1. 赛车轮辋轻量化的意义
由于时代的进步与经济发展,各种汽车赛事正在进入普通百姓生活。国内外赛车竞技水平的不断提高,对赛车轮辋的结构性能提出了更高的要求。轮辋是车辆行驶系统中车辆与地表间的主要受力部件,它起到了承载、驱动、制动及转向等作用,对车辆行驶的动力性、操纵稳定性以及制动安全性等起到关键作用。
研究以FSC比赛为参照,对FSC赛事中轮辋断裂事故状况进行受力分析,将分析得到的各种数据作为赛车轮辋重新设计的重要依据,在实现轻量化的同时,提高赛车的整体性能。
2. 轮辋结构及选用材料
轮辋和轮胎一般是配套组合使用,轮胎是弹性件,安装在轮辋外缘,具有良好的变形恢复能力和附着能力,行驶时可以减小车辆对路面的压应力,从而将车辆运动时的能量损耗降至最低。轮辋是车辆行驶中重要的受力部件,传导车辆与地面之间的应力。
对于FSC赛车而言,铝合金轮辋比钢轮辋更为适合,较轻的质量在高速运动中变形较小,形成的惯性阻力小,使赛车有较好的直线行驶性能。另外,铝合金材料散热性好,有助于赛车的轮胎热衰减及提升其制动性能。利用三维造型软件UG建立13寸铝合金赛车轮辋模型,如图1所示。
3. 轮辋冲击试验
轮辋冲击试验是模仿汽车在行驶过程中车轮的侧面受到外界力的冲击而发生的轮辋特性变化。根据国家标准,不同汽车生产厂商有不同的试验方法,目前广泛使用的标准是进行13˚方向的冲击试验。
轮辋冲击试验系统中主要包括轮辋、轮胎、冲击块及悬挂装置,轮辋通过螺栓与试验台连接,同时
将轮缘处设定为固定面,主要研究对象为赛车轮辋。
3.1. 材料属性定义
此次赛车设计选用的车轮轮辋为整体铸造铝合金轮辋,采用的材料为A356型号[1] 。材料属性相关参数如表1所示。
3.2. 冲击载荷确定
冲击块重力是根据其质量计算确定的,而冲击块质量按D = 0.6 W + 180得到,冲击试验需要的FSC赛车部分整车参数为:前轴载荷为120 kg,后轴载荷为130 kg,单个轮辋最大静载荷75 kg。根据冲击块质量计算公式可知,重力为2.20 kN。该模型为二分之一模型,因此模型中冲击块的质量为1.10 kN [2] 。
3.3. 冲击块运动数值模拟结果及分析
