1. 引言
目前传统的浓缩液桶内干燥装置多采用热风循环的干燥方式,需要将烘干液体的钢桶放置在干燥室内,干燥室侧面通过循环管路与风机和加热器连接,由加热器加热干燥室内的空气并通过风机进行循环 [1] ,钢桶内液体蒸发产生的蒸汽通过顶部管线经冷凝后排放。采用传统的烘干方法,涉及到换热器加热空气,再由热空气经风机循环将热量传递,另外,蒸发出的蒸汽还含有水分,如不及时排出会影响后序的过滤处理,影响排出气体的安全性。
随着经济进展和社会进步,我国的垃圾产生量也在逐年增加浓缩液处理方法是一种常见的化学处理方法,它可以将液体中的溶质浓缩到一定程度,从而达到分离、提纯等目的。利用物质的挥发性差异,通过加热或减压等手段将浓缩液中的溶质浓缩到一定程度。浓缩液处理方法广泛应用于电力行业,是一种非常重要的技术手段。在实际应用中,常用的浓缩液处理方法包括蒸发、回灌、膜蒸馏等技术进行处理。但都有一定的应用范围和弊端,其问题主要包括:处理成本高,处理效果不稳定 [2] ,处理难度大,操作难度大,处理效果不理想 [3] ,产生负面影响。
针对上述现有技术的不足,研究和开发了一种便于快速加热蒸发且能保证排放安全的浓缩液桶内干燥方法及其装置,并在后期进行了验证试验证明其系统的可行性。
2. 电厂浓缩液来源及系统功能
电力行业所产生的浓缩液主要来自于垃圾发电、火电和核电等领域。
2.1. 垃圾发电领域
生活垃圾进入焚烧或裂解处置前都会在垃圾贮坑内堆发酵3~7天,以使垃圾熟化并沥除水分,从而提高垃圾热值,在这个过程中,将会产生大量的垃圾浸出物。其中有机污染物、无机盐和金属离子的浓度均非常高,COD、BOD、氨氮浓度也都相对较高(COD可达40,000~80,000 ppm),并且生化性较差 [4] ,若处置不当会造成更严重的二次污染。垃圾经过焚烧和裂解后会产生大量的氨氮元素渗滤液,此废液不能通过常用手段进行降解,氨氮含量过高容易导致土壤碱性失衡和电离子失衡从而引发动植物和生态圈的突变,带来严重污染问题。
2.2. 火电领域
随着国家对于水资源的日益重视,零排放技术在全国范围内都得到了广泛的运用。火电站脱硫废水零排放工艺中会通过脱硫废水通过膜浓缩法、蒸发浓缩等深度处理方法,转化为浓度倍数较高的浓缩液。浓缩液盐含量高、成份复杂,进一步处理非常困难。
2.3. 核电领域
膜分离技术是核电厂目前常用的放射性废液处理技术,通过反渗透膜技术,放射性核素和其他大粒径物质,在膜的进液侧被截断,变成浓缩液,从而达到了分离液体和放射性核素的目的。核电站化学废液大部分来自于放射性化学实验室地面疏水、进行放化样品分析后产生的废水、化学去污排水和化学清洗废水等,核电厂浓缩液的水质较差、杂质多、电导率高,且放射性活度浓度可能较高 [5] ,处理处置困难。
2.4. 系统功能
此系统用于处理核电站放射性化学废液、核电站浓缩液、核电站产生的蒸残液、火电站脱硫废水零排放等使用反渗透膜产生的浓缩液、垃圾发电厂的垃圾渗滤液等浓缩液。将电力行业废水处理系统所产生的浓缩液采用桶内红外烘干的方式,将浓缩液烘干为滤饼,再将滤饼进一步的处理或者处置,从而达到固液分离的目的。
3. 干燥系统及装置介绍
3.1. 干燥系统简介
浓缩液干燥处理方法的原理是利用物质的挥发性差异,通过加热或沸腾等手段将液体中的溶质浓缩到一定程度。但不同类型的浓缩液和渗滤液采用干燥方式不同,传统型干燥工艺有操作复杂、危险系数高、所耗能量大、干燥周期长、干燥后产物含水率指标不稳定等一系列问题。针对上述问题我们在现有工艺上研究设计了一款能适用于电力行业大多数浓缩液的干燥工艺,此工艺采用“负压 + 红外线加热”干燥模式,经过参数调后试验结果和工艺成本相比现有工艺优势明显。
3.2. 干燥装置工艺流程
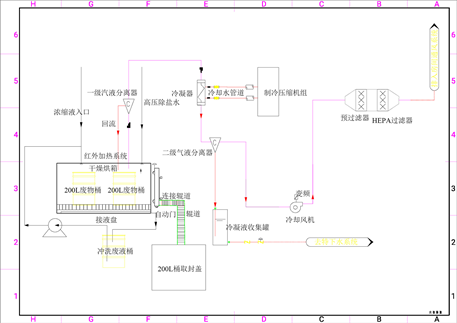
Figure 1. Process diagram of drying system in the concentrated bucket
图1. 浓缩液桶内烘干系统工艺流程简图
