 非最大值抑制。横向搜索最大梯度位置,并利用历史数据对该位置的正确性进行初步判定。
由于涉及的环型工件的边缘可能毛刺,必须在图像中将毛刺滤除,然后再进行边缘检测。本文统计出毛刺的宽度w范围在0.05 mm至1 mm之间,换算为像素的个数为:
(5)
带入数据,得到毛刺纵向宽度大约3到7个像素。
1) 检测边缘,得到边缘位置;
2) 以宽度3~7个像素对于边缘进行滤波;
3) 得到滤除毛刺后的边缘位置。
最后将滤除毛刺后的边缘位置进行记录和收集,这些数据在工件扫描完成后用于计算圆度并进行质量判定。一个工件检测流程图见图6所示。
4. 检测系统测试与分析
本文在6核2.40 GHz的Xeon E5645 CPU和16 G内存、Windows7的工作站上实现了系统并进行了
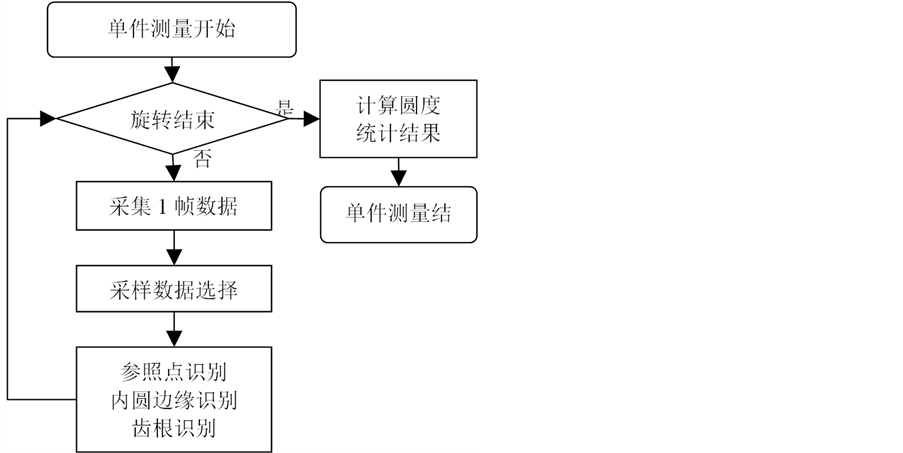
Figure 6. Flow chart of roundness detection
图6. 圆度检测流程图
ARMS系统主界面截图
Figure 7. Curve: system result of standard experiment
图7. 标准试验系统结果曲线
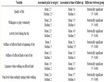
Table 2. Comparison between CMM results and ARMS results
表2. 三坐标CMM测量值与本文ARMS测量值对照表
实验,如图7所示。
表2是6个环型齿圈测定结果与三坐标测量结果对照表,系统测量平均误差6.054 um,单次测量耗时3.0秒。
5. 结语
设计了一种多规格环型工件检测任务分组方法和一种基于线阵列传感器的自动圆度检测系统,实现了对半径100 mm至400 mm的环型工件进行分组并分别进行内圆、齿根圆、齿顶圆进行非接触式测量。系统采用参考盘对机械振动、转轴跳动进行了分析,并设计了参照圆盘进行滤除。理论分析和实际使用结果表明,ARMS和RMTGM 配合能很好完成直径100 mm至400 mm、厚度1 mm至40 mm环型工件圆度的在线检测任务,系统尺寸测量的精度达到±0.01 mm。
如果检测精度要求更高,可从下面几点改进:① 本文采用了12k像素的相机,如果采用16 k相机,可增加系统精度;② 本文采用了白色LED高亮线光源,如果采用单色光,特别是蓝色光,并采用平行背投方式给远心镜头打光,可能提高系统精度;③ 测量算法方面存在提高性能的空间。这些是本文以后工作研究的内容。
基金项目
本文受到国家自然科学基金项目面上项目(51174151)资助,在此表示感谢。