首先确定冲击块约束关系,假设冲击块为刚性体,通过研究质心的运动模拟冲击块运动历程[3] 。图2、图3和图4分别为冲击块质心在Z方向上的位移、速度和加速度的时间历程。
从图2位移曲线可以看出,冲击块在约12 ms时达到最大位移2.12 mm,此时位移也是轮辋轮缘在竖直方向上的最大变形量,随后冲击块Z方向位置回升,这表示冲击块由于受到轮辋内力反向作用力而向上反弹,之后在重力的影响下冲击块的Z向正向速度逐渐衰减,图像上表现为斜率逐渐减小,并且有向下加速的趋势。
从图3速度曲线可以看出,冲击块与轮辋接触后,下落速度减小,冲击块下落过程中,受到轮辋弹性阻力,速度不断降低,直到速度降至零,而从4 ms以后,轮辋形变而产生的阻力和冲击块的所受重力合力方向向上,冲击块开始反弹,速度由负转为正。
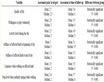
Table 1. The relevant parameters of material properties
表1. 材料属性相关参数
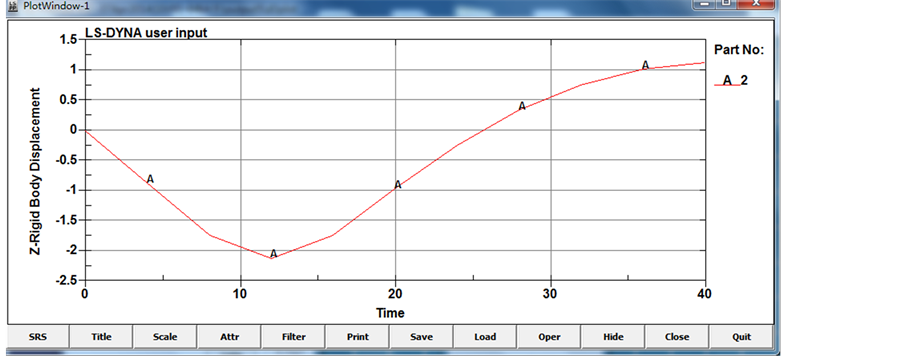
Figure 2. Displacement curve of impact block Z-direction
图2. 冲击块Z方向的位移曲线
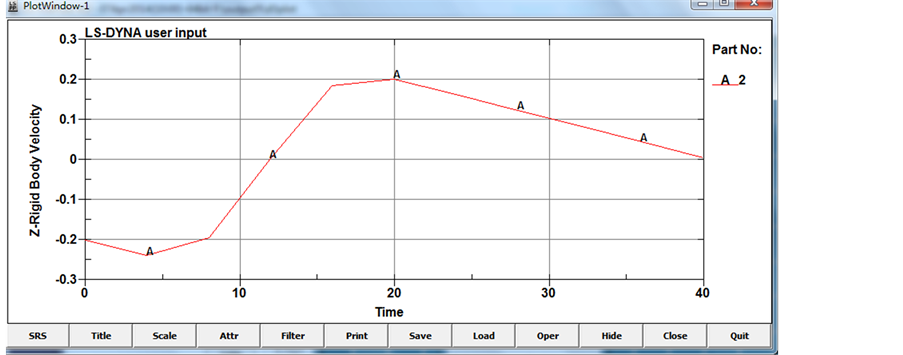
Figure 3. Velocity curve of impact block Z-direction
图3. 冲击块Z方向的速度曲线
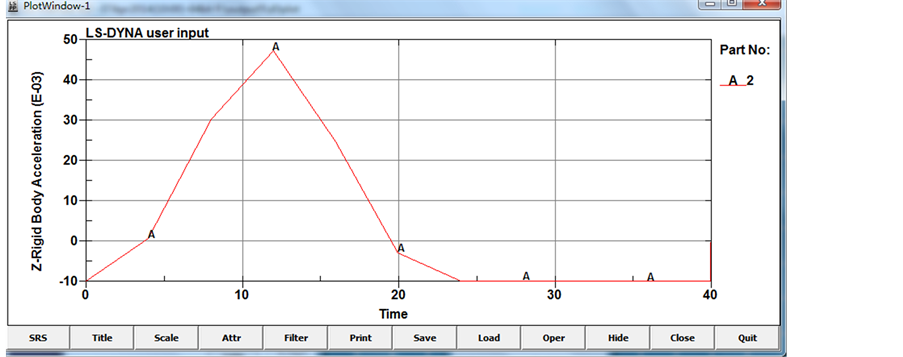
Figure 4. Acceleration curve of impact block Z-direction
图4. 冲击块Z方向的加速度曲线
从图4速度曲线可以看出,冲击块加速度曲线与它所受到的合力曲线成平移关系,而冲击力实际是合力中的主要分力,其过程也基本表现为四个阶段:
第一阶段大约为0~4 ms时间段,在此阶段内,冲击块在与轮辋接触前合力基本平衡。