浓缩液桶内干燥系统主要包括辊道、烘箱、冷却风机、红热加热装置、冷凝装置、阀门、冷凝液收集罐等设备。浓缩液干燥系统具有全自动控制系统,能实现进液、预热、干燥、烘干、冷却、冲洗全过程的自动化。浓缩液烘干冷却完成后将自动停止运行,发出信号。系统使用方便、加热安全可靠。其工艺流程简图见图1所示。系统的运行过程主要包括浓缩液的接收和就位、系统预热、烘干、冷却、烘干废物移除、高压除盐水冲洗及回流等过程,浓缩液桶内烘干系统工艺流程简图见图1。
3.2.1. 浓缩液的接收和就位
首先取掉200 L废物桶的盖子,将连接辊道下降250 mm,开启烘箱门,将连接辊道上升250 mm,由启动辊道、将废物桶运送至烘箱内。若工艺为装有浓缩液的废物桶直接进入烘干系统可进行直接烘干;若工艺设置为未装浓缩液的桶进入烘箱,则通过定位由浓缩液泵打入浓缩液到200 L废物桶。将旋转辊道再次下降250 mm,关闭烘箱的密封门,启动气缸顶紧烘箱门,使烘箱门与烘箱体之间密封严实。
3.2.2. 系统预热
200 L废物桶通过辊道传输烘干系统内部,浓缩液通过浓缩液入口输入到200 L废物桶中,烘箱密封门关闭且密封后,将红外加热装置产生的热量传递给烘箱以及浓缩液,使烘箱达到设计温度120℃。烘箱在预热阶段也将运行冷凝除湿系统,在启动循环风机的同时启动冷凝装置以及冷却风机,将烘箱内吸热吸湿的部分循环热空气抽排入冷凝装置。
3.2.3. 负压烘干
烘箱在预热结束后,烘干系统维持正常运行程序。红外加热装置产生的热量不断传递给烘箱以及浓缩液,同时冷凝系统将不断除去热湿空气的水分,最终使浓缩液干饼中含水量 < 0.05%。通过变频冷却风机使系统保持负压。一级汽液分离器将加热蒸汽中夹带的水分分离重新回流至200 L废物桶中。蒸汽通过冷却后进入二级汽液分离器,冷凝装置为列管式冷凝器,将热空气冷却至20℃,冷却后的气体通过冷却风机抽排入就地高效过滤器组件进行处理。经过就地过滤的气体最终将汇入厂房通风系统集中处理。
3.2.4. 冷却
冷却风机的抽气将维持烘箱内呈微负压,冷凝液在的冷凝液收集罐中的液位达到一定高度时,排至特下水槽或者暂存罐中。当浓缩液烘干后,红外加热,冷凝器及冷水机组正常运行,冷凝系统不断将热空气和热蒸汽所带出的烘箱热量吸收,最终将烘箱冷却至常温。
3.2.5. 烘干废物的移出
烘干后盛满盐饼的200 L废物桶可通过放射性或者含水率检测,其表面剂量率不超过0.2 mSv/h,盐饼的游离水含水率 < 1%送至暂存或者处置。烘箱冷却至常温后,开启烘箱的密封门,通过上升连接辊道,开启辊道将2桶烘干废物转移出烘箱。
3.2.6. 高压除盐水冲洗及回流
当系统长时间运行以后,干燥烘箱内部可能被浓缩液中的金属或者放射性核素等污染,此时,可采用高压除盐水对干燥烘箱内部进行冲洗,冲洗后的废水通过干燥烘箱底部的接液盘连接的管道输送到冲洗废液桶,废液桶中废液返回烘干系统继续进行烘干处理。系统烘干过程产生的水蒸气通过一级汽液分离器后,分离出的液体回流至烘箱内的200 L废液桶。
4. 系统主要设备
4.1. 烘箱本体
烘箱本体位于烘干间内,烘箱体和外壳均采用不锈钢304制作,工作室和外壳之间填充隔热层,使箱体外表面温度低于45℃。
烘箱体设置升降密封门,设有行程控制,并设置密封压紧装置。密封圈应选用无毒、无味、耐腐蚀、耐热且不脱落微粒的材料制作 [6] 。
烘箱体上设有就地指示的温度和压力仪表。
烘箱顶部设置进排气口,进气口设置调节阀,与系统排气连锁,以保证系统压差。
烘箱内壁、分风板等采用不锈钢材料制造。
烘箱内允许的温度均匀度为允差 ± 3℃。
浓缩液烘箱与基础连接方式采用基础预埋钢板,焊接地脚螺栓形式。
4.2. 红外加热装置
烘干系统红外加热装置位于管道阀门间机架上,与烘箱采用管道连接。红外加热装置采用防爆型,设备设计12支加热管,每只加热管功率3 KW,每三只加热管为一组,每只加热管采用一只固态继电器控制 [7] [8] ,有利于分组控制。
红外加热管设定为以烘箱内温度来控制加热管的启动和加热管的启动数量。
4.3. 循环风机
循环风机选用烘箱专用轴流风机,易拆卸并便于吹扫或冲洗,安装于管道阀门间机架上。
4.4. 冷凝器与冷水机组
热空气经过湿物料时,物料中部分水会进入热空气中形成湿热空气,部分湿热空气在冷却风机的抽吸作用下,经过冷凝器进行热交换,使湿热空气温度降低,冷凝成20℃饱和状态的气液混合体。
冷凝器采用列管式,热空气走管程,冷却水走壳程。
4.5. 气液分离器
气液分离器采用的分离结构为离心分离。由于气体与液体的密度不同,将液体与气体混合一起高速旋转流动时,液体受到的离心力大于气体,所以液体有离心分离的倾向,液体附着在分离壁面上由于重力的作用向下汇集到一起,通过排放管排出 [9] 。
4.6. 冷凝液收集罐
冷凝液最终被收集在200 L的冷凝液储罐中,通过液位控制,在达到一定的储量时,冷凝液通过泵或者自流至特下水槽中。在收集罐中设置液位显示,用于检测烘箱的蒸发速率,判断浓缩液烘干效果。
4.7. 冷却风机
冷却风机在烘干时将冷凝气体排入房间通风系统,冷却风机电机配置变频装置。冷却风机同时维持烘箱内一定的负压,约低于房间室内压力约100 Pa。
5. 系统组装、调试和试验
在电厂浓缩液桶内干燥装置设计的基础上建立了电厂浓缩液桶内干燥系统。
5.1. 系统调试
5.1.1. 单机调试
单机调试内容及结果见表1。
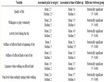
Table 1. Single-machine debugging content and results
表1. 单机调试内容及结果
5.1.2. 单元调试
在单机调试的基础上,分别进行浓缩液干燥装置接收和就位单元、系统预热单元、烘干单元、冷却单元、烘干废物移除单元、高压除盐水冲洗及回流单元等单元的调试。通过单元调试熟练掌握了浓缩液桶内干燥系统各部件的操作,获得了装置初步控制参数。单元调试内容及结果见表2。
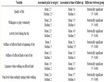
Table 2. Unit debugging content and results
表2. 单元调试内容及结果
5.2. 全流程试验
浓缩液桶内干燥系统调试完成后,利用初始含水量86.35%的模拟浓缩液进行2次全流程验证试验,验证试验数据见表3。
试验1水分蒸发率最小6.13 L/h−1,最大8.64 L/h−1,平均7.38 L/h−1;试验2水分蒸发率最小5.03 L/h−1,最大11.21 L/h−1,平均8.12 L/h−1。达到了水分蒸发率为7.5 L/h−1的系统目标值。
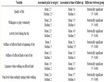
Table 3. Validation of experimental data
表3. 验证试验数据
验证试验干燥后产物见图2所示,干燥产物表面平整,未出现大量缝隙和孔洞。
干燥产物剖开干燥产物时未出现粉碎掉落现象,说明使用红外线加热受热是较均匀的。将试验1干燥产物取样沿如图3所示轴向剖开经行分布取样,测定含水率分布。结果表明了含水率呈现中心高四周低的分布趋势。中心和四周平均含水率分别是11.27%和7.33%,两次试验总体含水率平均值为10.115%。
通过上述实验表明电厂浓缩液桶内干燥装置及工艺干燥处理模拟浓缩液是切实可行的。
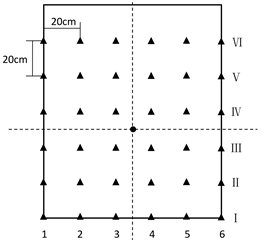
Figure 3. Test 1 the water content distribution of the sampling point was determined after drying
图3. 试验–干燥后产物含水率测定取样点含水率分布
6. 结论
经实验证明本系统待负压稳定后,再升高干燥温度到320~380℃,蒸发速率平均可达10 L/h,减容比平均为4.7,干燥后产物平均含水率为10.115%。达到预期设计目标水分蒸发率 ≤ 8 L/h−1,减容比 ≤ 15,产物含水率 ≤ 15%。本系统设置的干燥箱使用红外加热器,并在排出蒸汽时,在冷凝器的前后端各设有一个气液分离器,把排出气体中的水分充分析出,同时,为了保持干燥箱内的清洁,由喷水管注入水,清洗水经冲洗液箱收集,再由回水管流回到干燥箱内的料桶中做干燥处理。在现有技术背景下,在考虑使用寿命的前提下,本系统比其他传统系统更加节约成本。浓缩液桶内干燥系统的推广和应用,是解决电力行业浓缩液烘干时存在能耗高、易起泡、结垢、爆炸等行之有效的方案。
NOTES
*通讯作者。