第二阶段大约为4~12 ms,在此阶段内,冲击块受到的阻力迅速增大。
第三阶段大约为12~24 ms,在此阶段内,阻力基本平稳但缓慢增大,至13 ms时达到峰值,阻力使冲击块下降的反向加速度增至大约为5倍重力加速度。
第四阶段为24 ms以后,在此阶段内轮辋内力释放,冲击块受到的正向力也快速下降,此阶段实质是冲击块的卸载阶段。
综合冲击块Z向的位移、速度和加速度曲线,数值模拟体现了冲击块下落与反弹的两个变化阶段,同时反映了FSC赛车轮辋的冲击变形特点。
3.4. 冲击效果仿真及应力分析
利用LS-DYNA的后处理软件LS-PREPOST的影像模拟功能,可直观地模拟整个运动过程。当冲击部位在轮缘正上方两轮辐之间,试验分析了0 ms、3 ms、12 ms及24 ms时轮缘受冲击边缘受力情况,图5至图8中反映了各时段轮辋vonmise应力分布变化。
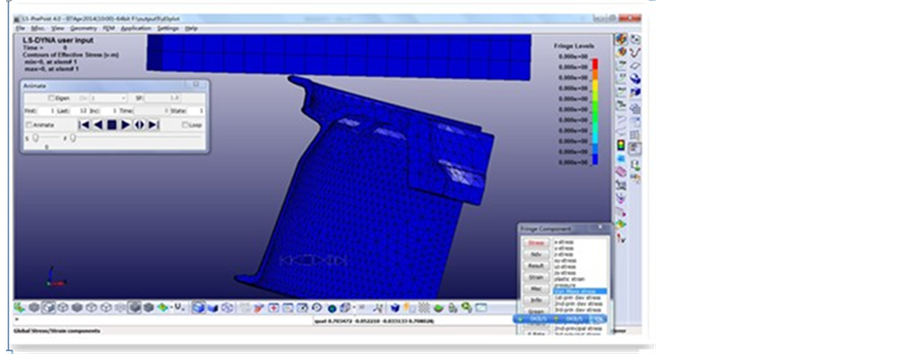
Figure 5. Impact stress map of rim edge at the zeroth millisecond
图5. 0 ms时轮缘受冲击边缘应力图
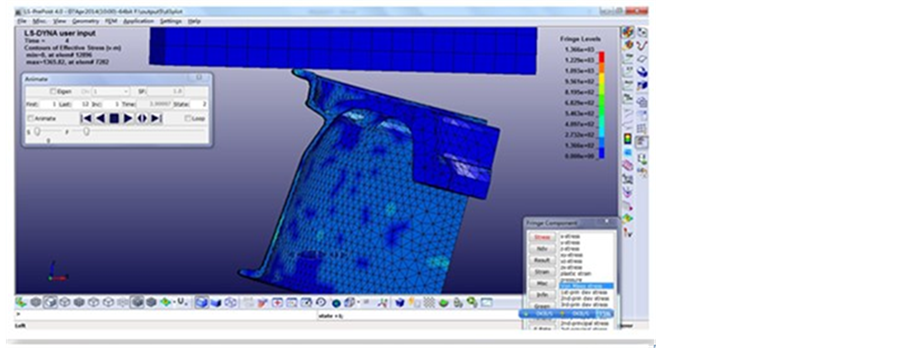
Figure 6. Impact stress map of rim edge at the third millisecond
图6. 3 ms时轮缘受冲击边缘应力图
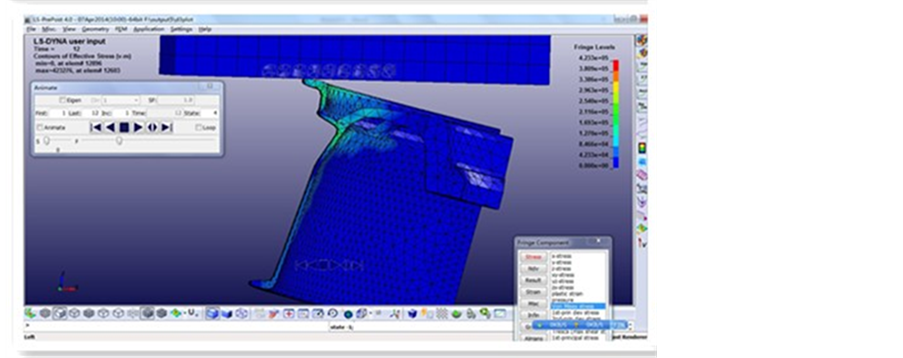
Figure 7. Impact stress map of rim edge at the twelfth millisecond
图7. 12 ms时轮缘受冲击边缘应力图
轮辋与轮辐分离程度以及轮胎与轮辋配合部位漏气情况是判定轮辋冲击试验结果的主要标准[4] 。因此结合冲击位置,图8所示阶段的变形与受力情况是研究轮辋重点分析时刻。
从应力分布变化来看,冲击块与轮缘接触部分及轮辐与轮辋连接区域在3 ms时出现明显应力集中,这时冲击块刚刚接触到轮辋,在3 ms之后应力扩展至周边,到12 ms左右时冲击块达到最低位置,对应的最大等效应力达到4.2 MPa。
4. 轮辋的改进
通过对轮辋的应力图、变形图和冲击试验结果的分析,轮辐靠近安装台处的应力较小,整体寿命远超出使用要求,可对轮辋尺寸进行优化,减轻轮辋质量[5] 。
4.1. 改进方法
利用ANSYS workbench Shape Optimization模块对轮辋进行结构优化,得到材料最优使用情况[6] -[8] 。经过几次模拟运算后,因螺母和轮胎匹配的关系,部分优化区域实际无法进行尺寸更改,只有在辐条两端进行适当的调整,如图9所示。
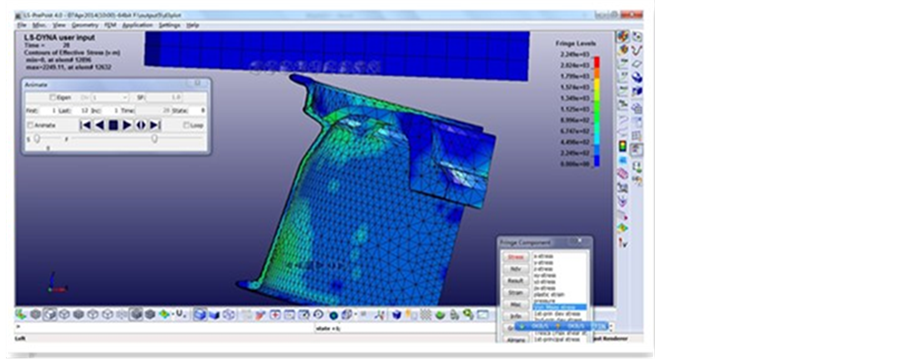
Figure 8. Impact stress map of rim edge at the twenty-fourth millisecond
图8. 24 ms时轮缘受冲击边缘应力图
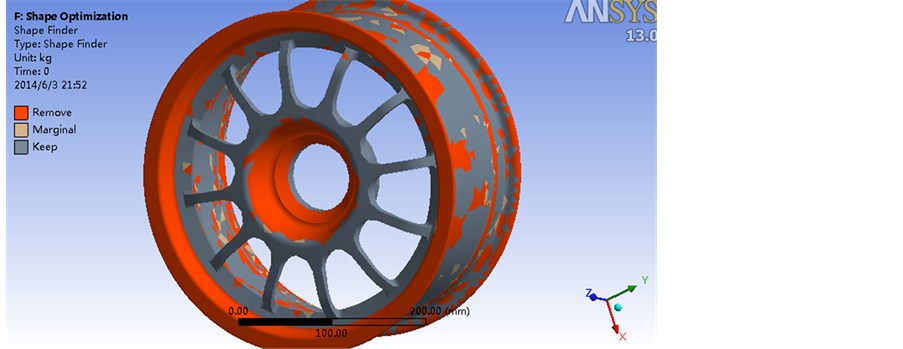
Figure 9. Analysis of ANSYS optimizing area
图9. ANSYS优化区域分析
(a) (b)
Figure 10. Comparison of wheel rim quality lightweight: (a) Quality before improved; (b) Quality after improved
图10. 10 轮辋轻量化前后质量对比:(a) 改进前质量;(b) 改进后质量
4.2. 改进结果
结合冲击试验模拟结果,单个轮辋经计算可减重0.3 kg左右,占总重量的10%左右,图10为改进前
后质量对比结果。
另外,根据模拟弯曲疲劳试验,可以得到轮辋最低寿命仍可达5.9107次,虽然改进后的轮辋安全系数有所降低,但仍能达到2.2467,可以满足使用的要求。
5. 总结
本文主要借助计算机仿真,从结构设计方面对轮辋进行受力模拟,为轮辋实际设计提供依据。仿真情况与道路车辆仍有一定的偏差,但通过后续数据采集补充,进一步修正仿真模型和参数,可以更加真实模拟道路状况,为提升赛车性能提供设计依据。